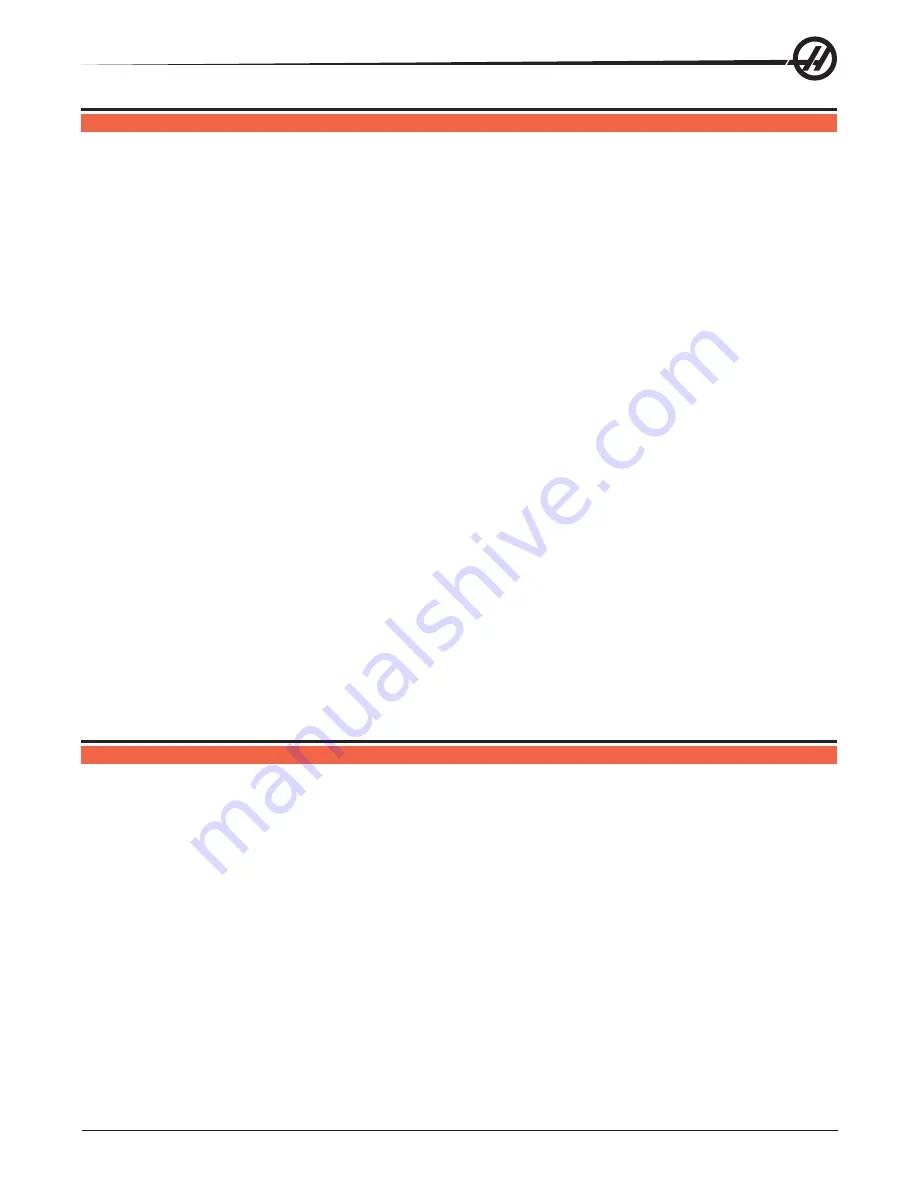
13
96-5047 rev L June 2005
2.2 I
NTERFACING
TO
O
THER
E
QUIPMENT
Semi-Fourth Axis Operation
Interfacing is an unfriendly word that inspires fear in most non-electrical people. In reality, you are interfacing
objects all the time. Hooking up a stereo, computer, or VCR requires many connections, or interfaces. Plug-
ging a lamp into the wall and turning the switch on is really interfacing a 100 watt incandescent lamp up to a 15
Megawatt generating plant. While there are hundreds of connections between your lamp and the power com-
pany, it is really a simple process. The HAAS control is just as simple.
The control can be installed to communicate with your mill two different ways: RS-232 Interface or CNC
Interface Cable. These connections are detailed in the following sections.
The HAAS control has two signals: one input and one output. Your equipment tells the HAAS control to index
(an input), it indexes, and then sends a signal back to your equipment that the index (an output) has been
completed. These signals are simply switch closures, or in mechanical terms, relays. A switch (relay) is closed
inside your machine that tells us to index, we index and then close a switch (relay) inside our control to tell
your machine that we are done. This inferface requires four wires; two for each signal. They are from the remote
input on the back of the HAAS control and from your equipment or CNC (Computer Numerically Controlled)
machine.
The Relay In The HAAS Control
The relay inside the control has a maximum rating of 2 amps at 30 volts D.C./ 120V AC. It is programmed as
either a normally closed or a normally open relay, closed during cycle or after cycle (see "Parameters" sec-
tion). It is intended to drive other logic or small relays. It will not drive other motors, magnetic starters, or loads
exceeding 100 watts. If you use the feedback relay to drive another D.C. relay (or any inductive load), remem-
ber to install a snubber diode across your relay’s coil in the opposite direction of coil current flow. Failure to
use this diode or other arc suppression circuitry on inductive loads, no matter how small they may be, will
result in the contacts of the relay arcing together in a very short time.
To test the relay, use an ohmmeter to measure the resistance across pins 1 and 2. With the control off, the
reading should be infinite. If a lower resistance is measured, the contact points have failed and the relay must
be replaced. Radio Shack sells a relay that can be used as a replacement (Cat. #275-241) but it should only
be replaced by a qualified technician.
2.3 T
HE
RS-232 I
NTERFACE
There are two connectors used for the RS-232 interface. They are both DB-25 connectors, one male and one
female. Multiple controllers are connected by daisy-chaining the boxes. The cable from the computer connects
to the female connector. Another cable can connect the first box to the second by connecting the male connec-
tor of the first box to the female connector of the second. This can be repeated for up to nine controllers.
Since the RS-232 connector on the back of most PC's is a male DB-9, only one type of cable is required for
connection to the controller, or between controllers. This cable must be a DB-25 male on one end and a DB-9
female on the other. Pins 1, 2, 3, 4, 5, 6, 7, 8, and 9 must be wired one-to-one. It cannot be a Null Modem
cable, which inverts pins 2 and 3. To check cable type, use a cable tester to check that communication lines
are correct. The controller is DCE (Data Communication Equipment). This means that it transmits on the RXD
line (pin 3) and receives on the TXD line (pin 2). The RS-232 connector on most PC's is wired for DTE (Data
Terminal Equipment), so no special jumpers should be required.
The Down Line (RS-232 out) DB-25 connector is only used when more than one controller is to be used. The
first controller's down (RS-232 out) line connector goes to the second controller's up (RS-232 in) line connector,
etc.
Summary of Contents for HRT 160
Page 9: ...8 96 5047 rev L June 2005 HRT210SHS MACHINE DIMENSIONS ...
Page 55: ...54 96 5047 rev L June 2005 9 HRT ASSEMBLY DRAWINGS ...
Page 58: ...57 96 5047 rev L June 2005 ...
Page 59: ...58 96 5047 rev L June 2005 ...
Page 61: ...60 96 5047 rev L June 2005 ...
Page 62: ...61 96 5047 rev L June 2005 ...
Page 63: ...62 96 5047 rev L June 2005 ...
Page 64: ...63 96 5047 rev L June 2005 ...