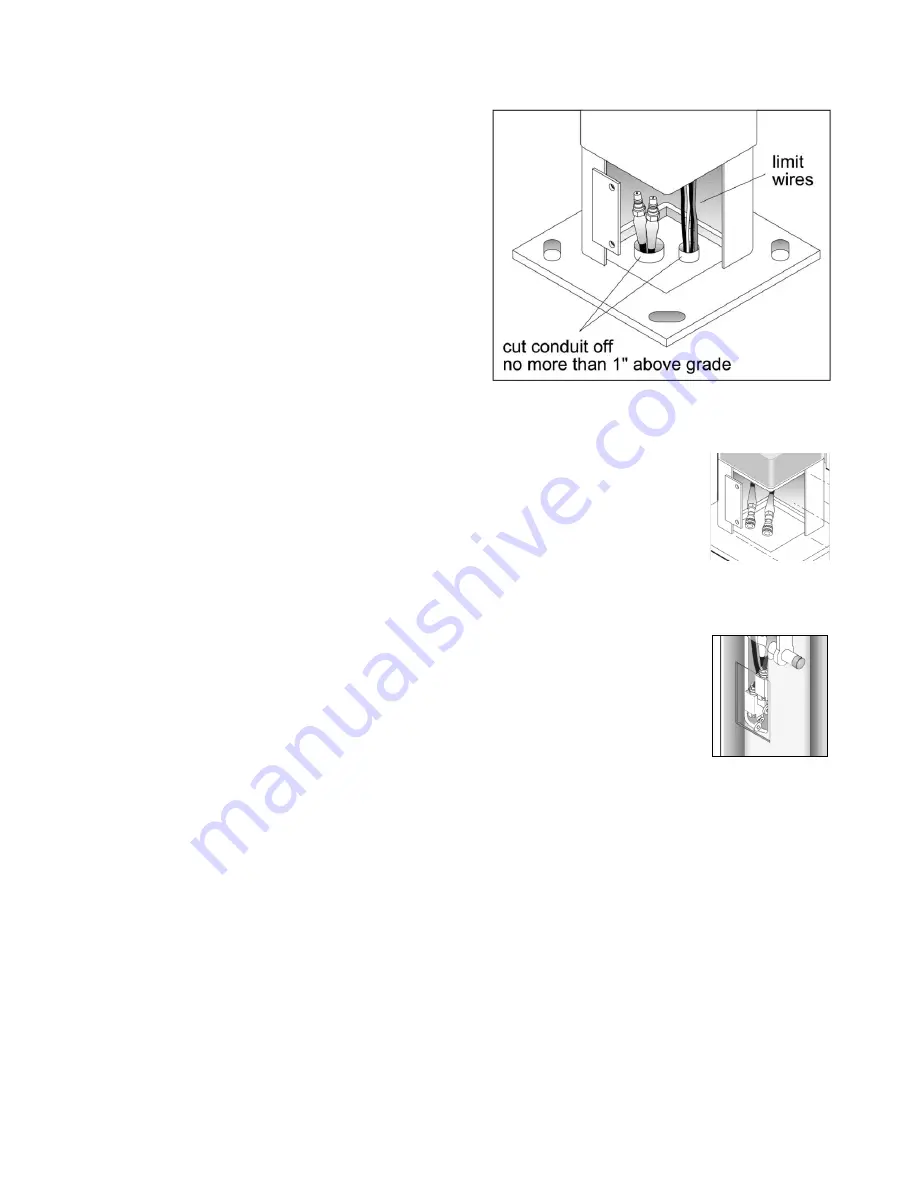
Installation and Maintenance Manual
18
limit switches
limit switches
3) Typical conduits required at the control panel
a) High voltage wires: (120, 208, 240) single
phase or (208, 240, 480) three phase, or
24VDC from Batteries. Refer to
Wiring and
Control Configuration for DC Operators
.
NOTE
: 120 VAC not available on 2HP models
b)
2‖ conduit (with swept elbows) to the hydraulic
post(s) for hoses.
c)
3/4‖ conduit to the post(s) for limit switches.
d) Access control wires (Keypads, telephone entry
systems or any access control devices)
e) Loop wires for vehicle detectors
f) Other accessories such as warning lights etc.
4)
Mount or install all control wiring.
Loops, access
controls, and entrapment protection sensors are
aspects involved with control wiring.
5) Pull and connect all wires and hydraulic hoses
a) Pull four wires, 18 gauge minimum, for the limit switches from control panel to
junction area in the base of the operator post(s). This may be either by
underground conduit or by a seal-tight conduit into the side of the base.
b)
Remove the lower cover (at 2’ height) on the post(s) to expose the limit
switches and connect the limit switch wires. The open limit switch is on the left
and lower down than the close limit switch. Connect these wires to the control
box at the five pole terminal strip marked open limit and close limit.
c) HRG operators normally do not ship with the hydraulic hoses included, until the
exact length is specified by the installer. Refer to the HySecurity
Price Book
for
the correct length before ordering.
d) For protection, tape the ends and pull the hoses through the 2" conduit from
each post to the controller box. Connect the hoses to the couplings, being
certain to match the color coded ends. Also be certain that the connectors are
firmly snapped together.
e) Remove the steel or red plastic shipping plug on the pump and replace it with
the breather cap provided. (See
Instructions for Hand Pump or Manual
Operation
.)
f) Connect the electrical power wiring to the loose wires from the On/Off switch
and a grounding wire to the lower left corner of the electrical panel. Be certain
the labeled voltage and phase of the operator matches the available supply. At a minimum, a 20 amp
circuit (protected with a 20 Amp Inverse Time Breaker) should be provided. Also be sure the operator
is electrically well grounded per NEC Article 250 and local codes.
Also be certain to oversize the
branch circuit wires to allow for voltage drop, especially for single-phase machines. See the wire size
schedules in the appendix. Machines operating on high voltages (above 120 VAC) do not need a
neutral wire.
g) Verify that the primary tap of the control transformer is connected to match the supplied voltage. It is
especially important to distinguish between 208 and 230 volt supplies. The various voltage taps are
identified by a label on the transformer.
6) Test and Adjust the Operator (See Smart Touch Setup First)
a) Test basic functions of the operator first, before connecting any external control wiring. If your operator
is equipped with vehicle detectors, be certain that they are connected to a loop or unplugged so that
they do not cause interference with the function of the machine. If the motor turns, but nothing moves,
on a three phase power source, reverse two wires. Also, be certain that the hose quick connectors are
firmly engaged.
b) After testing the basic functions, add accessories and external control wiring. Fully test the
operator functions again.
Access panel at
operator base
Access panel at
operator base
Summary of Contents for SwingRiser 14
Page 2: ......
Page 18: ...Installation and Maintenance Manual 8 Tools Required for an Efficient Installation ...
Page 19: ...Installation and Maintenance Manual 9 Swing Gate Post Details ...
Page 20: ...Installation and Maintenance Manual 10 Swing Gate Post Details continued ...
Page 21: ...Installation and Maintenance Manual 11 Swing Gate Post Details continued ...
Page 22: ...Installation and Maintenance Manual 12 HRG 220 Pump Pack ...
Page 23: ...Installation and Maintenance Manual 13 HRG 222 Pump Pack ...
Page 24: ...Installation and Maintenance Manual 14 How Our Hydraulic Swing Gates Work ...
Page 32: ...Installation and Maintenance Manual 22 ...
Page 54: ...Installation and Maintenance Manual 44 Loop Layouts ...
Page 77: ...Installation and Maintenance Manual 67 ...
Page 83: ...Installation and Maintenance Manual 73 Smart Touch Controller Connections ...