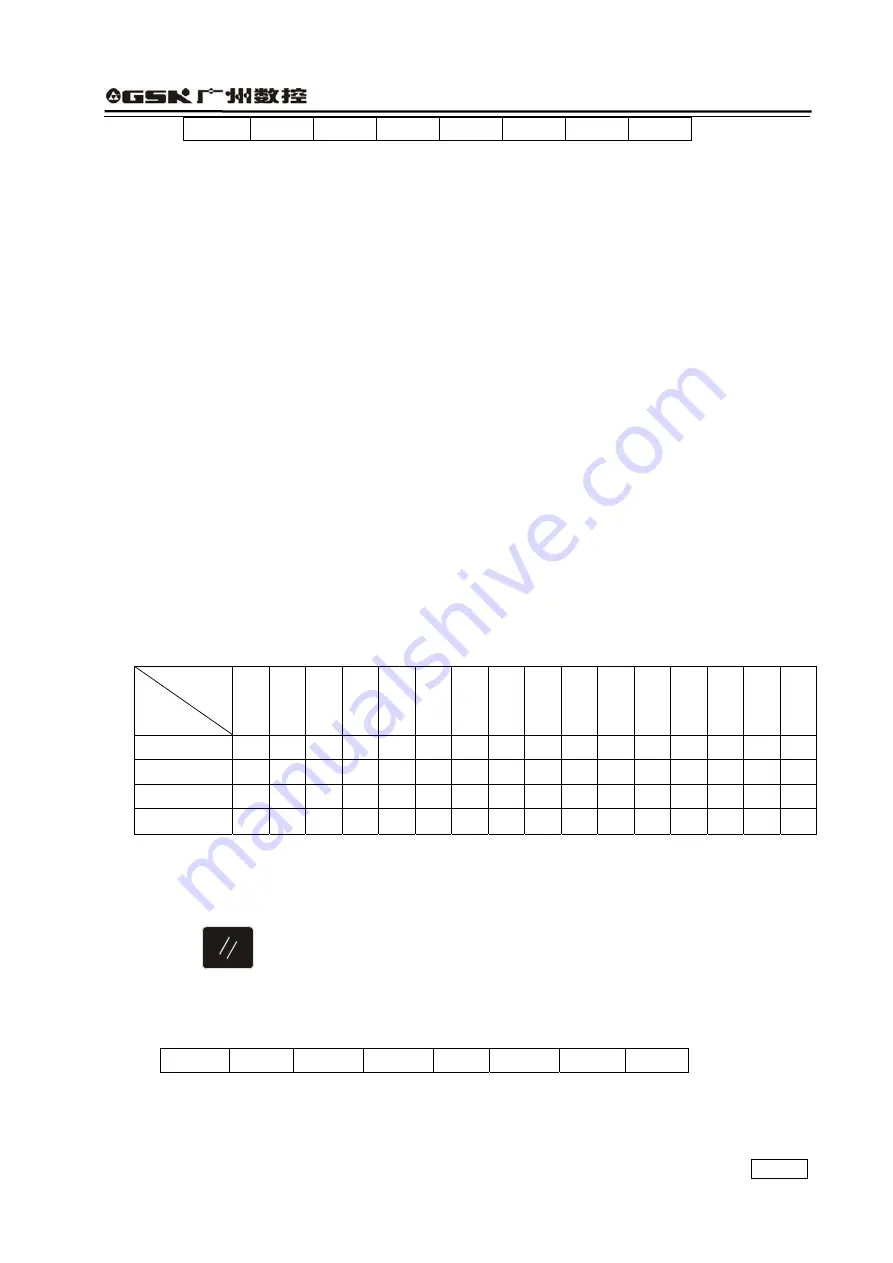
GSK928TE
Ⅱ
Turning CNC System User Manual
60
Bit7
Bit6
Bit 5
Bit 4
Bit 3
Bit 2
Bit 1
Bit 0
Bit 7 0 in MPG mode, 0.1mm override is valid.
1 in MPG mode, 0.1mm override is invalid, enter the menu after the system has
been ON for 15s.
Bit 6 0 move the machine slider not to modify the coordinates when executing the offset.
1 modify the coordinates and do not move the machine slide when executing the
offset.
Bit 5 0 the system uses the general motor turret tool post.
1 the system uses the line-up tool post.
Bit 4 0 the spindle speed gear directly outputs S1
~
S4.
1 the spindle speed gear outputs S0
~
S15 16 codes, the output is as the following
code table.
Bit 3 0 do not check the encoder resolution in
DIAGNOSIS, JOG
mode, display the
spindle programmed speed in
JOG, AUTO
mode.
1 check the encoder resolution in
DIAGNOSIS, JOG
mode, display the spindle
actual speed in
JOG, AUTO
mode.
Bit 2 0 spindle encoder pulse: 1200 pulse/r.
1 spindle encoder pulse: 1024 pulse/r.
(
the spindle speed is more than 120r/min
,
otherwise, the system does normally execute the check.
Bit 1 selecting Z motor rotation direction.
Bit 0 selecting X motor rotation direction.
Code table of S code:
Code
Output
point
S00 S01 S02 S03 S04 S05 S06 S07 S08 S09 S10 S11 S12 S13 S14 S15
S1
★
★
★
★
★
★
★
★
S2
★
★
★
★
★
★
★
★
S3
★
★
★
★
★
★
★
★
S4
★
★
★
★
★
★
★
★
“ ”: the output of corresponding
★
bit is valid.
Note 1:
By setting DIRX and DIRZ as 0 or 1, the actual rotation direction of motor can be
changed without any external tune. Ensure the moving direction of tool post is the same
that of the defined one. After rewriting the parameter of motor direction and pressing
or power on again, the direction changed is valid.
Note 2: Bit7- Bit6 are not used.
●
P12 bit specifications
Bit 7
Bit 6
Bit 5
Bit 4
Bit 3
Bit 2
Bit 1
Bit 0
P12 bit specifications
Bit 7 0
machine zero return(machine reference point) function is invalid.
1
machine zero return function is valid.
Bit 6 0 Z drive unit alarm input signal
(
Zalm
)
being HIGH, the system alarm “ Z drive