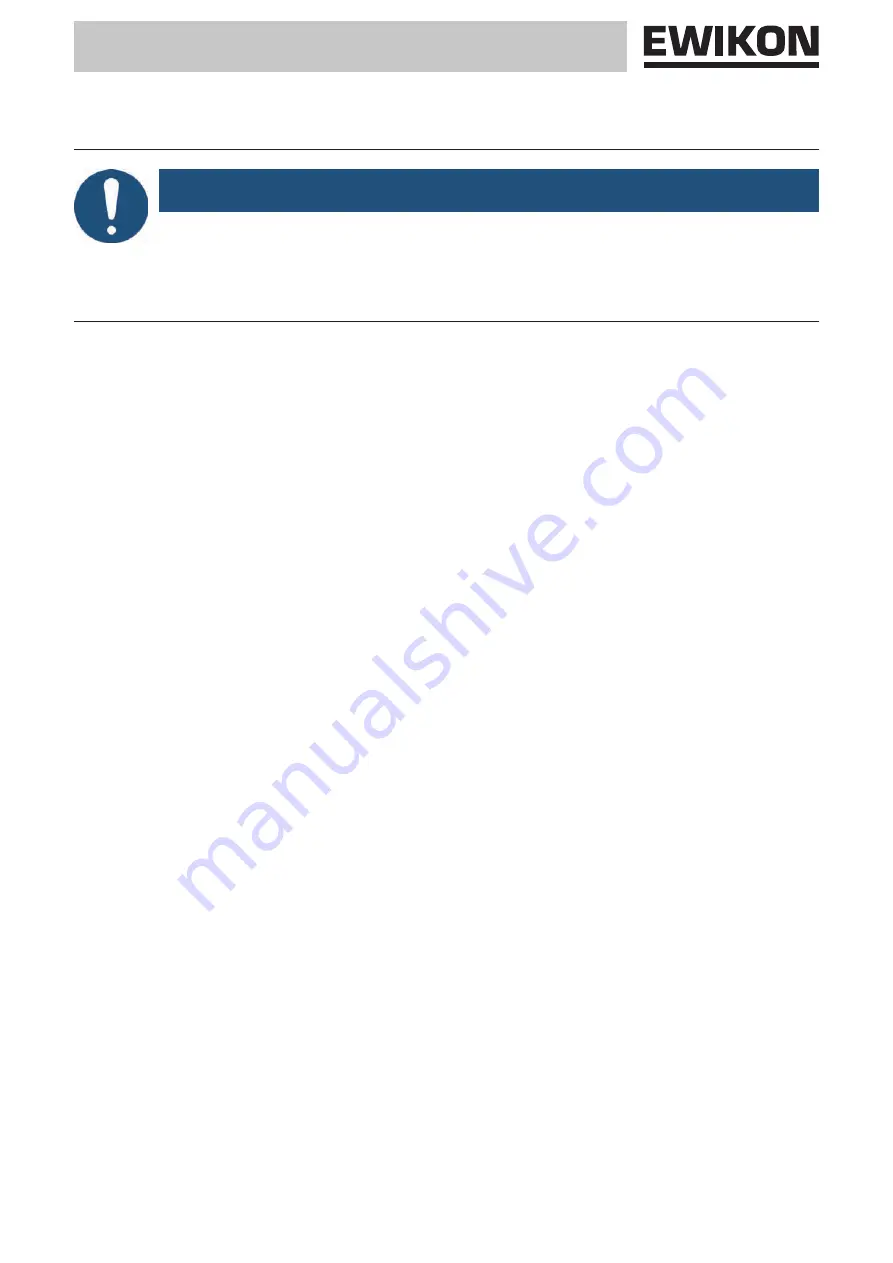
57
HPS-III-Heißkanalsystem_Inbetriebnahme-System-Einzeldüsen-L2X-NV_BA_V-2-0_EN
Start-up of a HPS III hot runner system
6.3 Start-up of a HPS III hot runner system
6.3.1
First-time start-up and filling of a HPS III hot runner system
•
Switch on the mould cooling.
•
Mould and barrel should have reached the recommended temperatures.
•
Switch on the hot runner and let the humidity from the heaters dry out at a temperature between 100 °C and 120 °C
for approx. 10 minutes (sequential start /compound heating mode of the controller).
•
Set processing temperature and heat system for 3 - 5 minutes (sequential start /compound heating mode) so that the
preload is ensured.
•
Make sure that there is a sufficient barrel pressure. Without that leakage might occur between machine nozzle and
mould. Fill the hot runner with approx. 300 - 400 bar back pressure until plastic emerges at the gates.
•
When filling the hot runner system use natural material without additives especially if colour changes are planned or if
materials with flame retardant additives and glass fibres respectively are used.
•
Start moulding process.
•
If intense mould cooling is required increase temperature by approx. 20 °C - 25 °C if necessary.
6.3.2
Start-up of an already filled HPS III hot runner system
•
Switch on the mould cooling.
•
Mould and barrel should have reached the recommended temperatures.
•
Switch on the hot runner and let the humidity from the heaters dry out at a temperature between 100 °C and 120 °C
for approx. 10 minutes (sequential start /compound heating mode of the controller).
•
Set processing temperature and heat system for 3 - 5 minutes (sequential start /compound heating mode) so that the
preload is ensured.
•
When material melts at the sprue bush remove cold slug and purge machine barrel – then start up mould.
•
Start moulding process.
•
If intense mould cooling is required increase temperature by approx. 20 °C - 25 °C if necessary.
6.3.3 Colour and material changes
1.
In order to successfully carry out a colour change the hot runner system needs to be filled with natural material.
2.
Fill the hot runner system as described under „6.3.1 First-time start-up and filling of a HPS III hot runner system“ .
3.
Mould articles using the first colour.
4. For the colour change increase barrel temperature by 20 - 40 °C and change to natural material.
5.
Purge the barrel with natural material first, then purge the hot runner system and the barrel together with natural material.
6. When approx. 95% of the purged material contains of natural material, increase the temperature of the hot runner
by 30 - 50 °C and continue to purge with natural material until no further improvement can be achieved.
7. Set temperature back to standard settings.
8. Start moulding with new colour.
NOTE!
In general the start-up of a hot runner system with
HPS III single tips
, a
L2X system
as well as a
valve gate
system
is carried out analougosly to the start-up of a system with HPS III-S nozzles. Possible differences are
specified in the text. Please pay special attention to the instructions for operating a valve gate sytem in chapter
„6.4 Instructions for the operation of valve gate systems“.