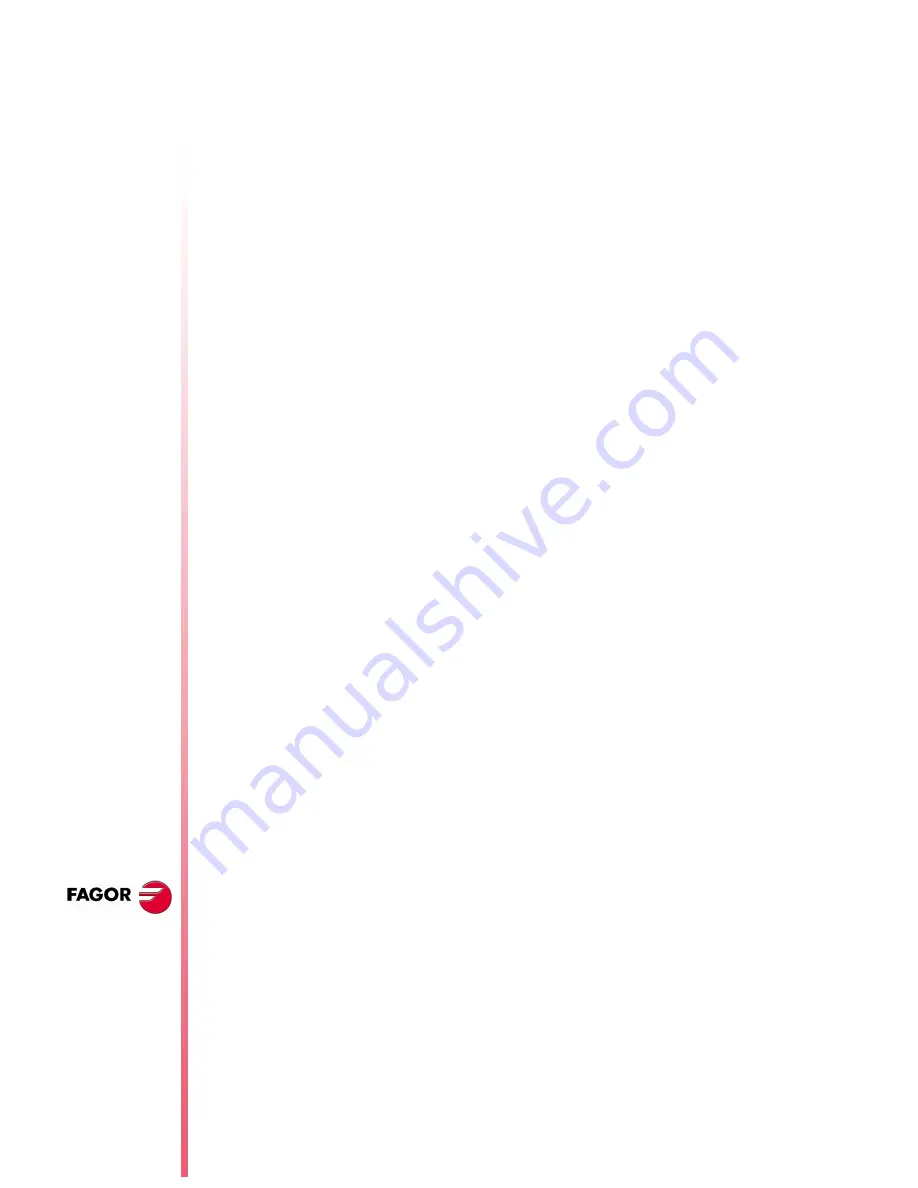
N
EW
F
EATURES
(S
OFT
M: 9.1
X
)
CNC 8
0
5
5
/ CNC 8
0
5
5
i
Page 96 of 106
Variables
The following variable is now available.
ADIOF(X-C)
Additive zero offset referred to machine reference zero. It is read-only
from the CNC, PLC and DNC.
