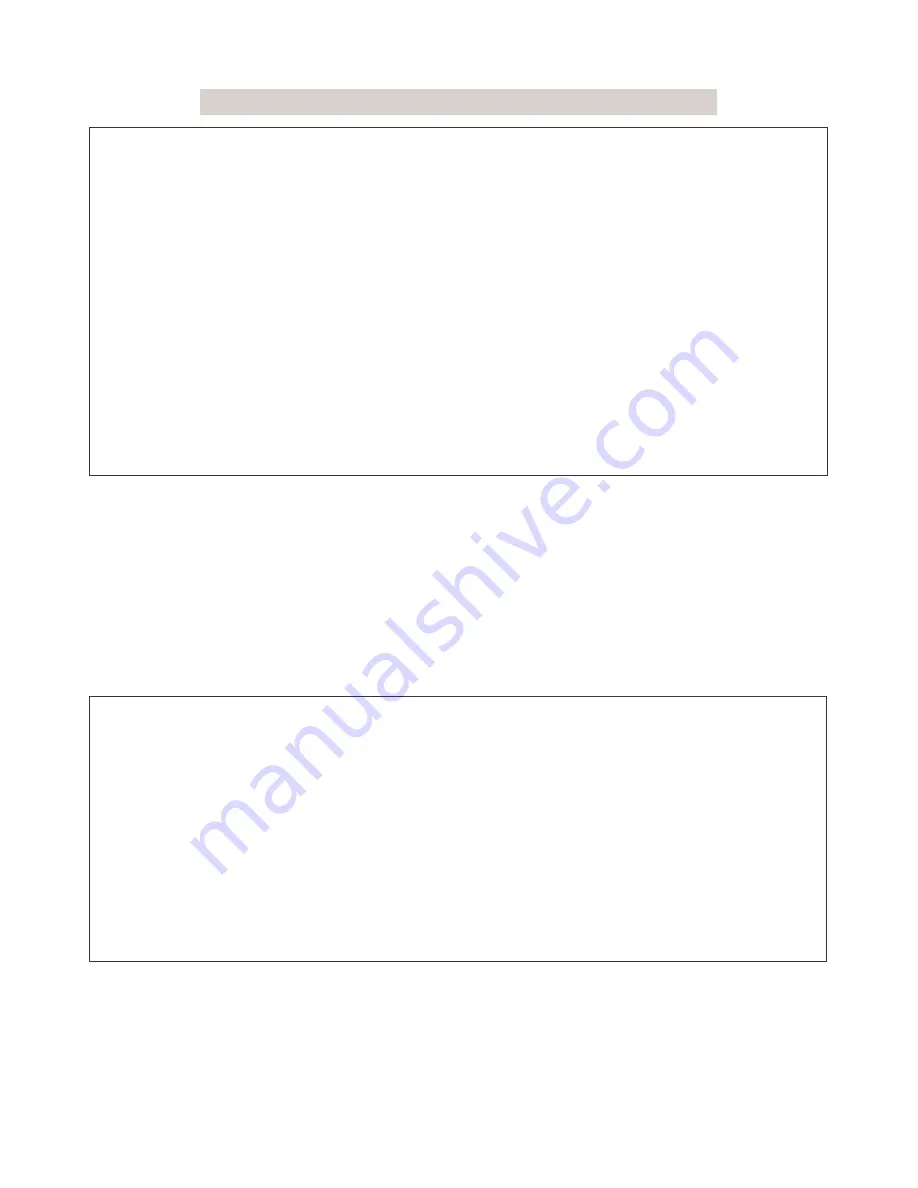
Chapter 4 Software Index
4-44
Parameter Group 9 – Drive and Load Protection Modes
9-00
:
:
:
:
Trip Prevention Selection During Acceleration:
0000
:
:
:
:
Enable Trip Prevention During Acceleration
0001
:
:
:
:
Disable Trip Prevention During Acceleration
9-01
:
:
:
:
Trip Prevention Level During Acceleration: 50% ~ 300%
9-02
:
:
:
:
Trip Prevention Selection During Deceleration:
0000
:
:
:
:
Enable Trip Prevention During Deceleration
0001
:
:
:
:
Disable Trip Prevention During Deceleration
9-03
:
:
:
:
Trip Prevention Level During Deceleration: 50% ~ 300%
9-04
:
:
:
:
Trip Prevention Selection in Run Mode:
0000
:
:
:
:
Enable Trip Prevention in Run Mode
0001
:
:
:
:
Disable Trip Prevention in Run Mode
9-05
:
:
:
:
Trip Prevention Level in Run Mode: 50% ~ 300%
9-06
:
:
:
:
Trip Prevention Deceleration Time Selection in Run Mode:
0000: Trip Prevention Deceleration Time Set by 3-03
0001: Trip Prevention Deceleration Time Set by 9-07
9-07
:
:
:
:
Deceleration Time in Trip Prevention Mode (sec): 0.1 ~ 3600.0
1. In acceleration, the inverter will delay the acceleration time if the time is too short resulting in the
over current in order to prevent the inverter trips.
2. In deceleration, the inverter will delay the acceleration time if the time is too short resulting in the
over voltage of DC VUS in order to prevent the inverter trips with ‘OV’ displayed.
3. Some mechanical characteristics (such as press) or unusual breakdown (seize due to insufficient
lubrication, uneven operation, impurities of processed materials, etc.) will cause the inverter to trip,
thus inconvenience users. When the operating torque of the inverter exceeds the setting of 9-05,
the inverter will lower the output frequency following the deceleration time set by 9-06, and return
to the normal operation frequency after the torque get steady.
9-08
:
:
:
:
Electronic Motor Overload Protection Operation Mode:
0000
:
:
:
:
Enable Electronic Motor Overload Protection
0001
:
:
:
:
Disable Electronic Motor Overload Protection
9-09
:
:
:
:
Motor Type Selection:
0000
:
:
:
:
Electronic Motor Overload Protection Set for Non-Inverter Duty Motor
0001
:
:
:
:
Electronic Motor Overload Protection Set for Inverter Duty Motor
9-10
:
:
:
:
Motor Overload Protection Curve Selection:
0000
:
:
:
:
Constant Torque (OL=103%)(150%,1 minute)
0001
:
:
:
:
Variable Torque (OL=113%)(123%,1 minute)
9-11
:
:
:
:
Operation After Overload Protection is Activated:
0000
:
:
:
:
Coast-to-Stop After Overload Protection is Activated
0001
:
:
:
:
Drive Will not Trip when Overload Protection is Activated (OL1)
Description of the thermal relay function:
1. 9-10 = 0000
:
protect the general mechanical load, the load is less than 103% rated current, the
motor continue to run. The load is larger than 150% rated current, the motor will run
for 1 minute.(Refer to following curve(1).
= 0001
:
protect HVAC load(FAN
、
PUMP…so on)
:
the load is less than 113% rated current,
the motor continue to run. The load is larger than 123% rated current, the motor will