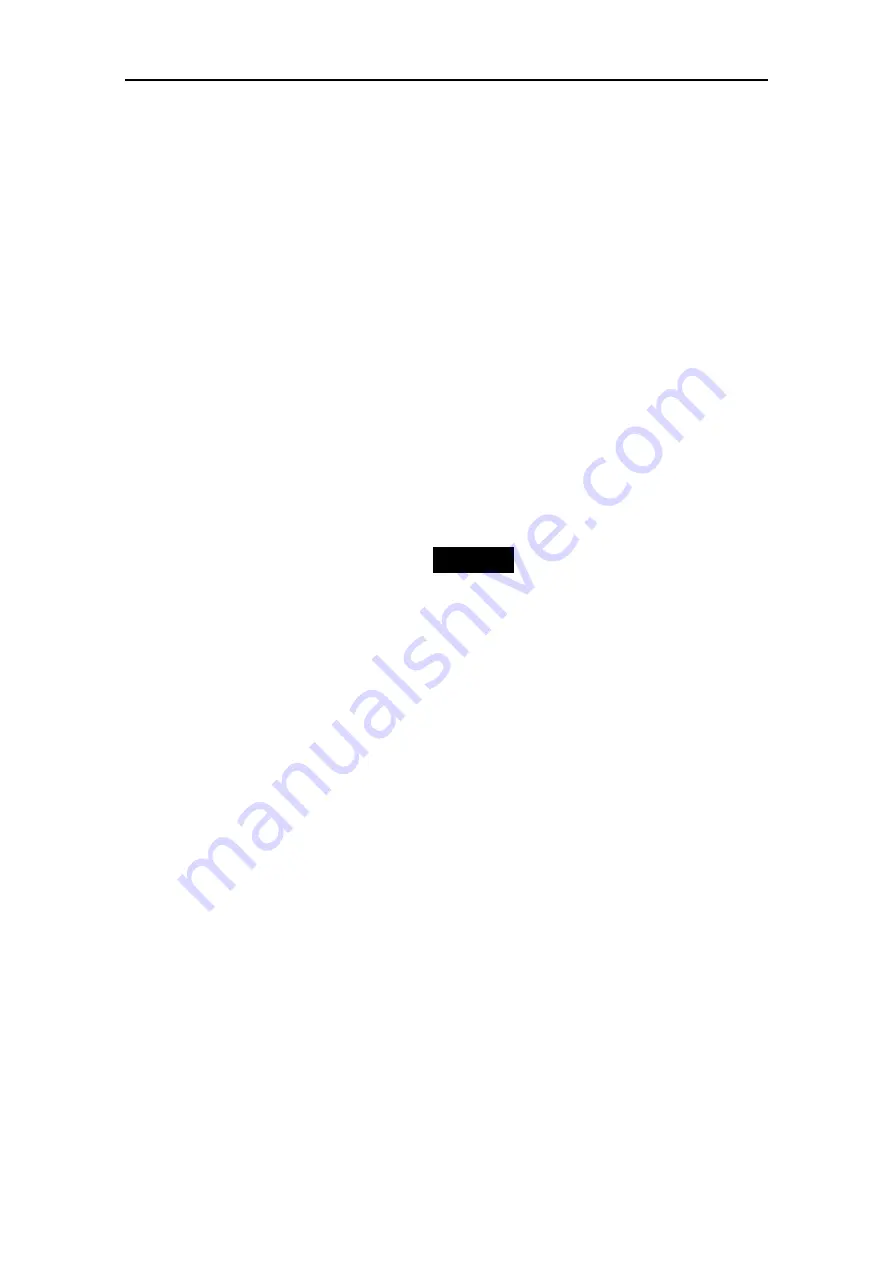
MAINTENANCE AND ADJUSTMENT OF THE EV
33
Serial and identification numbers are stamped on various locations on the frame
motor and controller. Record these numbers in the Quick Reference Data section in the
front of the manual. Have these numbers available when ordering parts.
FASTENERS
Proper fastener selection and installation is important to ensure the motorcycle
operates as designed and can be serviced efficiently. The choice of original equipment
fasteners is not arrived at by chance. Make sure replacement fasteners meet all the
same requirements as the originals
Many screws. Bolts and studs are combined with nuts to secure particular
components. to indicate the size of a nut. Manufactures specify the internal diameter
and the thread pitch
The measurement across two flats on a nut or bolt indicates the wrench size
WARNING
Do not install fasteners with a
strength classification lower than
what was originally installed by the
manufacturer doing so may cause
equipment failure and or damage
Torque Specifications
The material used in the manufacturing of the
EV
may be subjected to uneven
stresses if the fasteners of the various subassemblies are not installed and tightened
correctly. Fasteners that are improperly installed or work loose can cause extensive
damage. it is essential to use an accurate torque wrench as described in this chapter
Self-Locking Fasteners
Several types of bolts. Screws and nuts incorporate a system that creates
interference between the two fasteners. Interference is achieved in various ways. The
most common types are the nylon insert nut and a dry adhesive coating on the threads
of a blot.
