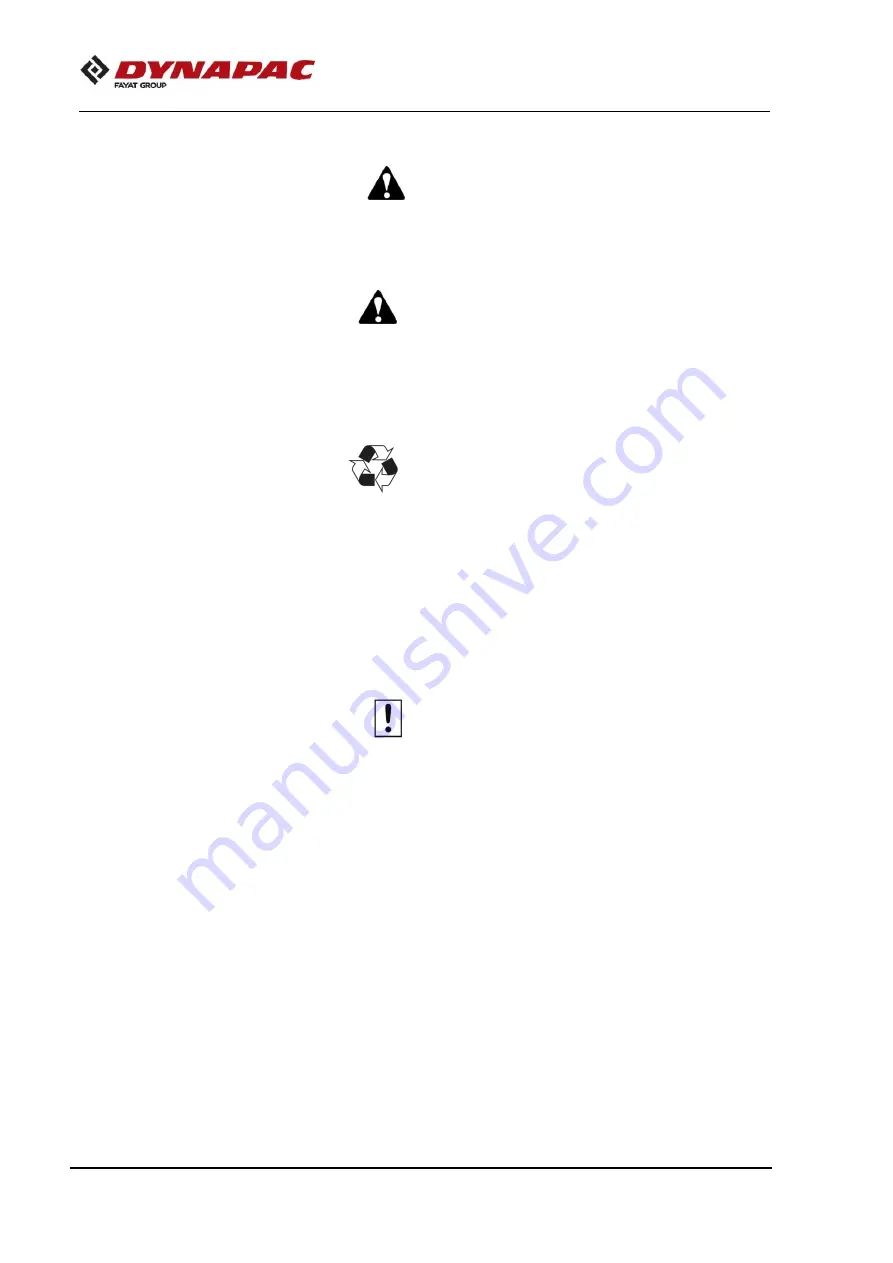
Maintenance
– Annually (Every 2,000 hours of operation)
92
4812325559EN
2018-02-20
Replace the engine coolant.
Caution! Risk of severe burns!
Wait until the engine's temperature is below 122
°F (50 °C) before removing the cap of the coolant
reservoir or draining the cooling system.
1.
Open the expansion reservoir cap.
NEVER open the coolant reservoir cap while the
engine is hot.
2.
Drain the engine cooling system through the radiator drain
valve.
NOTE:
Use a proper container to collect the coolant.
TAKE CARE OF THE ENVIRONMENT: All used
coolant shall be collected and stored properly for
recycling. Do not discard coolant on the soil,
sewerage system or any other location that can
harm the environment.
3.
Fill the system through the expansion reservoir, with the
proper mixture of coolant, according to the item “Symbols
and Lubricants”.
4.
The level of the engine coolant can be visualized through the
reservoir translucent walls, which are located in the engine
compartment, near the radiators. The level should be
between the marks “MIN” and “MAX” when the engine is cold.
During this operation, the coolant of the system is
under pressure and very hot. NEVER open the cap
of the expansion reservoir when the engine is warm.
5.
The coolant should only be refilled when the engine is cold.
If necessary, add coolant when the engine is still warm, wait
10 minutes. Initially turn the cap only once: it does allow the
depressurization of the system. Wait a moment and then
remove the cap completely.
Summary of Contents for DYNAPAC CT3000
Page 2: ...2 4812325559EN 2018 02 20 ...
Page 4: ......
Page 107: ...2018 02 20 4812325559EN 103 ...