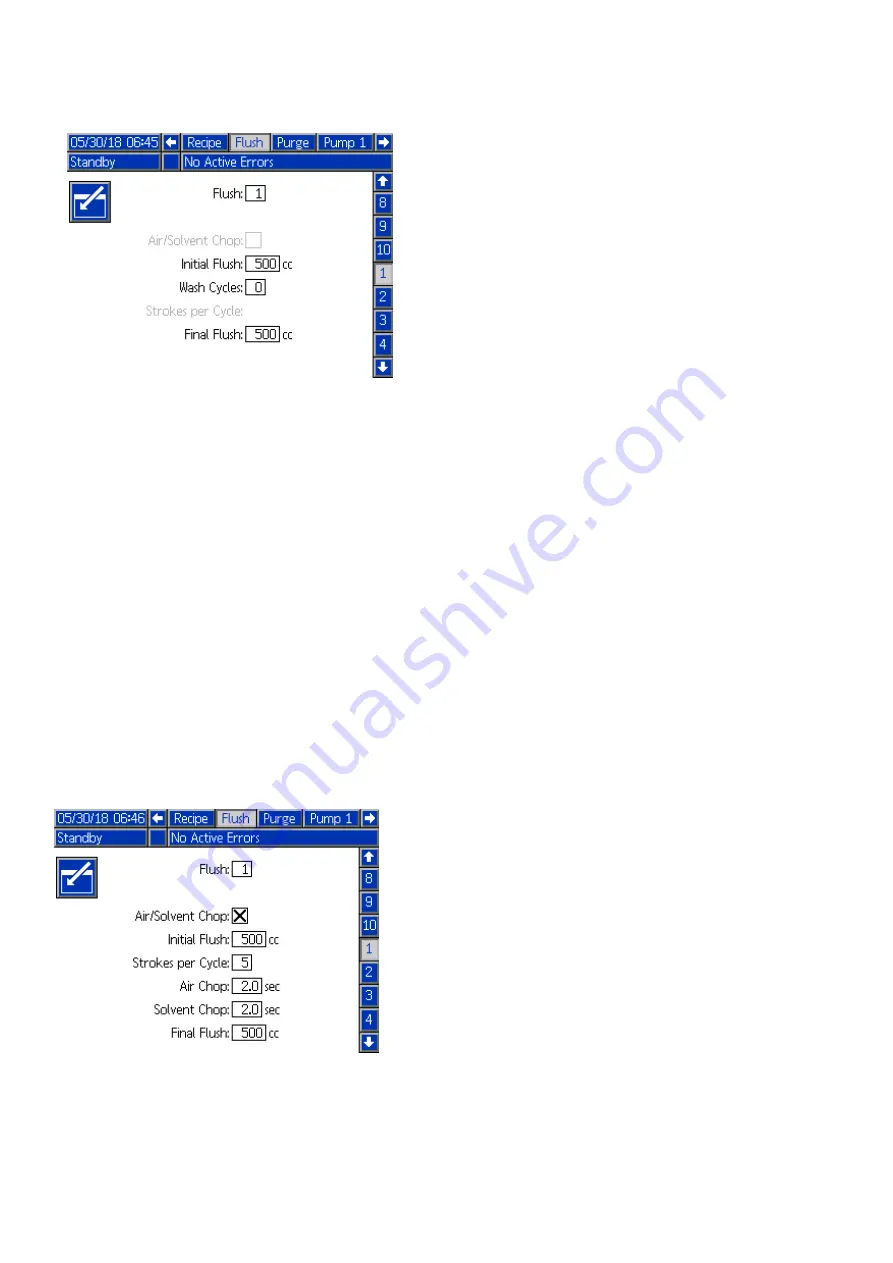
Flush
Flush
Flush Screen
Screen
Screen
Figure 55 Flush Screen
Flush
Flush
Flush Number
Number
Number
Enter the desired flush sequence (1-10). For hard
to flush colors, select a longer sequence. 1 is the
default, and should be designated for the longest,
most thorough flush duration.
Air/Solvent
Air/Solvent
Air/Solvent Chop
Chop
Chop
Enable air/solvent chop for flushing of the pump.
An air/solvent chop may be utilized in place of the
standard wash cycles to provide a more abrasive
clean, especially effective for flushing metallic
materials.
NOTE:
NOTE:
NOTE: This feature is only available for pumps that
have an air inlet valve enabled ( See
Advanced Configuration, page 84
). Air/solvent chop
requires additional hardware for the air purge valve
(See manual 333282 for kit numbers and installation).
Figure 56 Flush Screen with Chop
Initial
Initial
Initial Flush
Flush
Flush
Enter the initial flush volume (0 to 9999 cc).
Wash
Wash
Wash Cycles
Cycles
Cycles
A Wash Cycle activates the pump with the valves
closed, to use pumping motion to thoroughly clean
the pump. Enter the desired number of wash cycles
(0 to 99). Entering a number will make the Strokes
per Cycle field active.
Strokes
Strokes
Strokes per
per
per Wash
Wash
Wash Cycle
Cycle
Cycle
Enter the desired pump strokes per wash cycle (0
to 99). Default is 1.
NOTE:
NOTE:
NOTE: If Air/Solvent Chop is enabled, this setting
dictates the length of the chop cycle. Each stroke
runs about 2 seconds long, so determine your
total length of air/solvent chop time and divide by
2 seconds to determine an appropriate number of
strokes.
Final
Final
Final Flush
Flush
Flush
Enter the final flush volume (0 to 9999 cc).
Air
Air
Air Chop
Chop
Chop
Set the air chop duty cycle for the chop phase.
Solvent
Solvent
Solvent Chop
Chop
Chop
Set the solvent chop duty cycle for the chop phase.
3A6287E
79