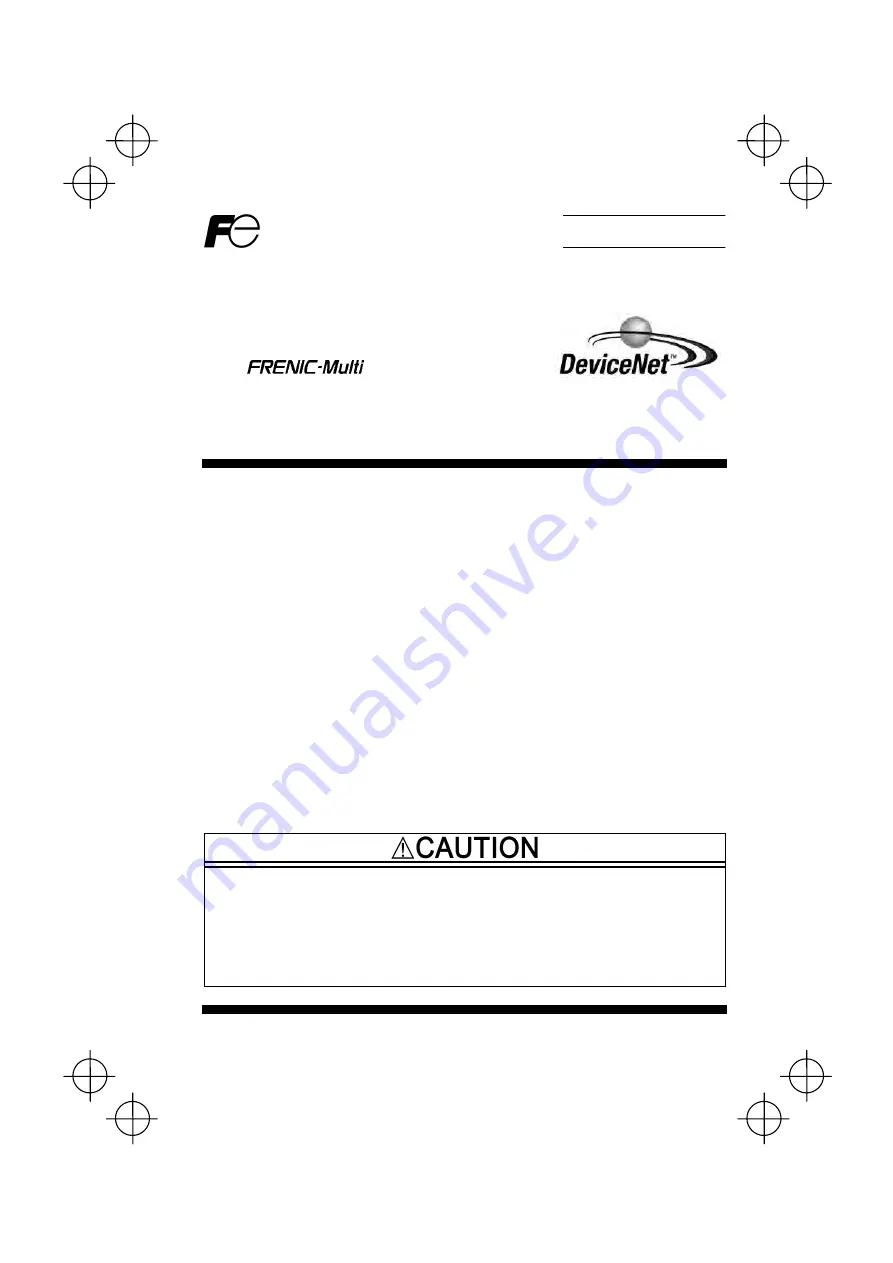
Instruction Manual
DeviceNet Interface Option
"OPC-E1-DEV"
Thank you for purchasing our DeviceNet Interface Option OPC-E1-DEV.
• This product is designed to connect the FRENIC-Multi series of inverters to DeviceNet. Read through this
instruction manual and be familiar with the handling procedure for correct use.
• Improper handling blocks correct operation or causes a short life or failure.
• Deliver this manual to the end user of the product. The end user should keep this manual in a safe place
until the DeviceNet Interface Option is discarded.
• For the usage of inverters, refer to the instruction manual prepared for the FRENIC-Multi series of inverters.
Fuji Electric FA Components & Systems Co., Ltd.
Summary of Contents for FRENIC-Multi OPC-E1-DEV
Page 40: ...38 MEMO...