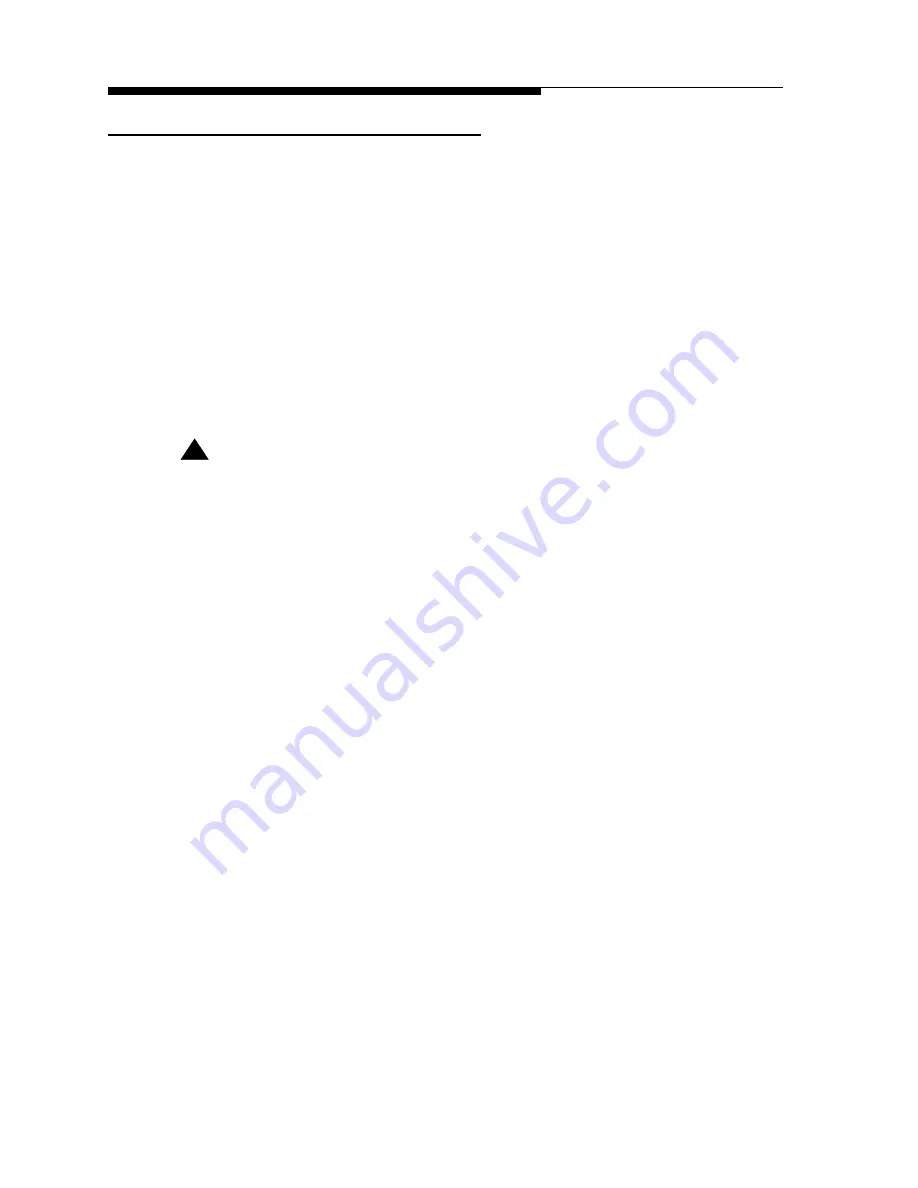
3/6/08
888-2463-001
A-9
WARNING: Disconnect primary power prior to servicing.
Appendix A Cutting and Soldering
Diamond Series™
1.4.1
Soldering Procedure
a.
The line should be free of burrs. The outer corner may be beveled slightly to
make assembly of flange easier. See Figure A-8.
b.
Emery cloth should be used to clean the outside of the line where it will meet the
flange. Also clean the inner surface of the flange with emery cloth.
c.
Insert the solder ring into the groove on the flange. If solder rings are not included
with the flange, they can be made from .062-inch diameter silver solder wire (30-
45% silver).
d.
Apply a thin coat of flux to the line and to the flange.
e.
Slide the flange onto the end of the outer conductor.
!
WARNING:
SKIN BURN HAZARD. TEMPERATURE OF THE HEATED LINE IN THE FOLLOWING
STEPS IS QUITE HIGH AND PRECAUTIONS MUST BE TAKEN TO AVOID CONTACT
WITH EXPOSED SKIN.
f.
Stand the line on end (vertical) for soldering (flange to be soldered pointing
down). Ensure that the flange remains square with the outer conductor.
g.
Using a #3 or #4 torch tip, heat the entire circumference of the line and flange.
Keep the torch moving and heat 2 or 3 inches of the line/flange at a time. Aim the
torch at the copper just above the crack between the flange and the line. This will
minimize the need for fill solder. If the brass flange is heated more than the cop-
per line, the flange will expand and create an unnecessary gap to fill with solder.
Use caution. There is a fine line between melting the solder and melting the brass
flange or burning a hole in the copper. The solder will pull up into the joint from
the solder ring by capillary action. Once it starts to flow, do not stop until the
entire circumference of the joint has solder appearing in it. If the solder from the
internal solder ring does not “wick up” and become visible at the joint after a few
minutes, a small amount of solder can be applied to the joint to enhance the heat
transfer. See Figure A-9.