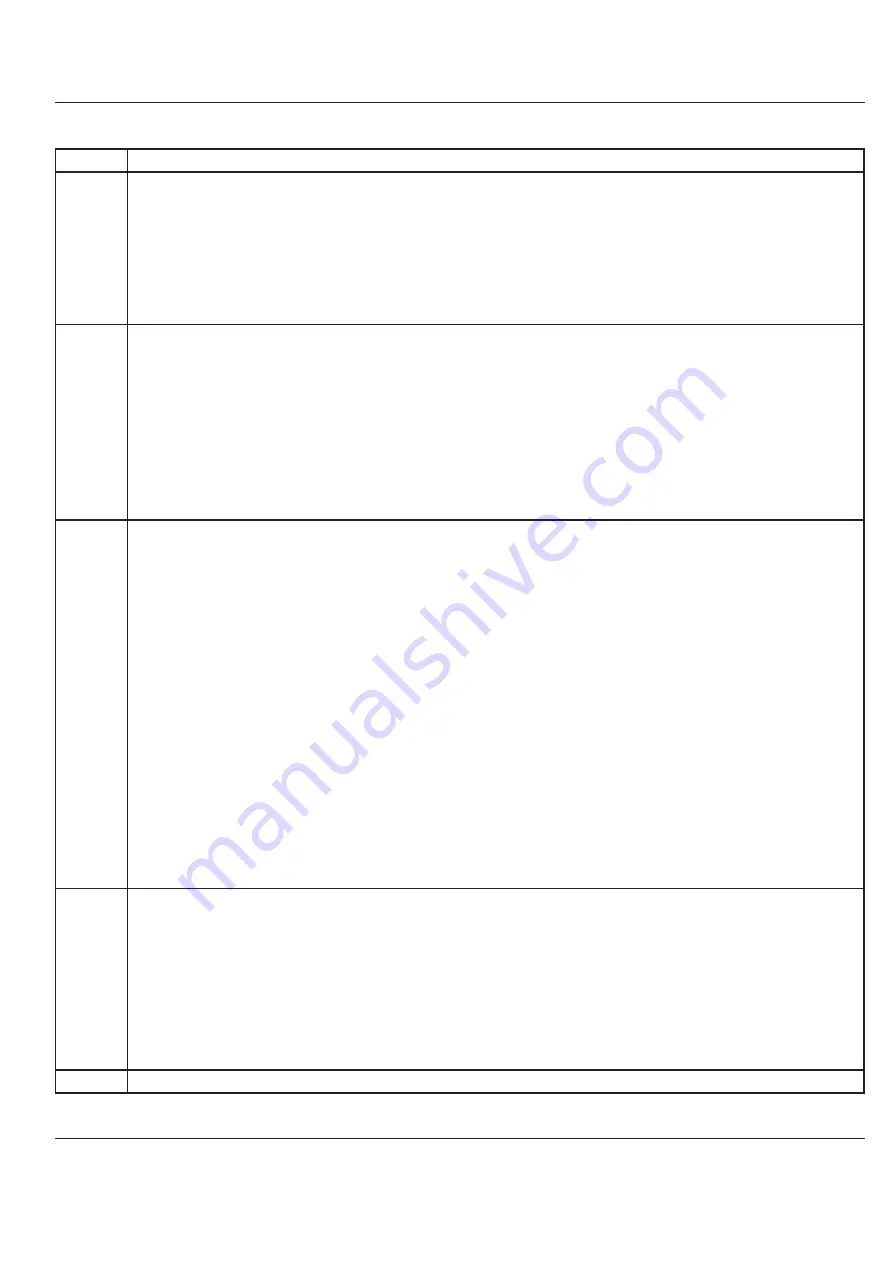
Tstat Series
- 19 -
Code
Description (Range, Default)
PPr
Proportional Term (10-255, 20)
The proportional term is the ‘P’ term of the familiar PID control strategy and determines how fast a valve will react to a deviation from
setpoint at a particular instant in time. The default value of 2.0° (C or F) is
fi
ne for most applications, where a 2.0° deviation is required
to make the valve respond 100%. For example, with the PPr term set to 2.0 (°C) and the cooling setpoint is set to 20°C, the valve will be
open 100% by the time the room hits 22°C. A larger PPr term will make the valve lazy since the deviation from setpoint will have to be
greater before it opens 100%. A smaller value makes the valve respond more quickly. The factory setting of 2.0° (C or F) is
fi
ne where the
thermostat is located out of the direct air
fl
ow in an of
fi
ce size room. For a smaller room or if the thermostat is located directly under the air
vent, a slower acting valve is required to avoid short cycling, so set the value of PPr to 3.0° or 4.0°. The PPr term acts in cooperation with
the PIn term which is described next. The P value is in increments of 0.1° (i.e. 20 means 2.0°) and is in the same units (C or F) as the tstat.