The ADIOF(X-C) values will appear in the zero offset table and they
may be displayed on the following-error screens.
Machine parameter setting
To enable the additive handwheel, set the following machine
parameters and consider the following.
•
If a.m.p. DWELL (P17) has been set and the axis being moved with
the additive handwheel was not already involved in the movement,
it activates the ENABLE mark of the axis and waits a period of time
indicated in DWELL to check whether the SERVO*ON signal has
been activated or not.
•
The acceleration applied to the additive handwheel movement is
that of a.m.p. ACCTIME (P18).
ADIMPG (P176)
This g.m.p. enables the additive handwheel feature. This parameter
has 16 bits that will count from left to right. Each bit has a function
assigned to it. By default, all bits are set to "0". Setting a bit to "1"
activates the corresponding function.
•
Bit 1 indicates whether manual intervention is activated or not.
•
Bit 2 indicates whether the additive zero offset of the handwheel
is canceled or not after an M02 or M30 and after an emergency or
reset.
•
Bit 3 indicates whether manual intervention is enabled with G51 or
not.
•
Bit 4 indicates whether the handwheel resolution is set by
parameter ADIMPRES (P177) or not.
If not, the resolution is set with the switch of the operator panel. If
the switch is not in the handwheel position, it assumes a x1 factor.
ADIMPRES (P177)
This g.m.p. indicates the resolution of the additive handwheel.
ADIFEED (P84)
This a.m.p. indicates the maximum feedrate allowed due to the
additive movement.
By default 1000.0 mm or degrees/min (inch/min).
DIPLCOF (P110)
This g.m.p. indicates how the coordinates will be displayed and how
to access variables POS and TPOS.
0
0.001mm or 0.0001 inch. (Default value 0)
1
0.01mm or 0.001 inch.
2
0.1mm or 0.01 inch.
0
When displaying the position of the axes referred to home, it only takes
into account the additive offset when displaying the coordinates
referred to machine reference zero. The coordinate returned by the
POS(X-C) and TPOS(X-C) variables takes into account the additive
offset due to the handwheel.
1
When displaying the position of the axes, it ignores the additive offset
due to the handwheel. The coordinate returned by POS(X-C) and
TPOS(X-C) ignores that offset.
2
When displaying the position of the axes, the CNC takes into account
the additive offset set by the handwheel except when showing the
Command - Actual - To go coordinates. The coordinate returned by
the POS(X-C) and TPOS(X-C) variables takes into account the
additive zero offset.
Summary of Contents for CNC 8055
Page 1: ...REF 0307 SOFT M 7 XX SOFT M 7 1X CNC 8055 CNC 8055i NEW FEATURES ...
Page 2: ...Pág 2 de 2 CNC 8055 CNC 8055i NEW FEATURES SOFT M 7 XX SOFT M 7 1X ...
Page 45: ...User notes NEW FEATURES SOFT M 7 XX Page 41 of 50 CNC 8055 CNC 8055i ...
Page 46: ...User notes NEW FEATURES SOFT M 7 XX Page 42 of 50 CNC 8055 CNC 8055i ...
Page 53: ...User notes NEW FEATURES SOFT M 7 1X Page 49 of 50 CNC 8055 CNC 8055i ...
Page 54: ...User notes NEW FEATURES SOFT M 7 1X Page 50 of 50 CNC 8055 CNC 8055i ...
Page 56: ......
Page 60: ......
Page 114: ...Page 54 of 106 CNC 8055 CNC 8055i NEW FEATURES SOFT M 9 0X User notes ...
Page 162: ...Page 102 of 106 CNC 8055 CNC 8055i NEW FEATURES SOFT M 9 1X User notes ...
Page 165: ...Page 105 of 106 CNC 8055 CNC 8055i NEW FEATURES SOFT M 9 1X User notes ...
Page 166: ...Page 106 of 106 CNC 8055 CNC 8055i NEW FEATURES SOFT M 9 1X User notes ...