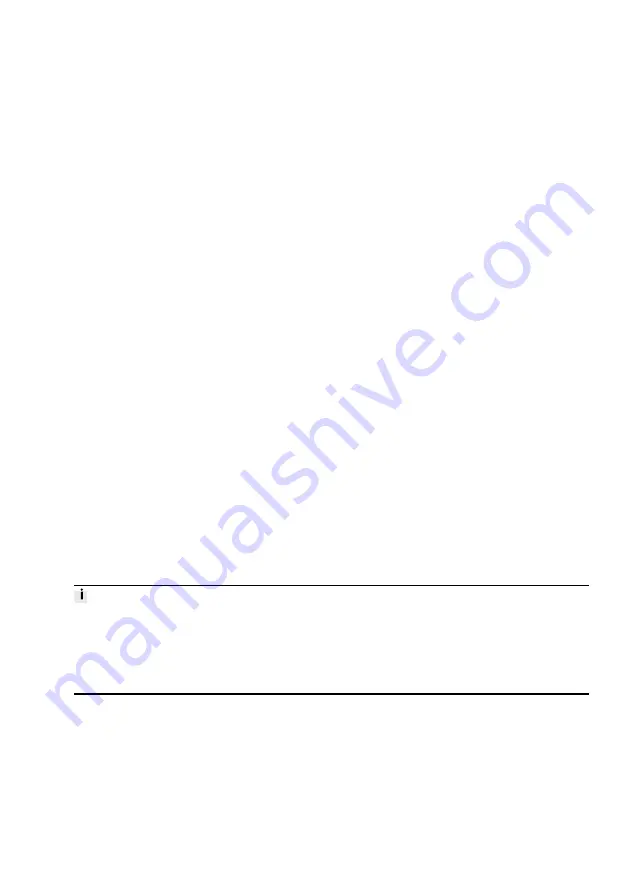
11.3.4
End-to-end operation with press function
11.3.4.1
Function
The drive can be moved to both end positions "Lim
In
/ Lim
Out
" in end-to-end operation with press func-
tion. When moving to the "Lim
Out
" end position the motion is position-controlled to the Start Press
Position "Pos
Start Press
" and then continued force-controlled. The end position "Lim
In
" is approached
exclusively under position control. The EMCS-ST controls the end-to-end operation with press function
via the "digital inputs/outputs (DIO)" or "IO-Link (LK)" [Logic] control interface . The travel direction
to the end position depends on the configuration of the reference end position Ref. The drive can be
stopped at any position of the stroke/angle range "x
In/Out
" with the stop setting. The motion is contin-
ued via the start setting at the control interface. When the end position "Lim
In
/Lim
Out
" or the stop pos-
ition "Pos
Stop
" is reached, the drive stops position-controlled.
The press function is activated via the default "Start Press Position Pos
Start Press
.
end position Lim
Out
".
The specification can be made via the following interfaces:
–
Display and operating components (HMI): "Start Press" menu
–
IO-Link (LK), acyclic process data: position "x
Start Press
", index 0x0105, subindex 0
Control is via the following interfaces:
–
Digital inputs/outputs (DIO)
–
Digital input DI1, "Mov
In
" [Logic]
–
Digital input DI2, "Mov
Out
" [Logic]
–
IO-Link (LK)
è
–
Index 0x0029, subindex 1, "Move
In
"
–
Index 0x0029, subindex 2, "Move
Out
"
The following commands are available:
–
Start
In
: position-controlled and force-controlled motion "Mov
In
" to the end position "Lim
In
(Ref)"
(start/resume)
–
Start
Out
: position-controlled and force-controlled motion "Mov
Out
" to the end position "Lim
Out
"
(start/resume)
–
Stop
In
/Stop
Out
: stop motion
Force is controlled and evaluated by closed-loop control of the motor current. A torque level or a linear
force can be determined from the level of current measured depending on the mechanism of the drive.
The target is set as a percentage of the rated motor current and may deviate from the actual force on
the drive unit. If force levels are set low, the influence of friction in the system on the running beha-
viour and the actual force on the drive unit must also be taken into account.
Motion task Start
In
–
Activation of the motion task DIO: digital input DI1 "Mov
In
" = 1 and DI2 "Mov
Out
" = 0
–
Activation of the motion task IO-Link: parameter 0x0029.1 = true and 0x0029.2 = false or
system parameter 0x0002 (value 0xC8 "Move In")
Drive system
51
Festo — EMCS-ST — 2020-04a
Summary of Contents for EMCS-ST
Page 1: ...8123666 EMCS ST Integrated drive 8123666 2020 04a 8123668 Operating instructions ...
Page 29: ...11 1 2 Dimension reference system Drive system 29 Festo EMCS ST 2020 04a ...
Page 48: ...Fig 22 Single end to end operation Drive system 48 Festo EMCS ST 2020 04a ...
Page 50: ...Fig 23 Stop and continue single end to end motion Drive system 50 Festo EMCS ST 2020 04a ...
Page 54: ...Fig 25 End to end operation with press function Drive system 54 Festo EMCS ST 2020 04a ...