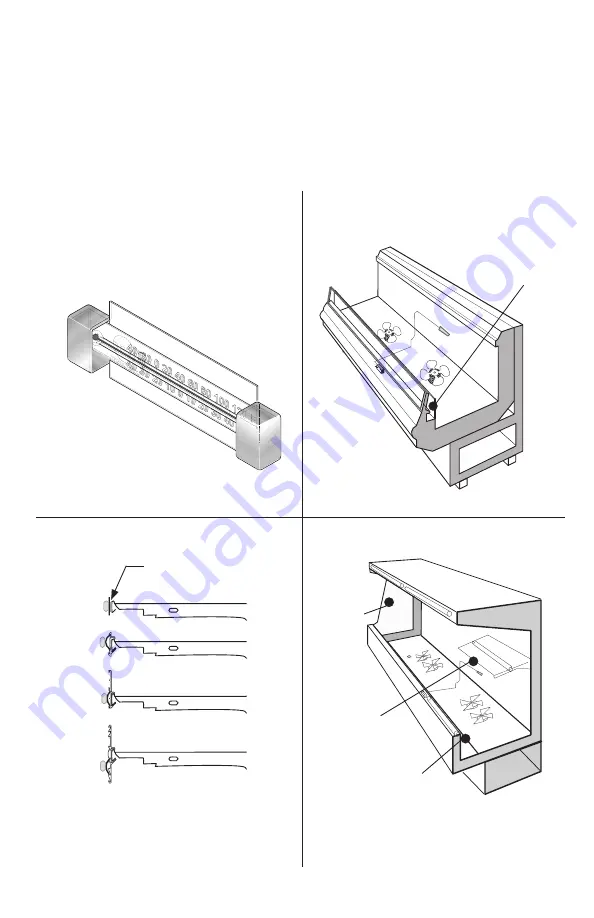
P/N 3053328_C 4-5
Reach-In
HUSSMANN CORPORATION • BRIDGETON, MO 63044-2483 U.S.A.
This is an NSF-7 &
US FDA Food Code
Required
Thermometer
Hussmann P/N 0429971_C
10/2007
Hussmann Corporation • 12999 St. Charles Rock Road • Bridgeton, MO 63044-2483
U.S. & Canada 1-800-922-1919 • Mexico 1-800-890-2900E • www.hussmann.com
© 2007 Hussmann Corporation
Thermometer — Hussmann Part TM.4911251
INSTALLING FDA/NSF REQUIRED
THERMOMETER
The following pages provide the same information that ships with the thermometer. This requirement does not
apply to display refrigerators intended for bulk produce (refer to Page 1-1). Please note that the tape cannot
be exposed after installation.
This is an NSF-7 &
US FDA Food Code
Required
Thermometer
Suggested Mounting Locations in
Single Deck Glass Front Impact
Merchandisers
– Acrylic Package
Guard, Facing Out
– Inside
End Panel
– Shelf
Price Tag
Molding
– Return Air Grille
Suggested Mounting Locations in
Multi-deck Merchandisers
Hussmann P/N 0429971_C
10/2007
Flexible Plastic
Fits in Price Tag
Moldings
Double Stick Tape
Thermometer – Hussmann Part TM.4911251
Hussmann Corporation • 12999 St. Charles Rock Road • Bridgeton, MO 63044-2483 U.S. & Canada
1-800-922-1919 • Mexico 1-800-890-2900 • www.hussmann.com
© 2007 Hussmann Corporation