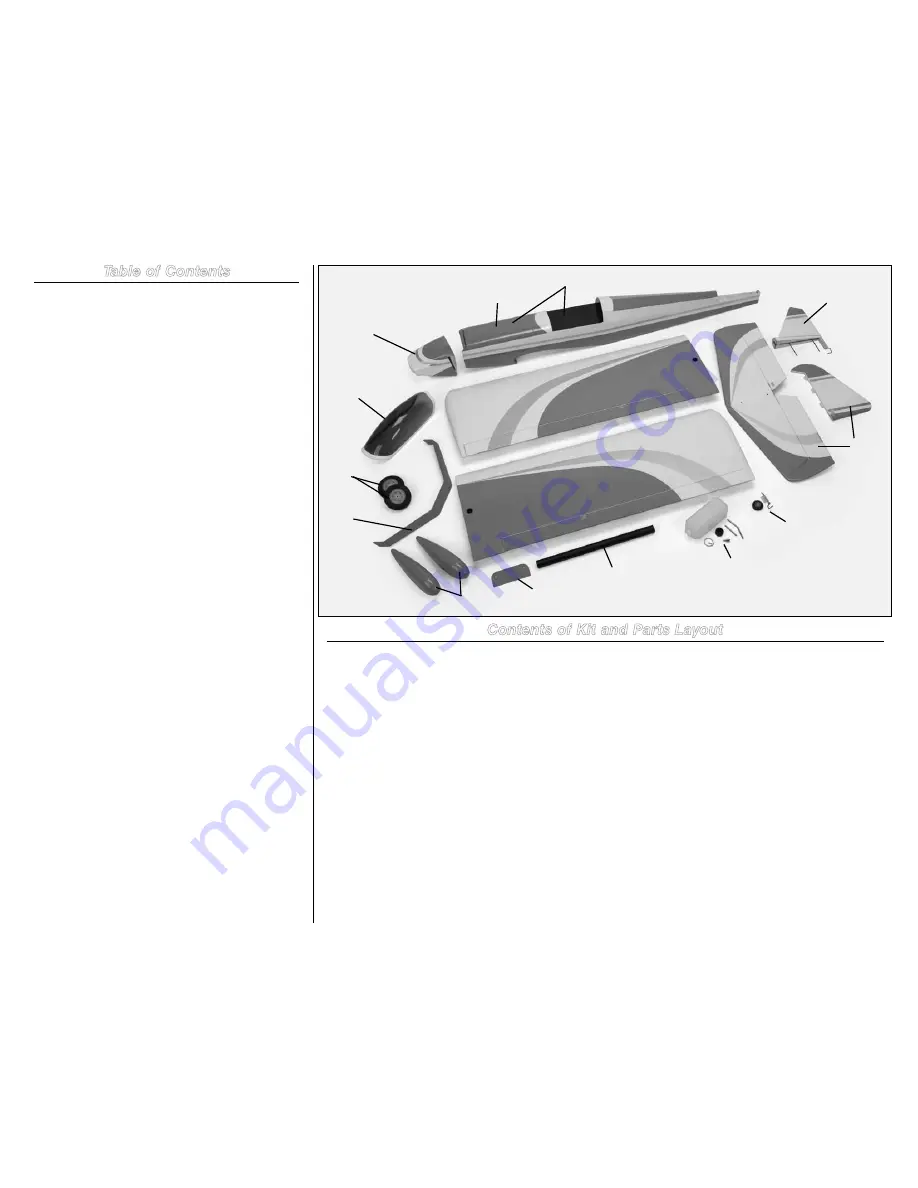
2
Hangar 9 Pulse 125 ARF Assembly Manual
Table of Contents
Contents of Kit and Parts Layout ......................................2
Included Parts Listing .......................................................3
Using the Manual ..............................................................4
Important Information Regarding Warranty Information ..4
UltraCote® Covering Colors .............................................4
Before Starting Assembly .................................................4
Transmitter Requirements.................................................4
Radio Equipment Requirements .......................................4
Recommended Setup–2-Stroke Glow ...............................4
Recommended Setup–4-Stroke Glow ...............................4
Recommended Setup–4-Stroke Gas .................................4
Recommended Setup–Electric Power (EP) .......................4
Field Equipment Required .................................................4
Optional Field Equipment ..................................................4
Additional Required Tools .................................................5
Additional Required Adhesives .........................................5
FS One® ...........................................................................5
Rudder and Fin Preparation ..............................................5
Tail Installation ..................................................................7
Radio Installation ..............................................................8
Aileron Servo Installation ................................................11
Landing Gear and Wheel Installation ..............................13
Four-Stroke Engine Installation .......................................15
Two-Stroke Engine Installation .......................................19
Fuel Tank Installation ......................................................23
Cowling and Spinner Installation - Four-Stroke Engine ..25
Cowling and Spinner Installation - Two-Stroke Engine ...27
Electric Motor Installation ...............................................29
Cowling and Spinner Installation - Electric Motor...........31
Final Assembly ................................................................32
Center of Gravity .............................................................34
Control Throws ...............................................................34
Flight Preparations ..........................................................35
Safety Do’s and Don’ts for Pilots ....................................35
Daily Flight Checks ..........................................................35
Age Requirements ..........................................................36
Safety, Precautions and Warnings ..................................36
Warranty Information ......................................................36
CE Compliance Information for the European Union ......37
2009 Official Academy of
Model Aeronautics Safety Code ................................38
Engine Mounting Template .............................................39
Replacement Parts
1. HAN517001
Fuselage with Hatch
2. HAN517002
Fuselage Hatch
3. HAN517003
Left Wing Panel
4. HAN517004
Right Wing Panel
5. HAN517005
Horizontal and Vertical Stabilizer
6. HAN517006
Canopy
7. HAN517007
Cowl
8. HAN517008
Landing Gear, with Axles
9. HAN517010
Wing Tube
10. HAN517011
Wheelpants (2)
11. HAN517012
Main Wheels
12. HAN517015
Fuel Tank
13. HAN517017
Tailwheel Assembly
14. HAN517018
Wing Bolt Plate
Items not shown:
HAN517009
Landing Gear Axles
HAN517013
Engine Mount
HAN517014
EP Motor Mount
HAN517016
Hardware Package
HAN517019
Wing Mounting Nylon Bolts
Contents of Kit and Parts Layout
1
2
3
4
5
5
6
7
8
9
14
10
11
12
13