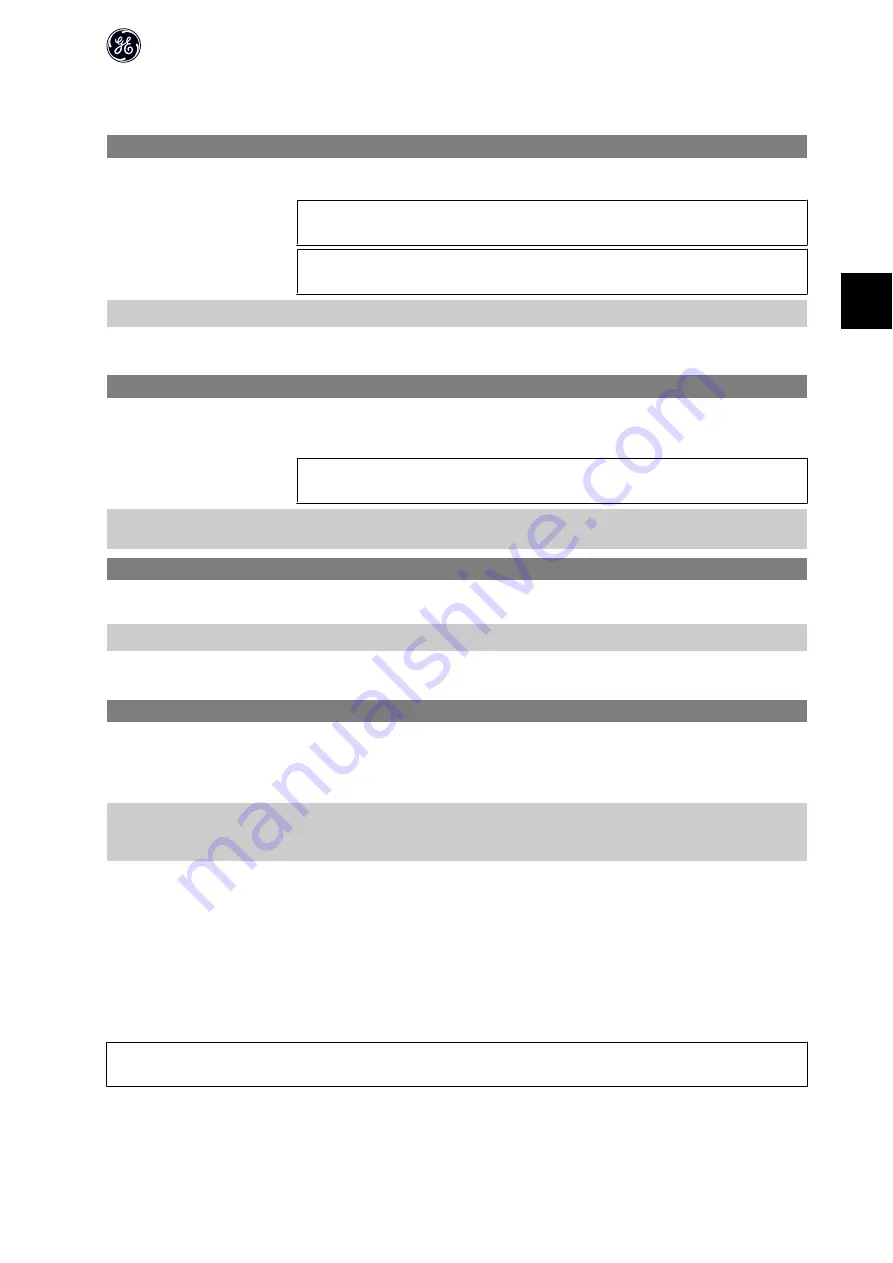
4.2. Parameter Group 1: Load/Motor
1-00 Configuration Mode
Option:
Function:
Use this parameter for selecting the application control principle to be used when a Remote Reference is active.
NB!
Changing this parameter will reset parameters 3-00, 3-02 and 3-03 to their default values.
NB!
This parameter cannot be adjusted while motor runs.
[0 ]
*
Speed Open Loop
For normal speed control (References).
[3]
Process Closed Loop
Enables process closed loop control. See par. group 7-3* for further information on PI-controller.
When running in process closed loop, par. 4-10
Motor Speed Direction
must be set to
Clockwise
[0]
1-01 Motor Control Principle
Option:
Function:
[0]
U/f
Is used for parallel connected motors and/or special motor applications. The U/f settings are set in parameters 1-55
and 1-56.
NB!
When running U/f control slip- and load compensations are not included.
[1]
*
Advanced Vector Con-
trol
Normal running mode, including slip- and load compensations.
1-03 Torque Characteristics
Option:
Function:
With more torque characteristics it is possible to run low energy consuming, as well as high torque applications.
[0 ]
*
Constant Torque
Motor shaft output provides constant torque under variable speed control.
[2]
Energy Savings
This function automatically optimizes energy consumption in centrifugal pump and fan applications. See par. 14-41
Energy Savings Minimum Magnetisation
.
1-05 Hand Mode Configuration
Option:
Function:
This parameter is only relevant when parameter 1-00
Configuration Mode
is set to
Process Closed Loop
[3]. The pa-
rameter is used for determining the reference or setpoint handling when changing from Auto Mode to Hand Mode on
the Keypad.
[0]
Speed Open Loop
In Hand Mode the drive always runs in Open Loop configuration regardless of setting in par. 1-00
Configuration
Mode
. Local potentiometer (if present) or Arrow up/down determines output frequency limited by Motor Speed High/
Low Limit (parameters 4-14 and 4-12).
[2]
*
As configuration in par.
1-00
If par. 1-00
Configuration Mode
is set to
Open Loop
[1] function is as described above.
If par. 1-00 is set to
Process Closed Loop
[3] changing from Auto mode to Hand mode results in a setpoint change via
local potentiometer or Arrow up/down. The change is limited by Reference Max/Min (parameters 3-02 and 3-03).
4.2.1. 1-2* Motor Data
Enter the correct motor nameplate data (power, voltage, frequency, current and speed).
Run Auto Tune, see par. 1-29.
Factory settings for advanced motor data, par. 1-3*, are automatically calculated.
NB!
Parameters in parameter group 1.2* cannot be adjusted while motor runs.
AF-60 LP™ Micro Drive Programming Guide
15
4