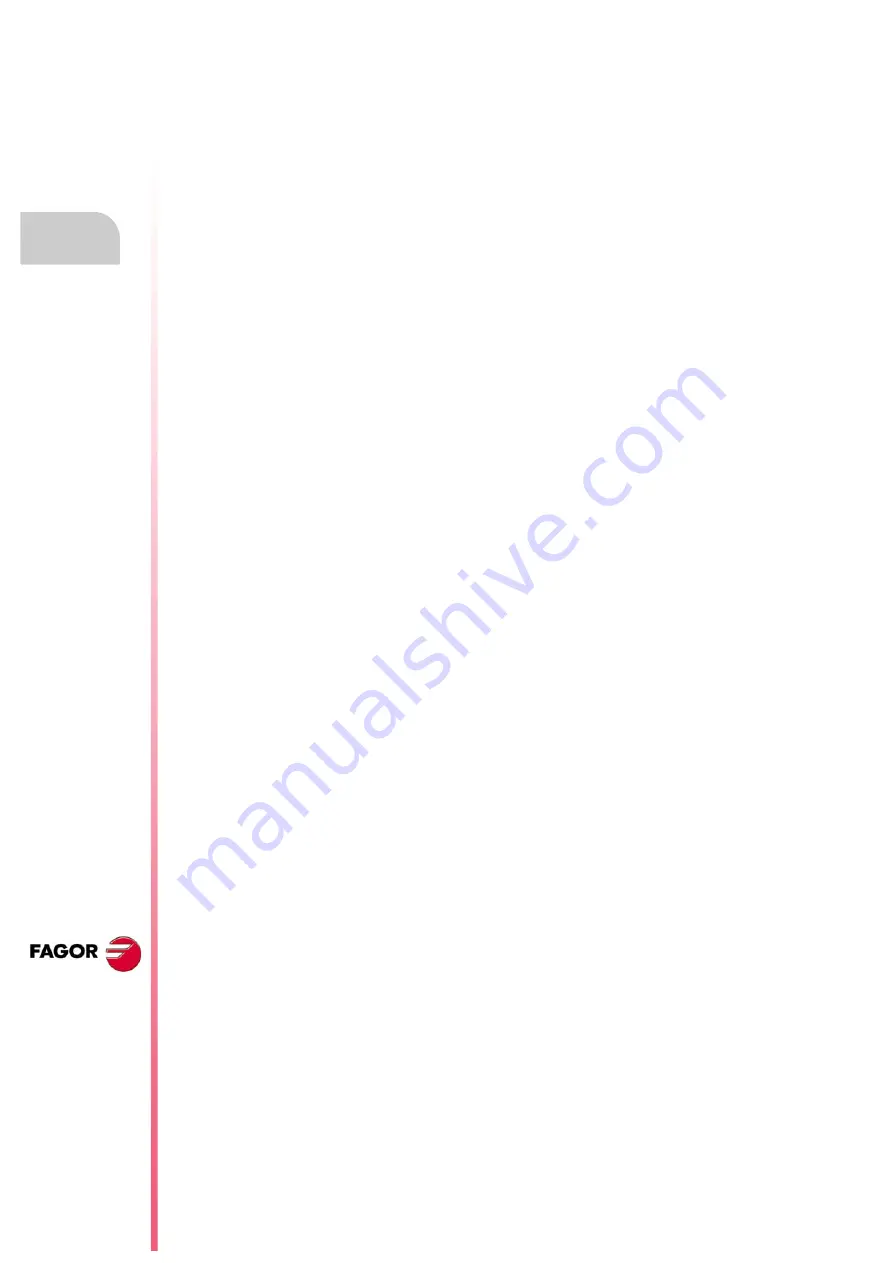
·78·
Remote modules
CNC 8060
CNC 8065
5.
(R
EF
: 1402)
RIOW REMOTE MODULES.
(CANOPEN
PROTOCOL).
Line terminating resistor.
In the CAN bus, it is necessary to use a line terminating resistor to identify which are the
elements that occupy the ends of the bus; i.e. the first and last physical element in the
connection. For the central unit, the terminating resistor is factory installed because the CNC
is always at one end of the bus.
The RIOW series modules do not have a factory-installed line terminating resistor. The RIOW
module mounted at the end of the bus must have a 120
line terminating resistor between
pins CAN_H and CAN_L to avoid signal deflections (rebounds).
Summary of Contents for CNC 8060
Page 1: ...Ref 1402 8060 8065 CNC Remote modules...
Page 6: ......
Page 8: ......
Page 10: ......
Page 12: ......
Page 16: ......
Page 20: ......
Page 22: ......
Page 147: ...Remote modules CNC 8060 CNC 8065 REF 1402 147...
Page 148: ...148 Remote modules CNC 8060 CNC 8065 REF 1402...