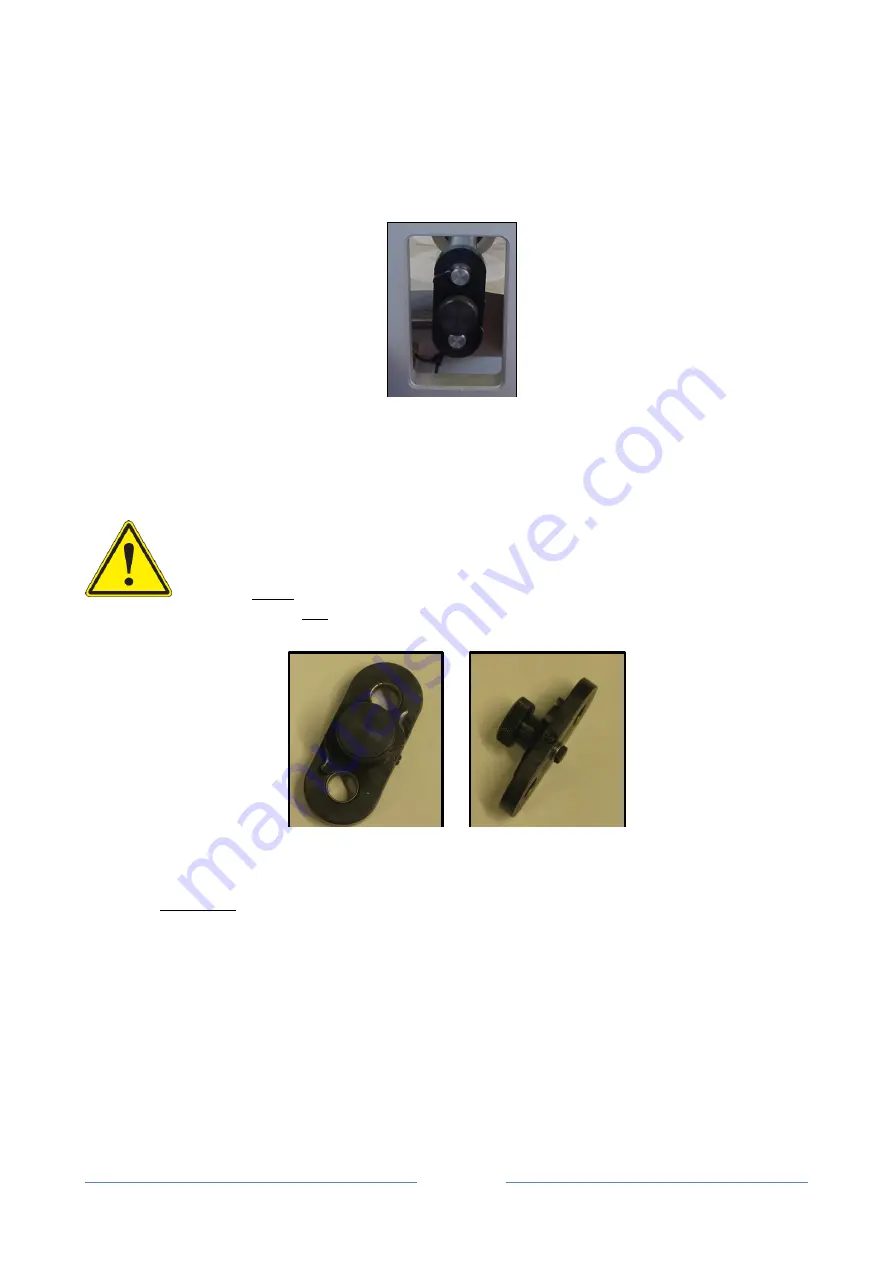
GM · CONVERTING UNIT
15
When produceing with slitting knives, it is very important to remember to mount the clamp
(see figure3).
It will stabilize the two axles and ensure a clean cut . When not using slitting knifes, the handle must only
be moved when the clamp is removed. The clamp can NOT be mounted when slitting knifes are
disengaged.
The slitting blades are running synchronised with web at a speed around 5% higher than the web. This
speed increase improves the cutting quality. When the safety cover is opened, the motor is turned off and
the blades are safe to move. Do never tighten the blades too hard, they just get harder to remove.
NOTE!
Never try to open or close the slitter knife shafts with the knife clamp mounted
on the shafts. It will damage the balance in the shafts, and the knife clamp to lock the
shafts.
5.10.
Rewinding
The two rewinders can run both ways, and can be individually turned off. As with all the other spindles,
the rotation mode is set with the rotation mode buttons, and the mandrel is engaged and released by
pressing the spindle.
The knife clamp
Figure 3 - Clamp mounted in slitting mode.