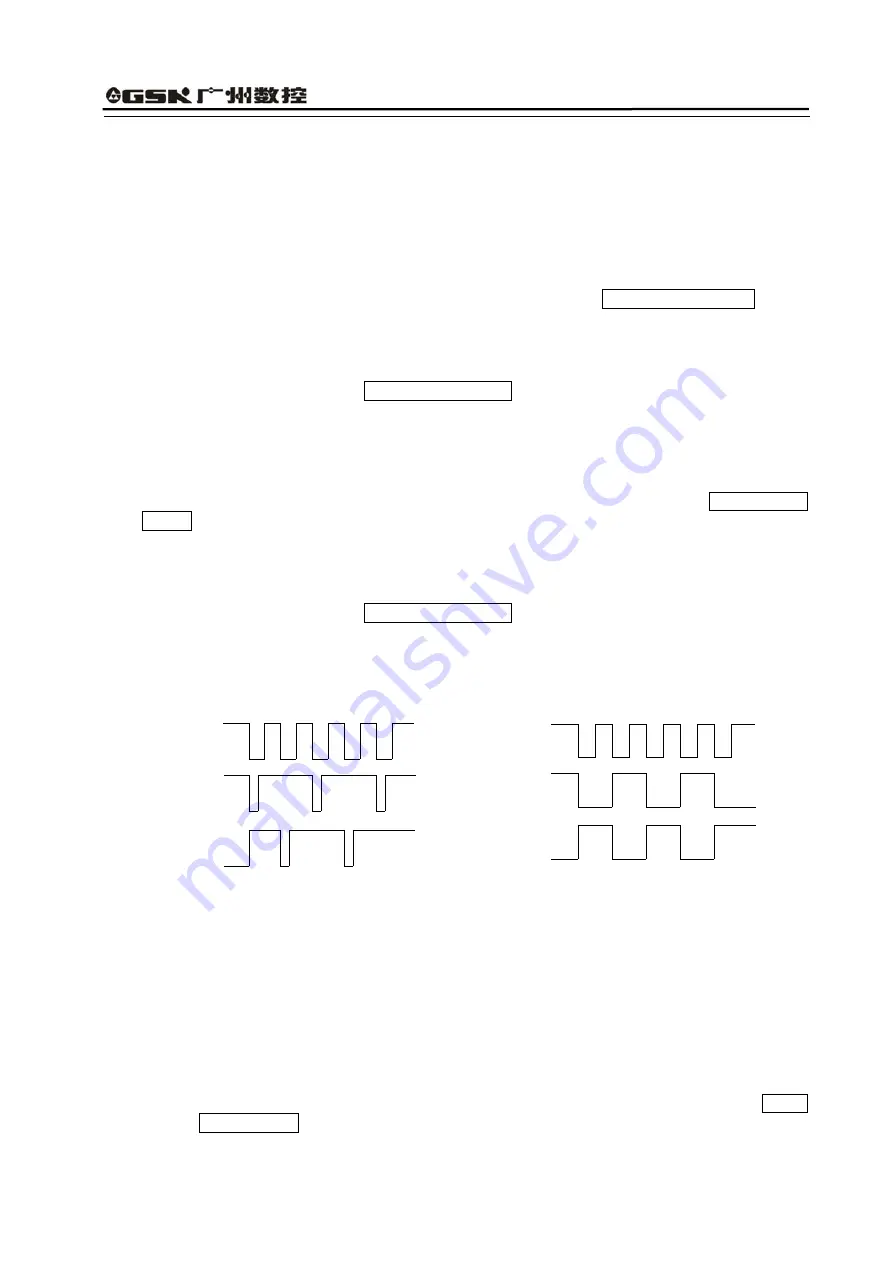
GSK928TE
Ⅱ
Turning CNC System User Manual
45
Bit4=1
:
the hydraulic chuck control signal uses the pulse control; its width is defined by the time
of P15
;
Bit3=0
:
the hydraulic chuck needs to receive the in-position feedback signal
;
Bit3=1
:
the hydraulic chuck does not need to receive the in-position feedback signal.
In outside chuck mode: After M10 is executed, the system outputs the chuck clamping signal
from X 7.19 (the output pulse or the level signal is selected by the parameter) and the chuck
clamping operation ends without needing the in-position feedback signal; when needing the
in-position feedback signal, the chuck clamping operation ends after detecting the in-position of
chuck clamping within 5 seconds, otherwise the system prompts
“
Chuck Ready Failure
”;
After M11 is executed, the system outputs the chuck releasing signal from X 7.18 (the output
pulse or the level signal is selected by the parameter), the chuck releasing operation ends
without needing the in-position feedback signal; when needing the in-position feedback signal,
the chuck releasing operation ends after detecting the chuck releasing in-position signal,
otherwise the system prompts
“
Chuck Ready Failure
”;
In inside chuck mode: after M10 is executed, the system outputs the chuck clamping signal from
X 7.18, (the output pulse or the level signal is selected by the parameter), and the chuck
clamping operation ends without needing the in-position feedback signal; when needing the
in-position feedback signal, the chuck clamping operation ends after detecting the chuck
clamping in-position signal within 5 seconds, otherwise the system prompts
“
Chuck Ready
Failure
”;
After M11 is executed, the system outputs the chuck releasing signal from X 7.19, (the output
pulse or the level signal is selected by the parameter), the chuck releasing operation ends
without needing the in-position feedback signal; when needing the in-position feedback signal,
the chuck releasing operation ends after detecting the chuck releasing in-position signal,
otherwise the system prompts
“
Chuck Ready Failure
”
Besides commands, other ways are employed to control the hydraulic chuck, including the
external pedal switch. The system switches the clamping/releasing by M10/M11 when the pedal
switch is stepped once.
]
Time sequence of pulse control mode Time sequence of level control mode
Note 1:
When the hydraulic chuck control is valid, the previous user input commands
(M91/M92/M93/M94) are invalid; when the hydraulic chuck control is invalid, the output
point is still used to the general one without interlocking with the spindle; the input point
is still used by the user, and M91/M92/M93/M94 are still valid.
Note 2:
When the hydraulic chuck control is valid, the system defaults the chuck releasing after
power on, the first control input of chuck is valid and the system outputs the signal of
chuck clamping.
Note 3:
The chuck control invalid when the spindle rotates.
Note 4:
When the spindle rotates in the state of chuck releasing, the system prompts “Chuck
Ready Failure” and the spindle stops at the same time.
Note 5:
In the course of automatic (continuous) run, the pedal switch control is invalid whether
the spindle rotates or not. When executing M10/M11 in the course of spindle rotating,
M11
M10
input
signal
M11
M10
input
signal