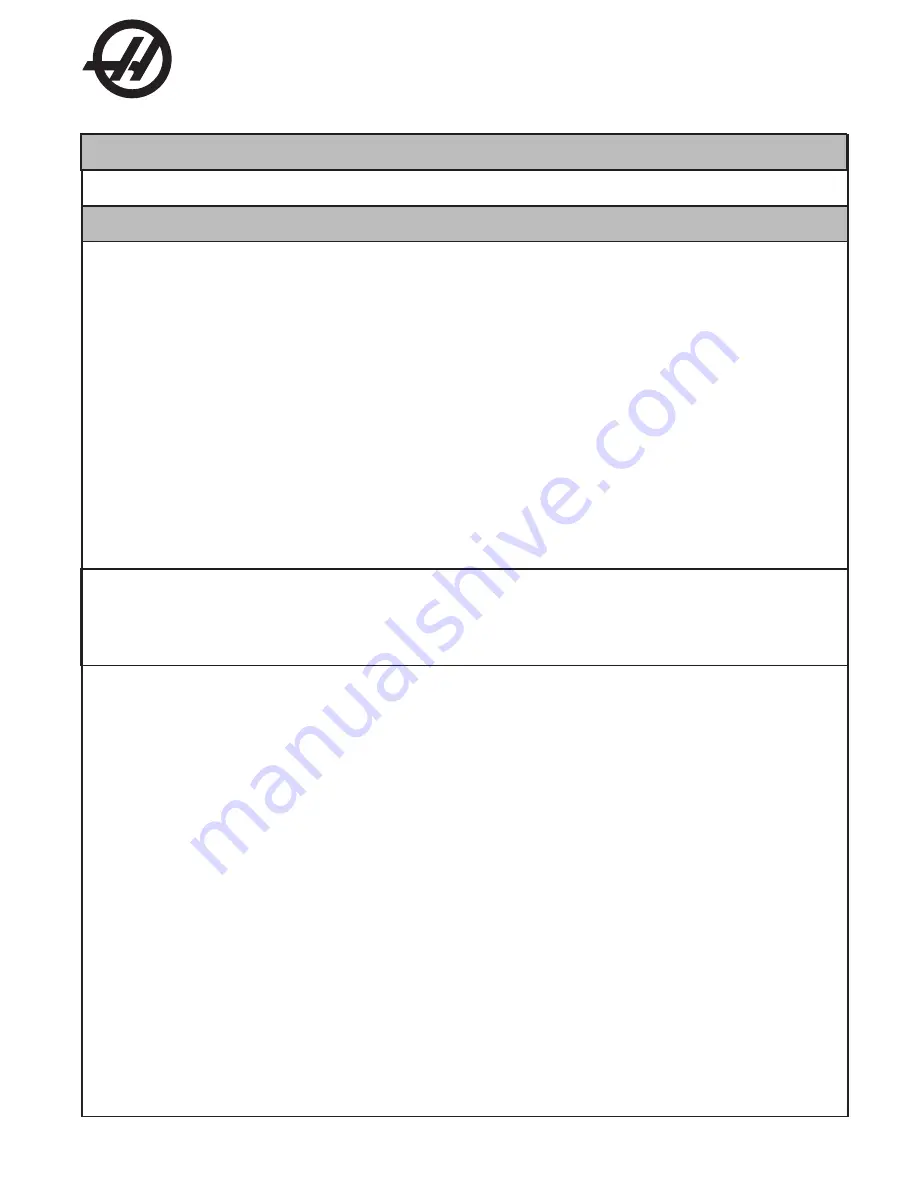
Haas Technical Publications
Manual_Archive_Cover_Page Rev A
June 6, 2013
•
This content is for illustrative purposes.
•
Historic machine Service Manuals are posted here to provide information for Haas machine owners.
•
Publications are intended for use only with machines built at the time of original publication.
•
As machine designs change the content of these publications can become obsolete.
•
You should not do mechanical or electrical machine repairs or service procedures unless you are qualified
and knowledgeable about the processes.
•
Only authorized personnel with the proper training and certification should do many repair procedures.
HAAS SERVICE AND OPERATOR MANUAL ARCHIVE
WARNING: Some mechanical and electrical service procedures can be
extremely dangerous or life-threatening.
Know your skill level and abilities.
All information herein is provided as a courtesy for Haas machine owners
for reference and illustrative purposes only. Haas Automation cannot be held
responsible for repairs you perform. Only those services and repairs that are
provided by authorized Haas Factory Outlet distributors are guaranteed.
Only an authorized Haas Factory Outlet distributor should service or repair a
Haas machine that is protected by the original factory warranty. Servicing by
any other party automatically voids the factory warranty.
HRT Operator Manual 96-5047 RevL English June 2005
Summary of Contents for HRT 160
Page 9: ...8 96 5047 rev L June 2005 HRT210SHS MACHINE DIMENSIONS ...
Page 55: ...54 96 5047 rev L June 2005 9 HRT ASSEMBLY DRAWINGS ...
Page 58: ...57 96 5047 rev L June 2005 ...
Page 59: ...58 96 5047 rev L June 2005 ...
Page 61: ...60 96 5047 rev L June 2005 ...
Page 62: ...61 96 5047 rev L June 2005 ...
Page 63: ...62 96 5047 rev L June 2005 ...
Page 64: ...63 96 5047 rev L June 2005 ...