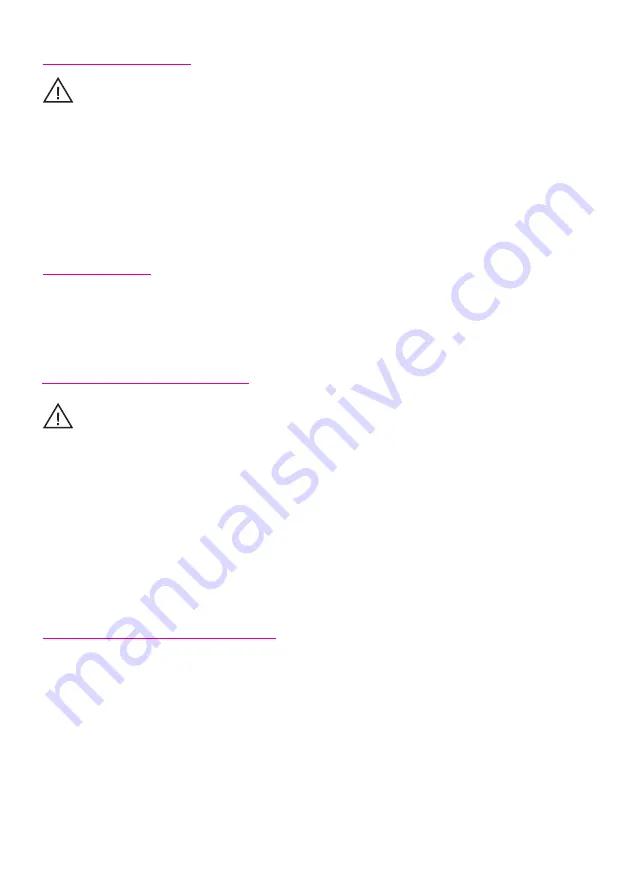
34
1003370 05/2016 V01
3.13.2 Switching in the motor cable
Attention!
Switching in the motor cable must take place with the power cut and the power stage disabled, as otherwise problems
such as burned-off contactor contacts may occur. In order to ensure unpowered switch-on, you must make sure that
the contacts of the motor contactor are closed before the drive controller power stage is enabled. At the moment the
contactor is switched off it is necessary for the contact to remain closed until the drive controller power stage is shut
down and the motor current is 0. This is done by inserting appropriate safety times for switching of the motor contac-
tor in the control sequence of your machine.
Despite these measures, the possibility cannot be ruled out that the drive controller may malfunction during switching
in the motor cable.
3.14 Braking resistor (RB)
In regenerative operation, e.g. when braking the drive, the motor feeds energy back to the drive controller. This
increases the voltage in the DC link. If the voltage exceeds a threshold value, the internal braking transistor is
activated and the regenerated power is converted into heat by means of a braking resistor.
3.14.1 Protection in case of braking chopper fault
Attention!
If the internal braking chopper transistor is permanently switched on, because it is alloyed through by overload
(= 0 Ω), there is a protective function to protect the device against overheating.
You activate this function by assigning any digital output (DriveManager 5
►
subject area “Configuration of the
inputs/outputs”
►
Digital outputs
►
OSD00 to OSD02) to BC_FAIL(56). In the event of a fault the selected output
then switches from 24 V to 0 V. This signal can be used to disconnect the drive controller from the mains supply.
For detailed information on parameterization refer to the Operating Manual YukonDrive®.
3.14.2 Design with integrated braking resistor (BG3+4)
The catalogue only specifies the peak braking power for the drive controllers with integrated braking resistor. The
permissible continuous braking power must be calculated. It depends on the effective loading of the controller in the
corresponding application.
The drive controller is thermally designed in such a way that no energy input by the internal braking resistor is permit-
ted during continuous operation with rated current and at maximum ambient temperature.
Consequently, a controller design featuring an integrated braking resistor only makes sense when the effective drive
controller load is ≤ 80 % or the braking resistor is designed for one-off emergency stop. In the event of an emergency
stop, only the heat capacity of the braking resistor can be used for a one-off braking action. The permissible energy
W
IBr
can be taken from the following table.