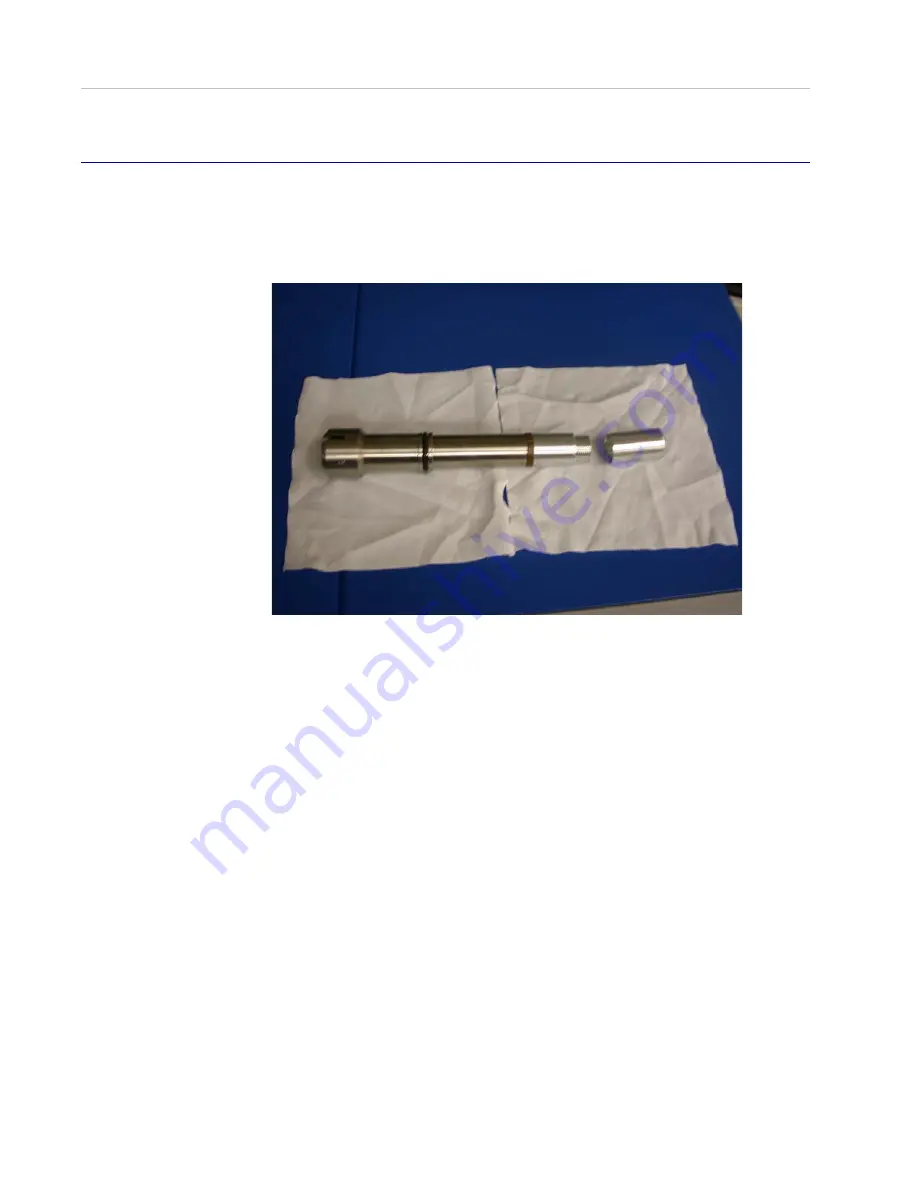
24
Solarus 950 Owner’s Manual and User’s Guide
Removing the Ion Shield
When cleaning a TEM holder that does not have a sample installed, you may
remove the ion shield in order to increase the cleaning speed (although it is not
necessary). This should not be done if a sample is installed or the sample may
experience ion damage. To remove, unscrew the ion shield (counter clock wise).
ƒigure 14
TEM holder-adapter with ion shield removed