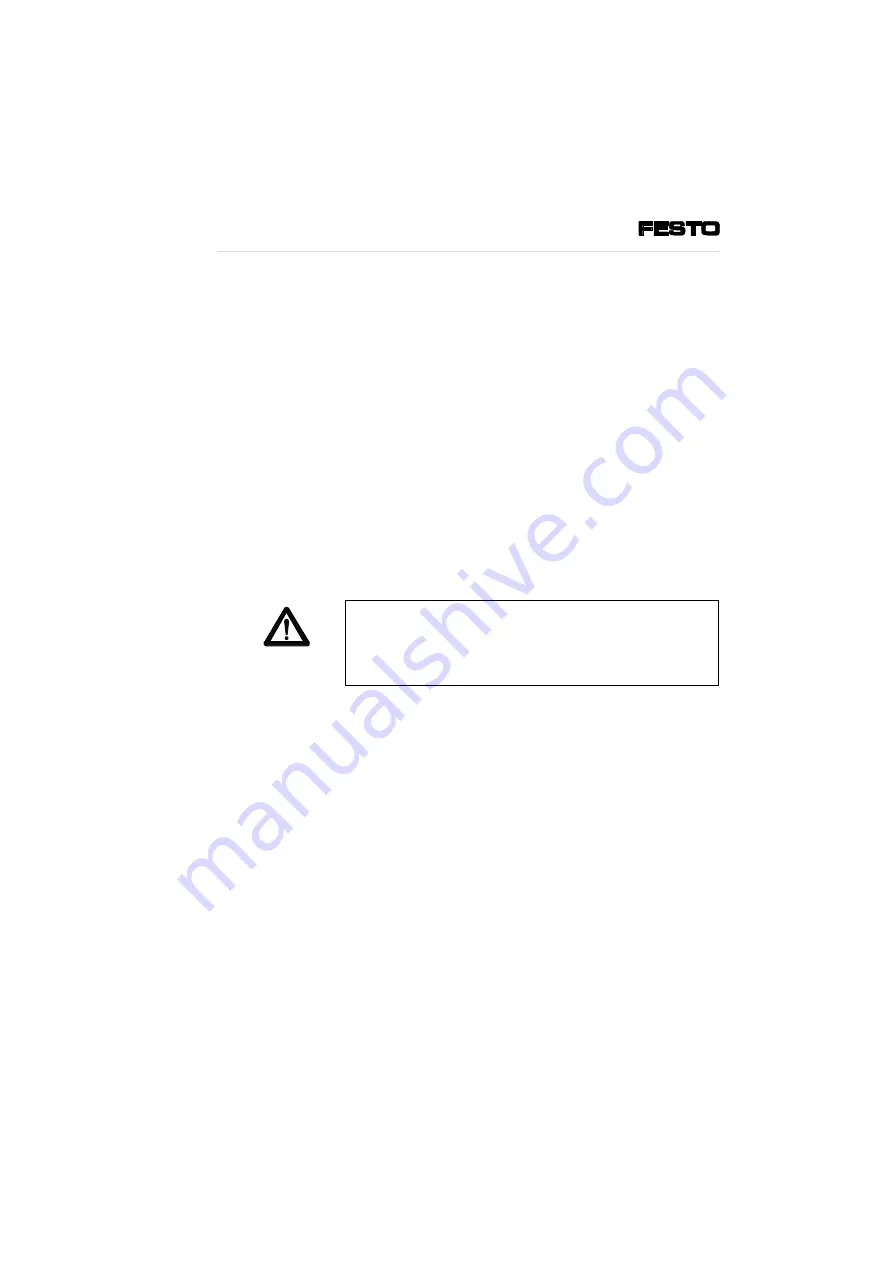
4.4.3 Commissioning on the field bus
Commissioning software for the field bus master usually
provides an online mode in which the current states of
the field bus inputs and outputs can be influenced.
As with commissioning with WinPISA, you can also
generate the control signals of the SPC200 by means
of the PROFIBUS master.
The functionability of the SPC200 on the field bus can
be checked in the online mode of the software for the
PROFIBUS master. The following tables give a sum-
mary of the configurable field bus address range of the
field bus module. The addresses are as seen by the
SPC200.
CAUTION
The outputs of the master are mapped on internal
inputs; internal outputs of the field bus module are
mapped on the inputs of the master.
4. Commissioning
SPC200-COM-PDP 9904NH
4-43
Summary of Contents for SPC200 Series
Page 1: ...Smart Positioning Controller SPC200 Fieldbus module PROFIBUS DP Type SPC200 COM PDP ...
Page 11: ...X SPC200 COM PDP 9904NH ...
Page 12: ...Chapter 1 System summary 1 System summary SPC200 COM PDP 9904NH 1 1 ...
Page 22: ...Chapter 2 Fitting 2 Fitting SPC200 COM PDP 9904NH 2 1 ...
Page 28: ...Chapter 3 Installation 3 Installation SPC200 COM PDP 9904NH 3 1 ...
Page 38: ...Chapter 4 Commissioning 4 Commissioning SPC200 COM PDP 9904NH 4 1 ...
Page 100: ...Appendix A Technical appendix A Technical appendix SPC200 COM PDP 9904NH A 1 ...
Page 103: ...A Technical appendix A 4 SPC200 COM PDP 9904NH ...
Page 107: ...A Technical appendix A 8 SPC200 COM PDP 9904NH ...