PIn
Integral Term (0-255, 50)
The integral term is the ‘I’ term of the familiar PID control strategy and determines how fast a valve will react to a deviation from setpoint
over time. For example with the room slightly above setpoint, the ‘P’ term may be basically satis
fi
ed, but a small deviation still exists. This
deviation is summed up or ‘Integrated’ over time and the I term will gradually open the valve to make up the
fi
nal small deviation from set-
point. The default value of 5.0 (%/Deg minute) is
fi
ne for most applications and will cause the valve to open 5% for one degree (C or F) of
error per minute. For example, when the PIn term set to the default of 5.0 (%/Deg minute), the cooling setpoint is set to 20°C, and the room
temperature is 21°C, the valve will be open partially due to the “P” term described earlier but the condition continues and we would like
the valve to be opening up slowly to make up the
fi
nal temperature error. If this situation of 1.0°C error continues for one minute, the error
accumulates and the I term nudges the valve open an additional 5%. If the previous explanation is not clear, a couple of helpful reminders
are as follows: -think of the I term as the opposite of the P term, -”a bigger I means faster valve, smaller I means lazier valve”. -The default
value of 5% will work
fi
ne for most applications. -If the valve is short cycling, make the I term lazier (smaller). The I value is in increments
of 0.1 %/°min (i.e. 50 means 5.0%/°min) and is in the same units (C or F) as the tstat.
SOP
Sequence of Operations (0-2, 1)
The Sequence of operation is normally set at the factory and does not need to be adjusted. The thermostat supports
fi
eld adjustment of
the operation to suit different variations of mechanical equipment. Setting this value to a different value will cause the thermostat to stop
working properly, so be careful not to adjust this value unless you are familiar with the various sequences.
Standard Operation:
When SOP is set to 1, the sequence of operations is stored in a table that allows for basically any arbitrary sequence of operation, for
example the tstat could be set up to control 5 stages of cooling, 5 stages of heating, or anything in between. Each output is individually
assigned to be active in any particular section of the cooling or heating cycle. There are 7 discreet steps, Heat3, Heat2, Heat1, Coasting,
Cool1, Cool2 and Cool3. So the table is a 5 outputs x 7 steps spreadsheet arrangement and you
fi
ll in the blanks to suit the application.
The settings can be stored in an external text
fi
le that is easily read and modi
fi
ed in a text editor. The “Tstat Factory” software utility on our
website (http://www.temcocontrols.com/ftp/tstat5software.zip) allows you to send your favorite sequence of operations table to a new tstat
speeding up the con
fi
guration process.
Transducer Mode:
Setting SOP to 2, puts the Tstat into transducer mode. In this mode, the cooling analog output corresponds directly to the room tempera-
ture in degrees C (i.e. at 25°C, the output would be 2.5V). The heating analog output corresponds directly to the setpoint in degrees C.
And relay1 corresponds to the occupied/unoccupied mode (occupied = relay1 ON, unoccupied = relay1 OFF).
Test Mode:
A special sequence of operations is embedded in the tstat that assists in commissioning of the installation and testing of the tstats. When
SOP is set to ‘0’ this is the testing sequence and the unit will cycle the relay outputs on and off in a slow rotation. The analog outputs are
also cycled in a slow ramp, the cooling goes from 0-10V while the heating goes in reverse from 10 to 0V. The duty cycle of this rotation is
approximately 20 seconds, be sure the mechanical system is able to handle this sort of cycling before using this feature.
HC
Heating Cooling Mode Confi guration (0-5, 0)
This item con
fi
gures the method by which the tstat determines the heating or cooling mode.
HC = 0: mode is controlled automatically by the PID. PID > 52 is heating mode, PID < 48 is cooling mode.
HC = 1: mode is controlled by the keypad or serial communication. This is for keypad con
fi
gurations in which the user or serial com can
manually set heating or cooling.
HC = 2: mode is controlled by the active high digital input. High is heating, low is cooling.
HC = 3: mode is controlled by the active low digital input. High is cooling, low is heating.
HC = 4: mode is controlled by difference in temperature of setpoint and analog in1 sensor. If the temperature of the sensor is greater
than the setpoint, the tstat will be in cooling mode, and if the temperature of the sensor is less than the setpoint, the tstat will be
in heating mode. This is primarily used for 2-pipe systems.
HC = 5: same as mode 4, but using the analog in2 sensor instead of analog in1.
Summary of Contents for Tstat Series
Page 6: ...Tstat Series 6 ...
Page 7: ...Tstat Series 7 ...
Page 8: ...Tstat Series 8 Switching Time Measurement Circuit and Waveforms ...
Page 9: ...Tstat Series 9 Tstat6 Highlights ...
Page 10: ...Tstat Series 10 Tstat6 Jumper Settings Tstat6 Wiring Diagram ...
Page 11: ...Tstat Series 11 Tstat6 CO2 Highlights Tstat6 CO2 Jumper Settings ...
Page 12: ...Tstat Series 12 Tstat6 CO2 Wiring Diagram ...
Page 13: ...Tstat Series 13 Tstat6 Zigbee Highlights ...
Page 14: ...Tstat Series 14 Tstat6 Zigbee Jumper Settings Tstat6 Zigbee Wiring Diagram ...
Page 15: ...Tstat Series 15 Tstat6 OCC Highlights ...
Page 16: ...Tstat Series 16 Tstat6 OCC Jumper Settings Tstat6 OCC Wiring Diagram ...
Page 26: ...Tstat Series 26 ...
Page 31: ...Tstat Series 31 ...