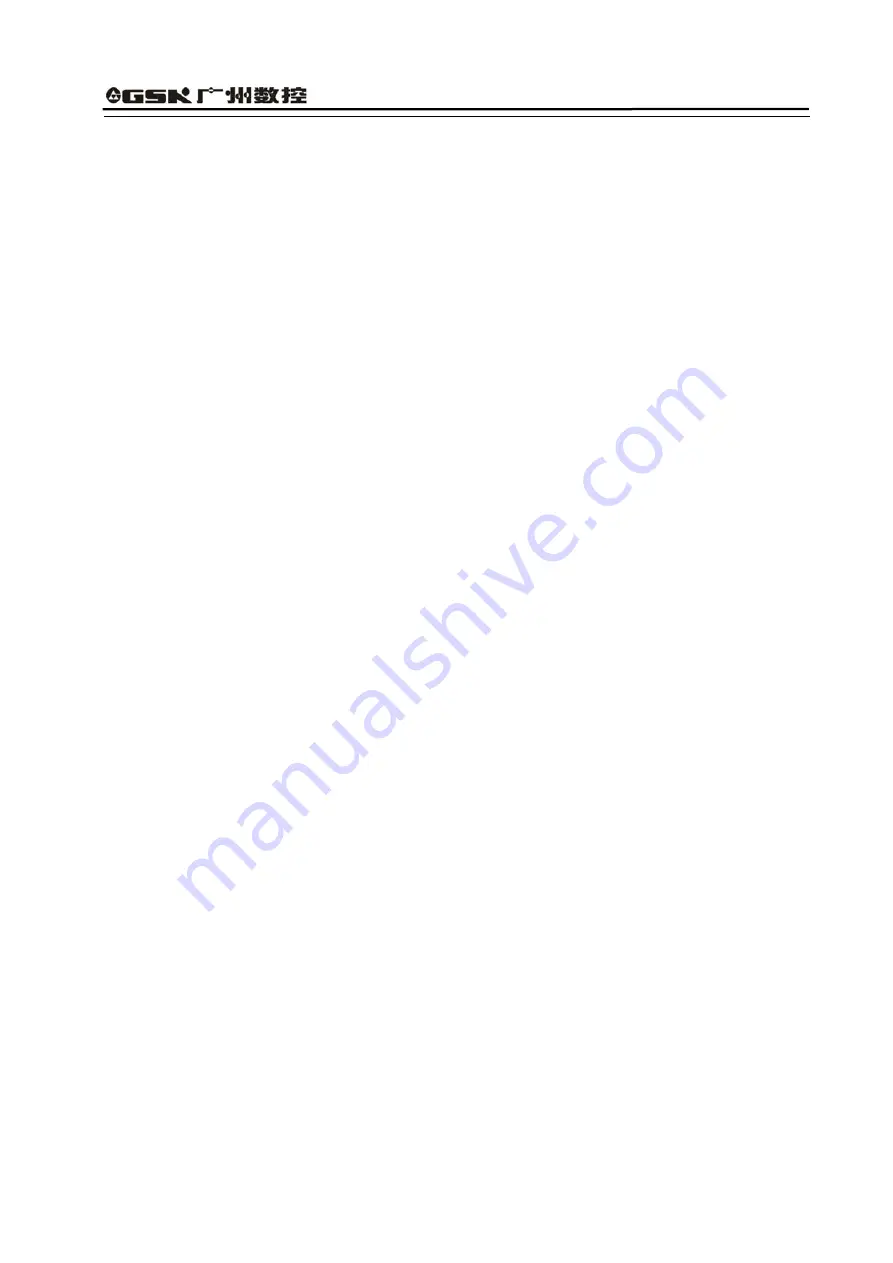
GSK928TE
Ⅱ
Turning CNC System User Manual
59
traverse override. Unit: mm/min
4.6.1.4 P06—X Rapid Traverse Speed
P06 defines X rapid traverse speed in “
Manual
” mode and G00. The actual rapid traverse speed
is also controlled by the rapid traverse override. X actual rapid traverse speed = P05* rapid
traverse override. Unit: mm/min
4.6.1.5 P07 P08—X, Z Backlash Value
P07 P08 separately defines X, Z backlash value of mechanically-driven. Unit: mm.
There are backlash clearance in the lead screw, the decelerator and other driving device, which
cause the error in the repeated motion of tool post. To avoid the error, set P07, P08, which make
CNC system automatically compensate the error when the machine changes its moving
direction.
Measurement method of mechanically-driven backlash (Example: Z axis):
z
Select
“Manual”
mode and the proper feedrate.
z
Install the dial indicator on the proper position of the machine, move the tool post to the
probe of the dial indicator and set its pointer to zero.
z
Select
STEP
mode with the step size 1.0 mm.
z
Press Z feed key to move the tool post to the dial indicator and make it point to zero when
rotating one circle.
z
Press Z feed key to move reversely and the pointer of dial indicator turns around. The
pointer cannot return to zero because of the backlash. At the moment, D-value between the
pointed position of pointer and zero is Z backlash value.
Note 1:
Repeat the above-mentioned operations many times to gain the exact measurement
value.
Note 2:
The measurement method of X backlash is the same that of Z, but the D-value must
multiply 2 to convert to the diameter value.
Note 3:
The compensation speed of X, Z backlash is the initial speed (P17, P18 value) of each
axis.
4.6.1.6 P09—Low Gear Speed of Spindle
P09 defines max. speed when the system is employed with the converter to control the spindle
with the low gear (M41 is valid) and the 10V analog output voltage of system. P09 is invalid when
the spindle is controlled with multi-gear switching value. Unit: r/min.
4.6.1.7 P10—High Gear Speed of Spindle
P10 defines max. speed when the system is employed with the converter to control the spindle
with the high gear (M43 is valid) and the 10V analog output voltage of system. P10 is invalid
when the spindle is controlled with multi-gear switching value. Unit: r/min.
Note:
The system will consider P10 value as the output benchmark when the spindle has no
high/medium/low gear. At the moment, P09, P23 are invalid. The high gear is valid after
power on.
4.6.1.8 P11 P12—Bit Parameter 1, Bit Parameter 2
For the different requirements of different machine, some control functions of this system can be
realized by setting the corresponding Bit of P11, P12 to 0 or 1.
The Bit parameters from left to right are Bit
7
~
Bit 0 . Each bit can be set to 0 or 1.
●
P11
b
it specification