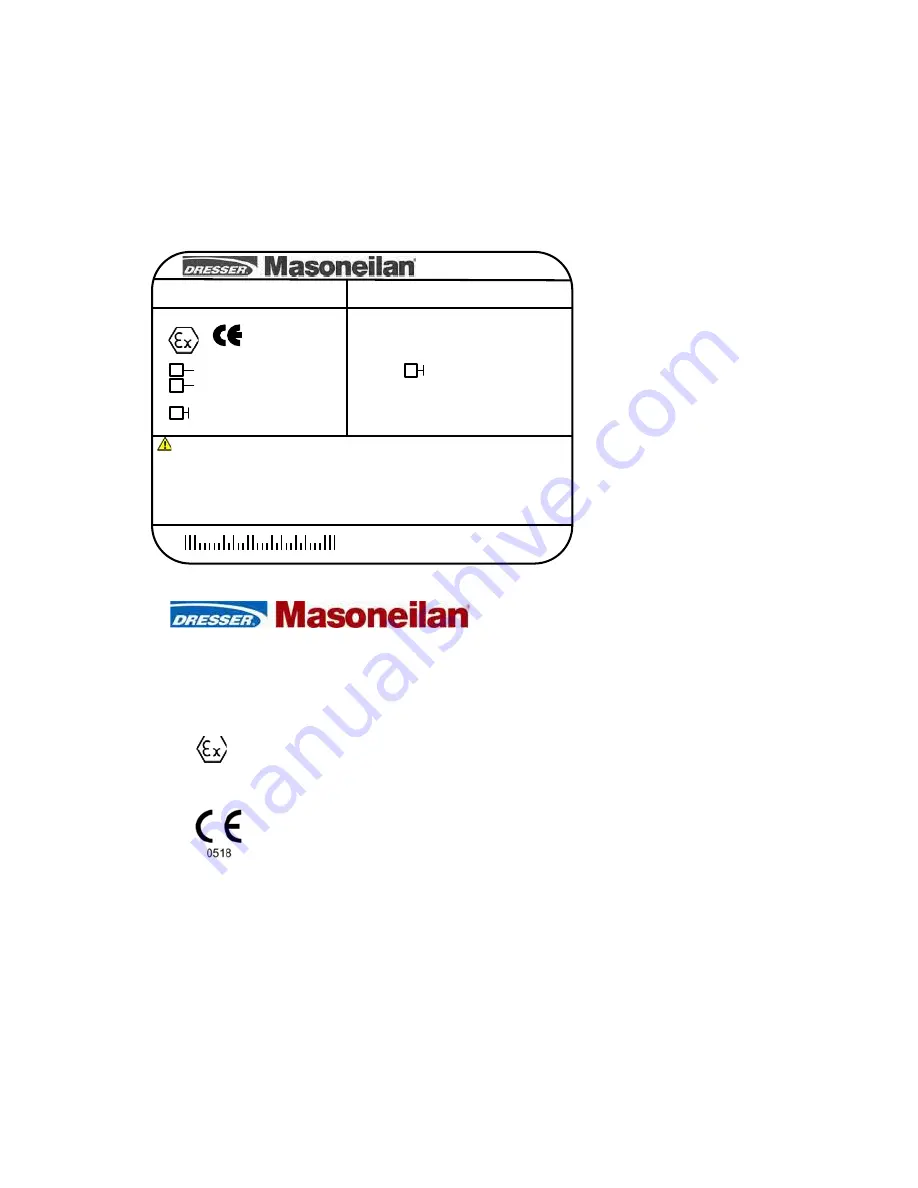
Masoneilan SVI II AP Digital Positioner Quick Start Guide
=
|
75
© 2015 General Electric Company. All rights reserved
.
ES-699 Rev AA
Page 9 of 16
7
DESCRIPTION OF INTRINSICALLY SAFE MARKINGS (Applies to “Easy
Smart” version only)
Applicable Model Numbers:
SVI2-abcdefgh, where “a” thru “h” can take on the following values:
a = 1 ; b = 1 ; c = 1 ; d = 1, 2 ; e = 3 ; f = 1 ; g = 1,2 ; h = 3,4
The label may not appear exactly as shown, but must contain the following information
listed below. Other information is allowed on the label.
II 3G Ex ic IIC T6
Avon MA USA
WARNING
REFER TO ES-699 FOR ADDITIONAL CAUTIONS OR WARNINGS
Supply Connection Wiring Rated for 5ºC Above Max Ambient
MODEL: SVI2-1bcdefgh
30 Volts, 4-20mA, 80 PSI
Type 4X-IP66
DO NOT OPEN EVEN WHEN ISOLATED WHEN
FLAMMABLE / DUST ATMOSPHERES ARE
PRESENT
ZELM 05ATEX0280X
SN-nnywwnnnn
Operating Temp –40ºC to +85ºC
T6 Ta=60ºC, T5 Ta=75ºC, T4 Ta=85ºC
055201-188-779
Rev G
PERMANENTLY MARK THE PROTECTION TYPE
CHOSEN. ONCE THE TYPE HAS BEEN MARKED, IT
CAN NOT BE CHANGED.
II 2G Ex ia IIC T6
0518
Ex ia IIC T6
IECEx FMG 07.0007x
IECEx
II 2D Ex ia IIIC T96°C
7.1
Manufacturers Name and Location
Avon MA – 02322 – USA
7.2
Markings:
(ATEX)
{Explosion Protected Mark}
{CE Conformity Marking, QAN
Notified Body Number}
ZELM
{Certifying Agency}