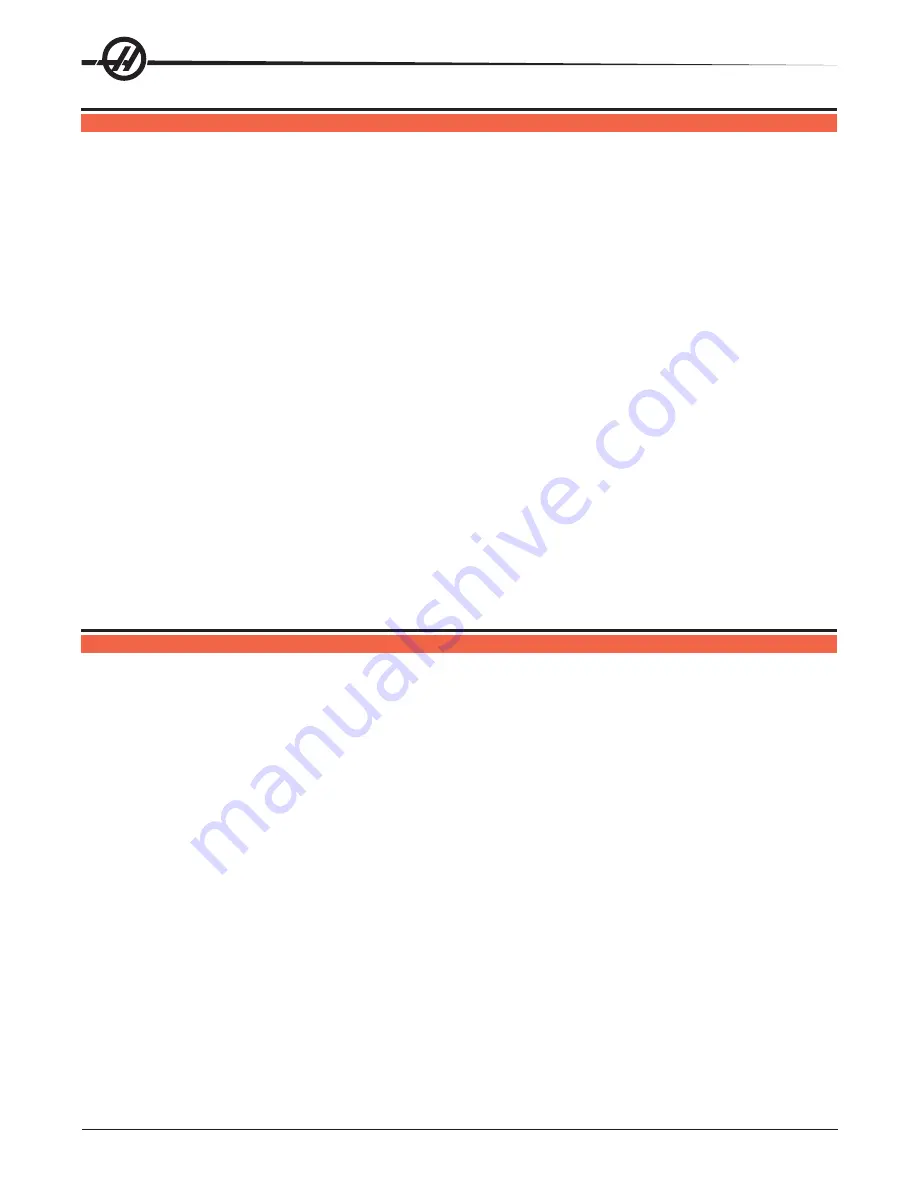
30
96-5047 rev L June 2005
4.3 E
NTERING
A S
TEP
To enter a step into the controller's memory, press the MODE button. This will put the controller into the
PROGRAM mode. The display will begin blinking and show a step size. Clear the last program by pressing and
holding the CLR key for three seconds. To enter a 45 degree (45
o
) step, press the following keys:
4 5 0 0 0
The display should now indicate:
01 45.000
Press the right arrow button. This will cause the 45 degree (45
o
) step to be stored and the feed rate to be
displayed. To enter a feed rate of 80 degrees (80
o
) per second, press the following keys:
8 0 0 0 0
The display should now indicate:
01 F 80.000
To return the controller to the RUN mode, press the MODE button. The display should now indicate:
01 P 000.000
Start the 45 degree (45
o
) step by pressing the CYCLE START button. The table should move to the new
position and at the end of the step, the display should indicate:
01 P045.000
4.4 P
UTTING
A P
ROGRAM
I
NTO
M
EMORY
Programming begins with ensuring that the controller is in PROGRAM mode and at step number 01. To do this,
press the MODE button while the servo is NOT in motion. The displays must be blinking. Next, push and
HOLD the clear (CLR) key for five seconds. You have now cleared the memory and are at step one and ready
to begin programming. “01 000.000 “ should be displayed. Please note that you do not have to clear the
memory each time you wish to enter or change data. Data in the program can be changed simply by writing
the new data over the old.
Up to 7 programs can be stored, numbered 0 to 6. To access a different program, press the minus key while
showing a G code. The display will change to:
Prog n
Press a number key to select a new program and then press the MODE key to return to RUN mode or the
START key to continue with the PROGRAM mode.
Every one of the possible 99 steps in a program may contain the following:
1.
a step size or position command (shown as a number with possible minus sign),
2.
a feed rate shown with a preceding F,
3.
a loop count shown with a preceding L,
4.
a G code shown with a preceding G, and
5.
a jump destination with a preceding Loc.
Every step must contain at least one G code. The following section describes the possible G codes.
Summary of Contents for HRT 160
Page 9: ...8 96 5047 rev L June 2005 HRT210SHS MACHINE DIMENSIONS ...
Page 55: ...54 96 5047 rev L June 2005 9 HRT ASSEMBLY DRAWINGS ...
Page 58: ...57 96 5047 rev L June 2005 ...
Page 59: ...58 96 5047 rev L June 2005 ...
Page 61: ...60 96 5047 rev L June 2005 ...
Page 62: ...61 96 5047 rev L June 2005 ...
Page 63: ...62 96 5047 rev L June 2005 ...
Page 64: ...63 96 5047 rev L June 2005 ...