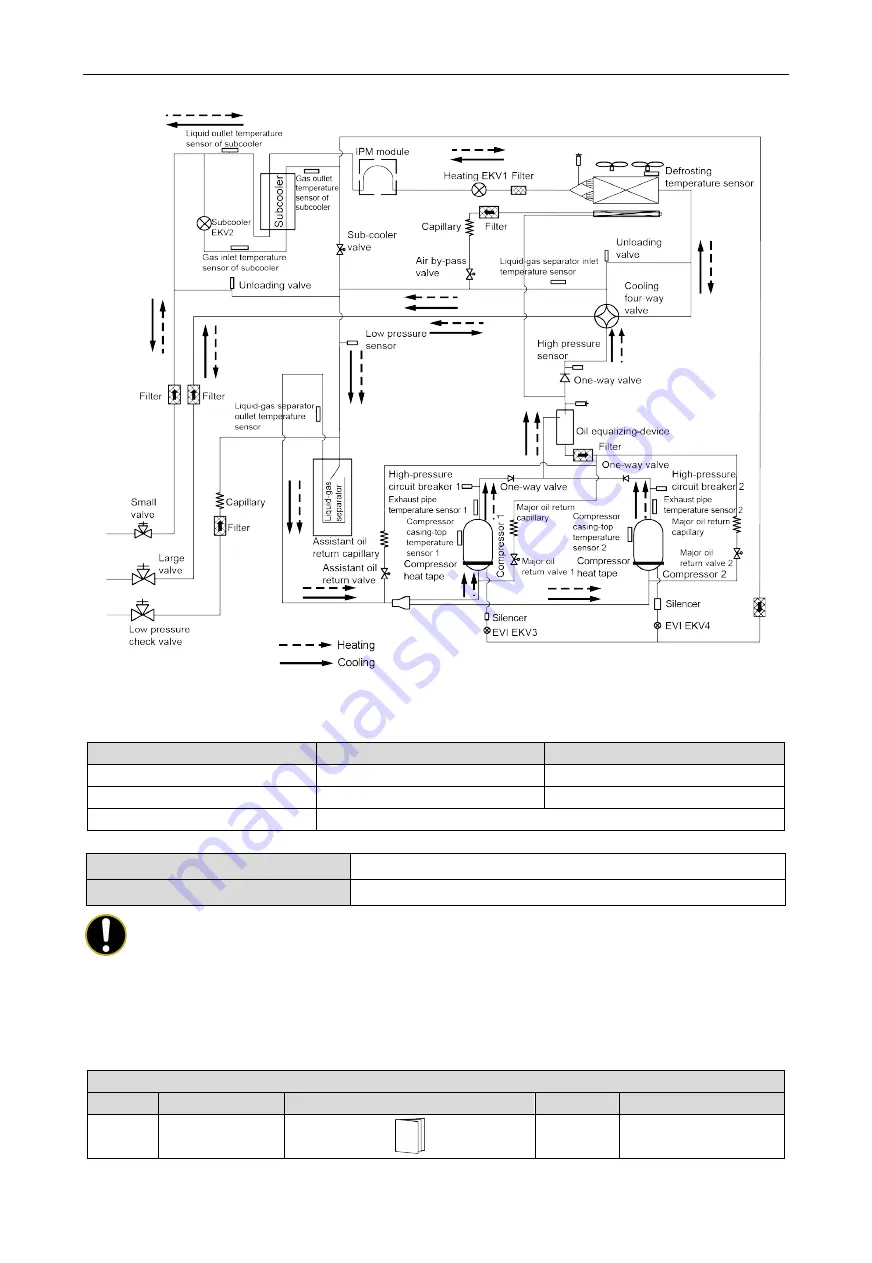
GMV DC Inverter VRF
10
System principle diagram of GMV-504WM/H-X , GMV-560WM/H-X , GMV-615WM/H-X
Fig. 2.4.3
2.5 The Range of Production Working Temperature
——
Cooling
Heating
Ambient temperature
-5
℃
~55
℃
DB
-30
℃
~24
℃
DB
Indoor temperature
14
℃
~25
℃
WB
15
℃
~27
℃
DB
Indoor humidity
≤
80%
When the indoor units are all VRF fresh air processor, the unit operating range is as follows:
Cooling
Ambient temperature: 16
℃
~45
℃
Heating
Ambient temperature: -7
℃
~16
℃
NOTE!
If exceeding the temperature range for working, the product may be damaged, which is not within
the warranty range.
2.6 Standard Parts
Please use the following standard parts supplied by Gree.
Parts for Outdoor Unit
Number
Name
Picture
Quantity
Remarks
1
Owner's Manual
1
——