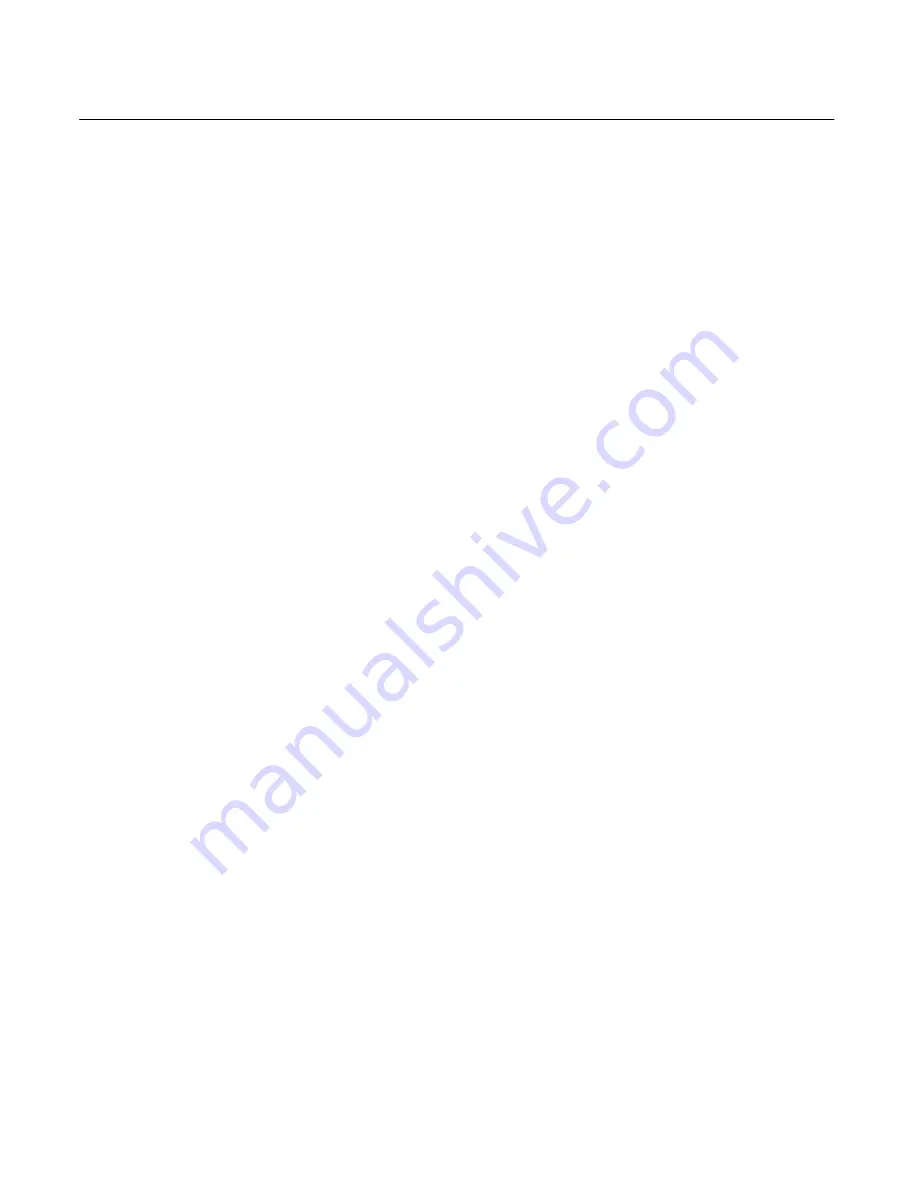
C1 Controllers and Transmitters
Instruction Manual
September 2009
19
Startup: Differential Gap Controllers
Calibrate the controller prior to this procedure.
1. Be sure that the supply pressure regulator is
delivering the proper supply pressure to the
controller.
2. Adjust the proportional band setting for the proper
differential gap (see figure 10).
3. If the controller is used in conjunction with a
control valve, slowly open the upstream and
downstream manual shutoff valves, and close the
bypass valves.
4. To change the differential gap, perform steps 1
through 5 of the calibration for differential gap
controllers procedure.
Transmitter Operation
This section describes the adjustments and
procedures for calibration and startup. Refer to
figure 11 for the adjustment locations. All
adjustments must be made with the cover open.
When the adjustments and calibration procedures
are complete, close and latch the cover.
To better understand the adjustments and overall
operation of the transmitter, refer to the Principle of
Operation section in this manual for transmitters.
Refer also to the schematic diagram in figure 13.
Adjustments
Adjustment: Zero
The pressure setting dial is marked ZERO
ADJUSTMENT PRESSURE SETTING. Zero is in the
center of the dial, and the pressure values increase
to the right and left of the center as shown in figure
11. To set the zero, rotate the pointer around the
pressure setting dial. Rotate the pointer clockwise to
increase or counterclockwise to decrease the output
depending on transmitter action and desired setting.
For direct
−
acting transmitters, zero adjustment
determines the process pressure at which the
transmitter output signal will be at its lower range
limit.
The dial (key 6) graduations are approximate
indications of the transmitter zero setting. When
making adjustments, do not rely solely on the dial
setting. Monitor the process pressure and output
pressure to be sure the desired settings are attained.
Adjustment: Span
The span adjustment is graduated from 0 to 10. A
setting of 10 represents a span setting of 100
percent of the process sensing element range. The
transmitter achieves the highest accuracy when the
span is 100 percent.
The transmitter span adjustment shown in figure 11
is the same as the controller proportional band
adjustment.
Calibration: Transmitters
The output of each transmitter is checked at the
factory before the unit is shipped. The transmitter
provides an output signal that is proportional to the
pressure applied to the sensing element. The output
pressure has no direct effect on the process
pressure.
The transmitter is calibrated at the factory and
should not need additional adjustment. Use the
following calibration procedures when the sensing
element has been changed or other maintenance
procedures have altered the calibration of the
transmitter. The following procedures use a 0.2 to
1.0 bar (3 to 15 psig) output pressure range as an
example. For other output pressure ranges [such as
0.4 to 2.0 bar (6 to 30 psig)] adjust the values to
match the application.
Provide a process pressure source capable of
simulating the process pressure range of the
transmitter. If an output pressure gauge is not
provided, install a suitable pressure gauge for
calibration purposes. Connect a pressure source to
the supply pressure regulator and be sure the
regulator is delivering the correct supply pressure to
the transmitter.
Note
For stability, some transmitter
applications will require additional
volume than just the gauge. Provide a
minimum volume of approximately 25
cm
3
(1.5 in
3
) or greater if stability is a
problem.
Unless otherwise indicated, key number locations
are shown in figure 11.
1. Complete the above connections and provide a
process pressure equal to the sensing element
range.
2. Rotate the span adjustment knob to the
maximum setting on the dial (100 percent span).