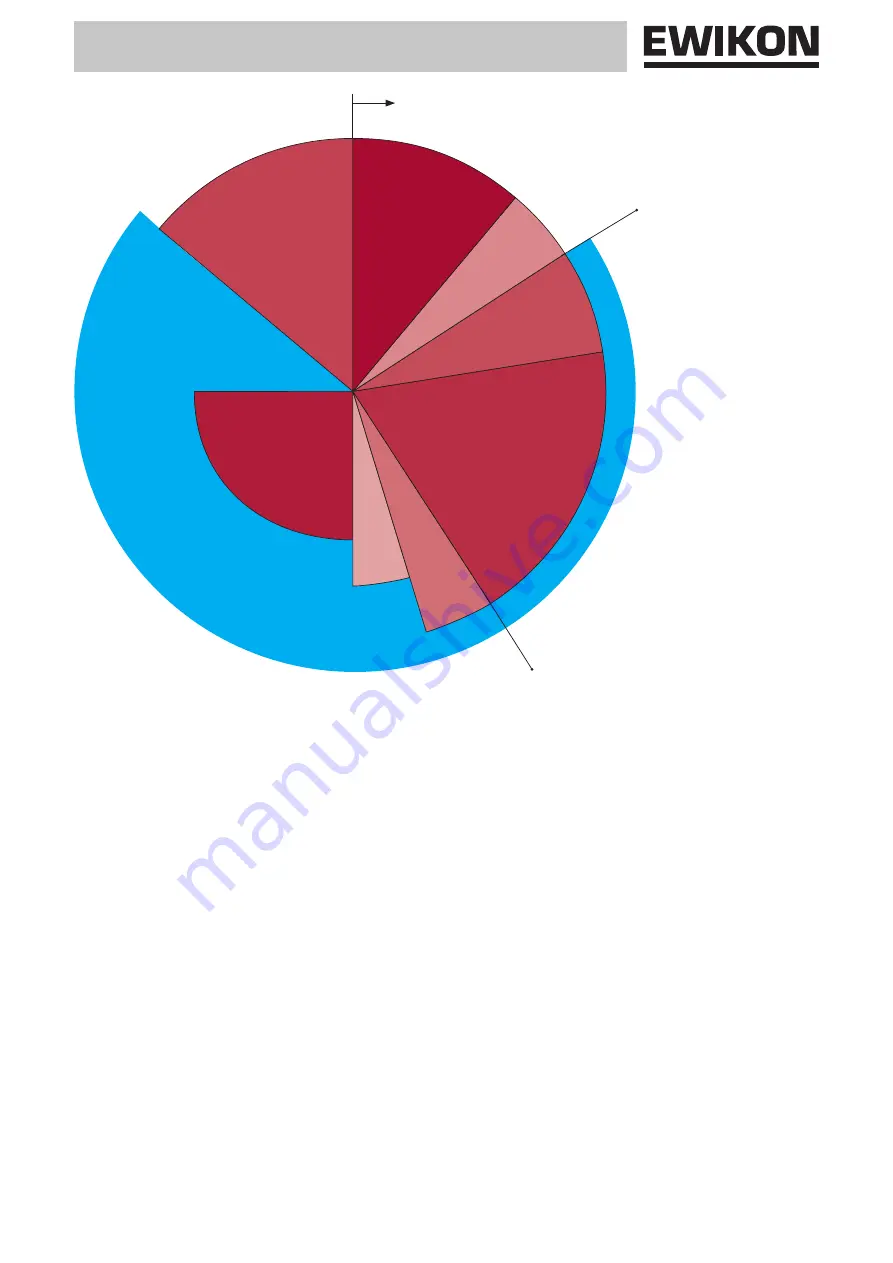
19
HPS-III-Heißkanalsystem_Vorspann_BA_V-2-0_EN
Functional description of the HPS III hot runner system
Picture 3: Injection moulding cycle
* for valve gate systems
** recommended for open systems
A hot runner system is used to distribute plastic melt between the injection moulding unit of an injection moulding machine
and the cavities of an injection mould (compare picture 2). The plastic material remains permanently molten until it enters the
cavities.
The plastic melt made available by the injection moulding unit is guided through the sprue bush to the manifold during the
injection moulding cycle. In the manifold the melt stream for the individual cavities is split and fed to the hot runner nozzles.
The hot runner nozzles guide the melt stream to the cooled cavities (compare picture 3).
If a valve gate system is used, the valve pins are opened when injection starts. While the moulded parts continue to cool
down a holding pressure phase to compensate shrinkage follows after the injection phase with a continued, usually pressu-
re-regulated melt transport into the cavity (compare picture 3). After the moulded part has solidified to such an extent that no
new material can enter the cavity, the holding pressure phase has finished and the moulded parts cool down until they reach
a safe demoulding temperature.
If a valve gate system is used the opening towards the cavity (gate) will be closed again by a movement of the valve pins
after the holding pressure phase has been finished (compare picture 3). If open systems are used, a decompression phase
will follow to prevent plastic melt from leaking from the gate area. While the moulded parts continue to cool down in the
cavity the injection moulding machine can prepare the melt for the next cycle. After the demoulding temperature has been
reached, the injection mould opens and the solidified parts are ejected.
Cooling
Start of cycle
Valve gate nozzle(s)
open(s)*
Valve gate nozzle(s) close(s)*
Mould closing
Buildup of barrel
pressure
Injecting
Holding pressure
Reduction of barrel
pressure
Dosing
Mould opening,
ejecting
Decompression**