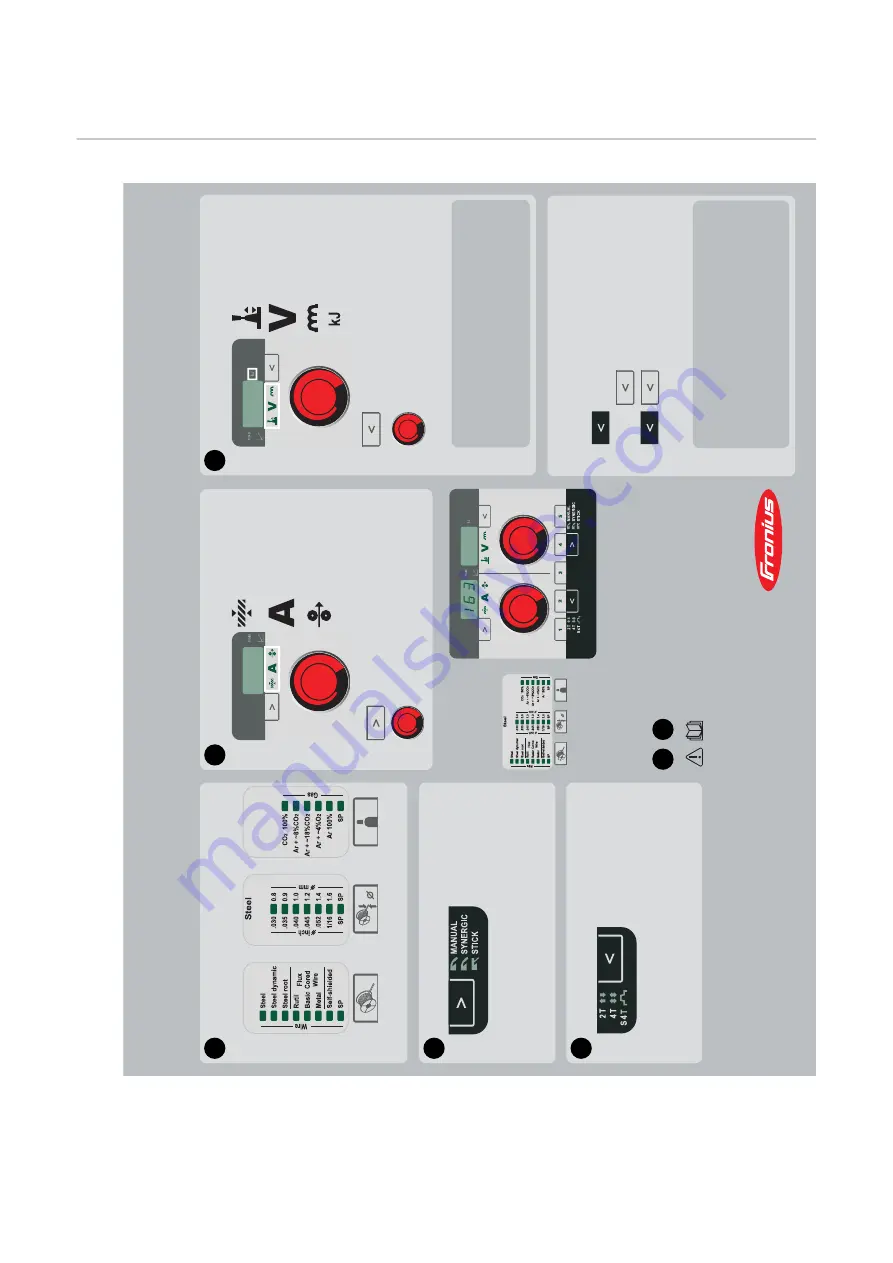
Appendix
Quick reference
4
1
3
2
5
Fronius International GmbH, www
.fronius.com
Keylock
Important!
If the keylock is activated, only the
parameter settings can be retrieved, as well
as any assigned “Save“ button provided that
an assigned “Save“ button was selected when
the keylock was enabled.
-
press and hold
- press
- release
activate / deactivate:
activated: „CLO | SEd“ display
deactivated: „OP
| En“ display
Quick Reference: English
Setting the welding power
Selecting the fi
ller metal and
shielding gas
2 T
2-step
mode
4 T
4-step
mode
S 4
T
Special 4-step mode
Selecting the process
Setting the mode
MANUAL
MIG/MAG standard manual
SYNERGIC Standard
synergic
STICK
Manual metal arc welding
Correcting parameters
Important
If external system components
are connected, some parameters can be
modifi
ed on those components.
The power
source control panel is only for display
purposes.
01/2013
Start-up sequence
Follow operating instructions
-
1
5
T
ransSteel Synergic
SP
... Special Program
-
select desired parameter
- set desired parameter
Sheet thickness
W
elding current
Wire feed speed
Arc length
correction
W
elding voltage
Dynamic
-
select desired parameter
- set desired parameter
Real Energy Input
114
Summary of Contents for TransSteel 2700c
Page 2: ......
Page 18: ...18...
Page 19: ...General information 19...
Page 20: ...20...
Page 26: ...VRD is active again The output voltage is limited to 35 V once more 26...
Page 27: ...Control elements and connections 27...
Page 28: ...28...
Page 37: ...Installation and commissioning 37...
Page 38: ...38...
Page 62: ...62...
Page 63: ...Welding 63...
Page 64: ...64...
Page 78: ...Number 2 Number 3 Number 4 Number 5 78...
Page 79: ...Setup settings 79...
Page 80: ...80...
Page 91: ...10 Fit the gas nozzle back onto the welding torch 91 EN...
Page 93: ...Troubleshooting and maintenance 93...
Page 94: ...94...