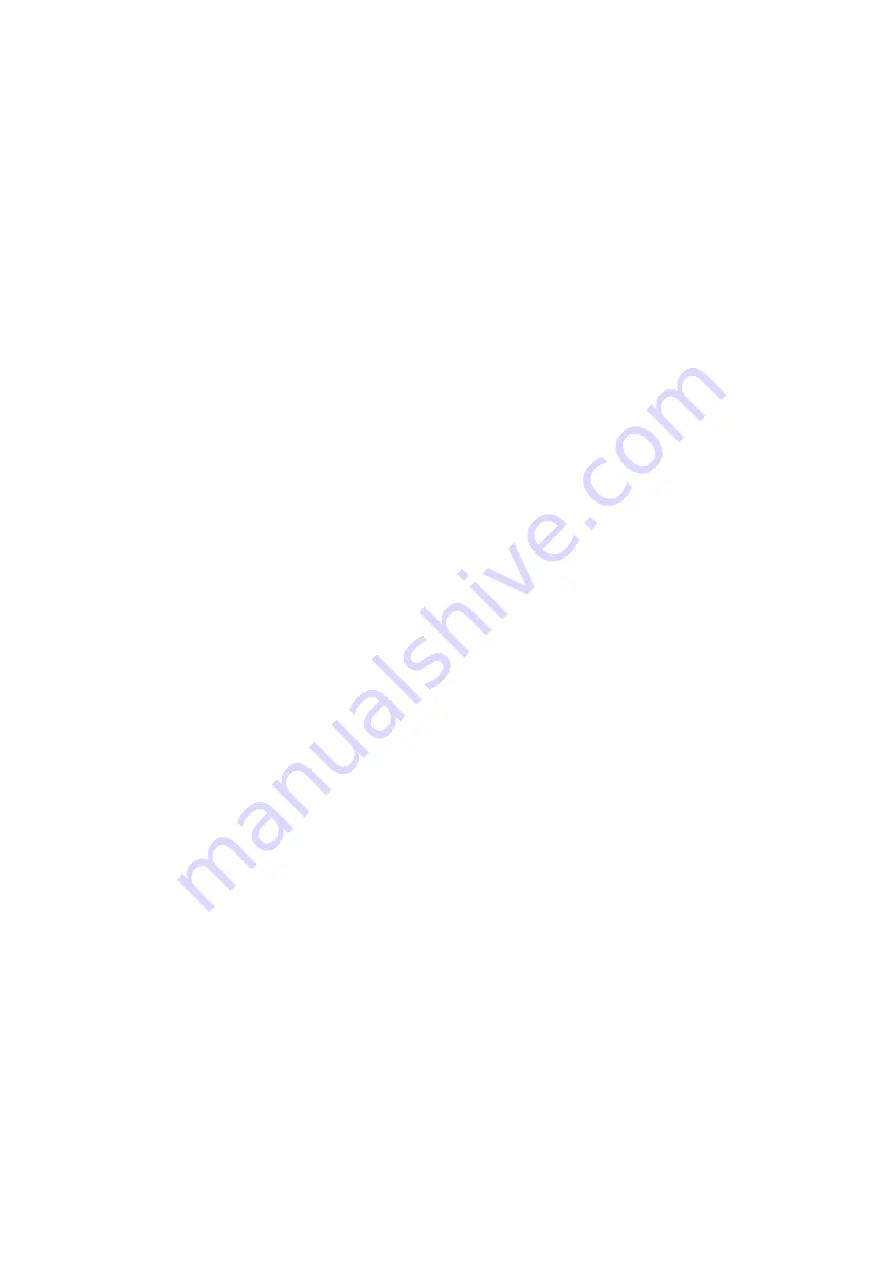
38
05 Insufficient Hot Water (no hot)
Possible causes:
1.
The hot water is not connected or the tap is turned off.
2.
The flow rate is too low. The product requires a minimum flow rate of 6
litres per minute.
3.
The hot water temperature is too low. The water temperature needs to
be 60oC for a hot wash.
4.
The hot water inlet hose is connected to the cold water supply.
5.
That there are kinks in the inlet hose.
6.
The filter in the hot inlet hose at the tap end is blocked.
7.
The filter screen in the hot inlet valve of the machine is blocked.
8.
Thermistor resistance is out of range. Resistance is 10kΩ @ 25 oC.
Replace if well outside of this range.
Note: If the machine is set to controlled cold, hot water may be required
to achieve the set temperature of 20 oC.
06 Insufficient Cold Water (no cold)
Possible causes:
1.
The cold water is not connected or the tap is turned off.
2.
The flow rate is too low. The product requires a minimum flow rate of 6
litres per minute.
3.
The cold water inlet hose is connected to the hot water supply.
4.
That there are kinks in the inlet hoses.
5.
The filter on the cold inlet hose at the tap end is blocked.
6.
The filter screen in the cold inlet valve of the machine is blocked.
7.
Thermistor resistance is out of range. Resistance is 10kΩ @ 25 oC.
Replace if well outside of this range.
07 Agitate Overload (too full)
Possible causes:
1.
The product is overloaded.
2.
The user has selected the wrong water level.
3.
The inner bowl assembly is jammed to the agitator with a foreign object
that may be caught under the agitator skirt.
4.
The spline drive and driven teeth are locked together with dirt, detergent or
lint.
5.
The spline drive and driven teeth are damaged / broken.