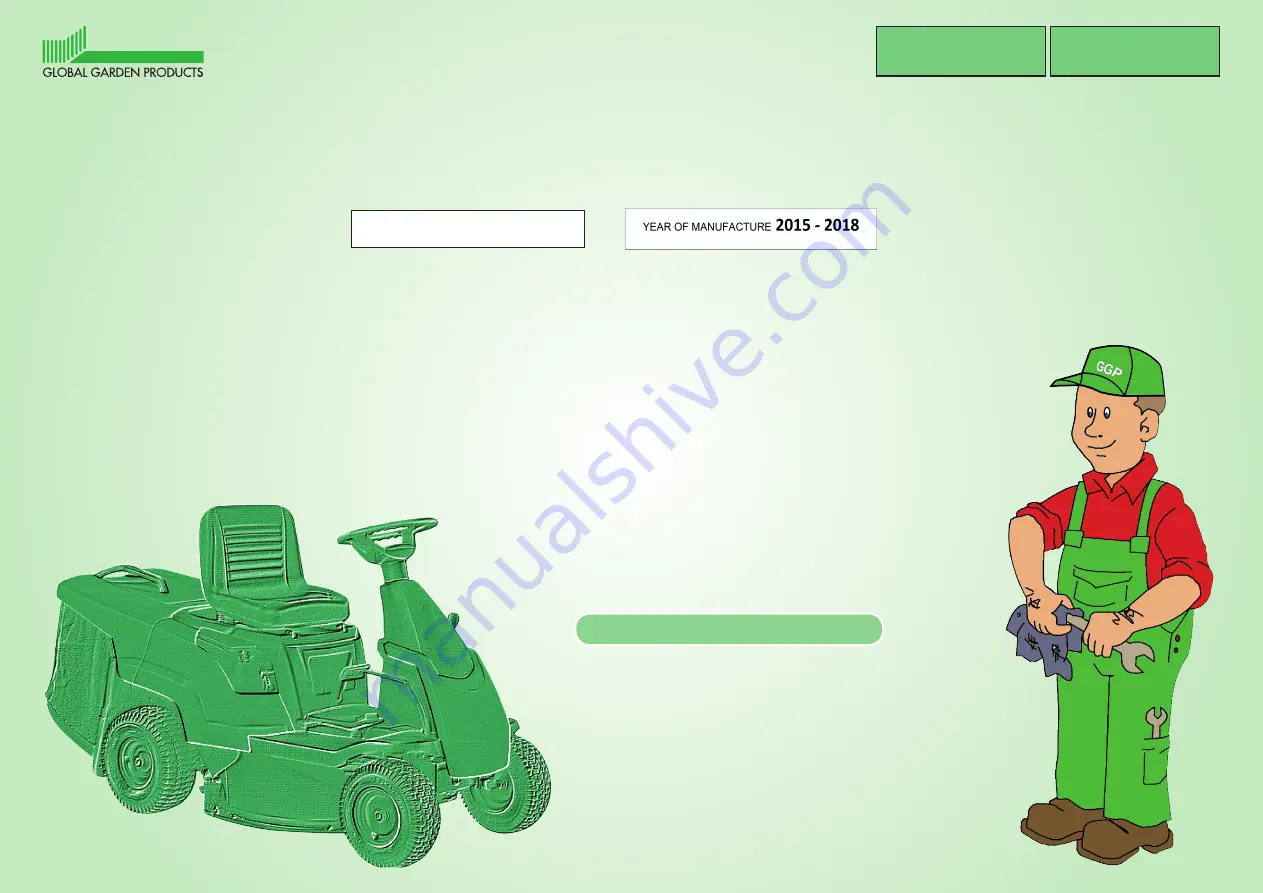
WORKSHOP MANUAL
WORKSHOP MANUAL
Rel. 3.0
YEAR OF MANUFACTURE
2015
The Manufacture reserves the right to make any improvements to the product of a technical or commercial nature
that may be necessary. There may be, therefore, differences between the various series of machines and that
described here, though the basic features and various repair methods will remain the same.
© by GLOBAL GARDEN PRODUCTS - No use of the illustrations or duplication, reproduction or translation,
even partial, of the texts in this document may be made without explicit authorization.
All brands, names, logos and trademarks mentioned
belong to their respective owners.
IMPORTANT NOTICE
- The information contained herein is intended
for Service Operations and professionals only, able to competently
perform the operations described herein, using the appropriate equip-
ment in order to safeguard security and performance of the machine.
The manufacturer is not liable for damages or injuries arising from
operations performed by individuals or inadequate facilities.
MJ66-Hy
MJ66