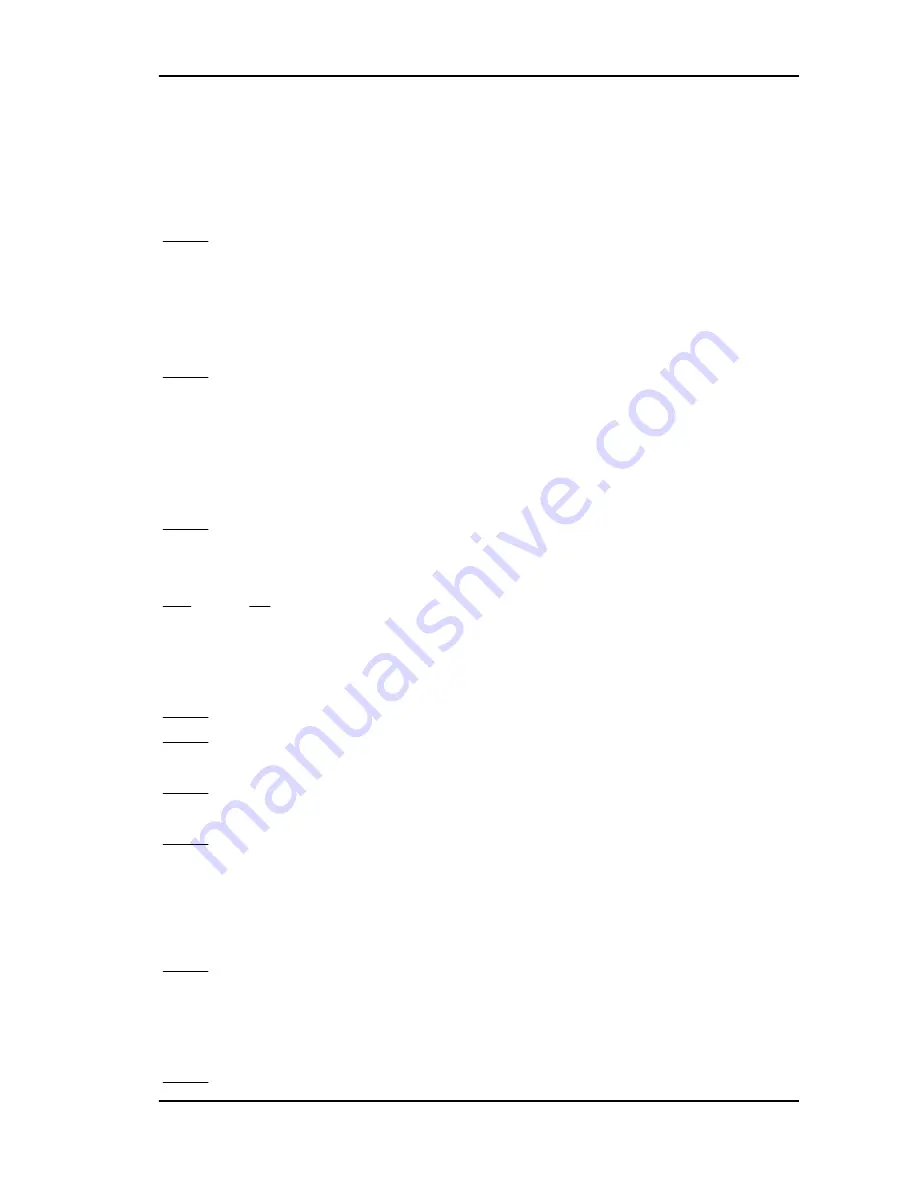
4- The ignition light does not switch on and the pump is correctly activated. Perform all the checks
required in the injection light section.
5- Connect the diagnostic tester of scooter. Select the «errors» function and check the faults that are
signalled in current status.
GO TO point 7 GO TO point 8
Specific tooling
020460Y
Scooter diagnosis and tester
6-The fuel pump did not start, but the ignition light is normally switched on. Perform all the checks
required in the «pump supply» section.
GO TO point 13
7- In current mode, the tester signals faults relating to:
- engine temperature
- TPS
Make all checks reported in the relating sections The ECU supply meets specs.
8- In current mode, the tester signals faults relating to the "battery voltage"
GO TO point 10
9- Connect the diagnostic tester of the scooter. Select the errors function. Check faults relating to «bat-
tery voltage » in stored status
YES point 15 NO point 16
Specific tooling
020460Y
Scooter diagnosis and tester
10- Measure the battery voltage.
GO TO point 11
GO TO point 12
11- Voltage is lower than 8.5 V. Recharge the battery.
GO TO point 15
12- The battery voltage is between 8.5 and 14.5 V
GO TO point 18
13- The ECU supplies are currently present. For a complete check, perform the check as described at
point «A»
14- The ignition light did not switch on. The fuel pump is not activated. When connecting the diagnostic
testers, the following message appears: «the ECU does not respond, check all connections».
GO TO point 19
Specific tooling
020460Y
Scooter diagnosis and tester
15
- Check the charger.
GO TO point 17
Runner Purejet
pure jet injection
INJ PJ - 127
Summary of Contents for Runner Purejet 2007
Page 1: ...WORKSHOP MANUAL 633499 Runner Purejet ...
Page 5: ...INDEX OF TOPICS CHARACTERISTICS CHAR ...
Page 15: ...INDEX OF TOPICS TOOLING TOOL ...
Page 26: ...INDEX OF TOPICS MAINTENANCE MAIN ...
Page 35: ...INDEX OF TOPICS TROUBLESHOOTING TROUBL ...
Page 39: ...INDEX OF TOPICS ELECTRICAL SYSTEM ELE SYS ...
Page 54: ...INDEX OF TOPICS ENGINE FROM VEHICLE ENG VE ...
Page 61: ...INDEX OF TOPICS ENGINE ENG ...
Page 101: ...INDEX OF TOPICS SUSPENSIONS SUSP ...
Page 112: ...INDEX OF TOPICS PURE JET INJECTION INJ PJ ...
Page 180: ...B Fixed pure jet injection Runner Purejet INJ PJ 180 ...
Page 181: ...INDEX OF TOPICS BRAKING SYSTEM BRAK SYS ...
Page 190: ...INDEX OF TOPICS COOLING SYSTEM COOL SYS ...
Page 196: ...INDEX OF TOPICS CHASSIS CHAS ...
Page 206: ...INDEX OF TOPICS PRE DELIVERY PRE DE ...
Page 210: ...INDEX OF TOPICS TIME TIME ...