Self-locking fasteners offer greater holding strength than standard fasteners, which
improves their resistance to vibration. All self-locking fasteners cannot be reused. The
Summary of Contents for HS5DUTV-2
Page 25: ...GENERAL INFORMATION 25 IDENTIFICATION CODE Frame No...
Page 69: ...MAINTENANCE AND ADJUSTMENT OF THE EV 69 Periodic Service Schedule...
Page 108: ...MAINTENANCE AND ADJUSTMENT OF THE EV 108...
Page 130: ...MAINTENANCE AND ADJUSTMENT OF THE EV 130...
Page 137: ...ENGINE 137...
Page 146: ...ENGINE 146 No Part Name Remarks 1 Binding post 2 Output shaft 3 Socket connector 4 Bearing...
Page 148: ...ENGINE 148...
Page 151: ...ENGINE 151 No Part Name Qty Remarks 1 Charger 1 2 Battery Assy 1...
Page 164: ...CHASSIS 164 PANEL AND CARGO BED Front Panel...
Page 168: ...CHASSIS 168...
Page 175: ...CHASSIS 175...
Page 182: ...CHASSIS 182 28 Rear right side reflector 1 29 Washer 6 18 1 6 2...
Page 184: ...CHASSIS 184...
Page 192: ...CHASSIS 192 8 Dustproof cover1 2 9 Hex nut M14 1 25 2 10 Steering ball head components 2...
Page 200: ...CHASSIS 200 4 Check steering joint Crack distortion Replace BRAKE SYSTEM...
Page 206: ...CHASSIS 206 33 Hexagon Flange Bolt M12 1 25 2 34 Cylindrical Bush 12 5 22 55 2...
Page 208: ...CHASSIS 208...
Page 214: ...CHASSIS 214...
Page 218: ...CHASSIS 218...
Page 220: ...CHASSIS 220...
Page 222: ...CHASSIS 222...
Page 226: ...CHASSIS 226...
Page 227: ...CHASSIS 227 3 Install brake pad NOTE 4 Install brake pad holding bolts 17Nm 1 7 m kg 12 ft lb...
Page 228: ...CHASSIS 228...
Page 230: ...CHASSIS 230...
Page 239: ...CHASSIS 239...
Page 241: ...CHASSIS 241 TRANSMISSION SYSTEM...
Page 243: ...CHASSIS 243 Front Bridge...
Page 245: ...CHASSIS 245...
Page 247: ...CHASSIS 247...
Page 249: ...CHASSIS 249...
Page 251: ...CHASSIS 251...
Page 253: ...CHASSIS 253...
Page 255: ...CHASSIS 255 Front Transmission Axle Assy...
Page 257: ...ELECTRICAL COMPONENTS 257...
Page 260: ...ELECTRICAL COMPONENTS 260...
Page 264: ...ELECTRICAL COMPONENTS 264 C V Axle Rear Axle...
Page 266: ...ELECTRICAL COMPONENTS 266...
Page 268: ...ELECTRICAL COMPONENTS 268...
Page 270: ...ELECTRICAL COMPONENTS 270...
Page 272: ...ELECTRICAL COMPONENTS 272...
Page 274: ...ELECTRICAL COMPONENTS 274...
Page 277: ...ELECTRICAL COMPONENTS 277 Shift Operating System...
Page 281: ...ELECTRICAL COMPONENTS 281 Reverse mechanism parts...
Page 283: ...ELECTRICAL COMPONENTS 283 Reverse mechanism parts...
Page 285: ...ELECTRICAL COMPONENTS 285 SUSPENSION...
Page 294: ...ELECTRICAL COMPONENTS 294 Rear Suspension...
Page 302: ...ELECTRICAL COMPONENTS 302 Nut 45 Nm 4 5 m kg 32 ft lb...
Page 321: ...ELECTRICAL COMPONENTS 294 CHARGING SYSTEM CIRCUIT DIAGRAM see 337 page...
Page 325: ...ELECTRICAL COMPONENTS 298 TROUBLESHOOTING IF THE HEADLIGHT AND OR TAILLIGHT FAIL TO COME ON...
Page 330: ...ELECTRICAL COMPONENTS 303 SIGNALING SYSTEM CIRCUIT DIAGRAM see 337 page...
Page 336: ...FOREWORD 309...
Page 338: ...FOREWORD 311...
Page 340: ...FOREWORD 313...
Page 341: ...FOREWORD 314 7 If the four wheel drive indicator light fails to come on...
Page 345: ...FOREWORD 318 SCHECKING THE SWITCH...
Page 346: ...FOREWORD 319...
Page 347: ...FOREWORD 320...