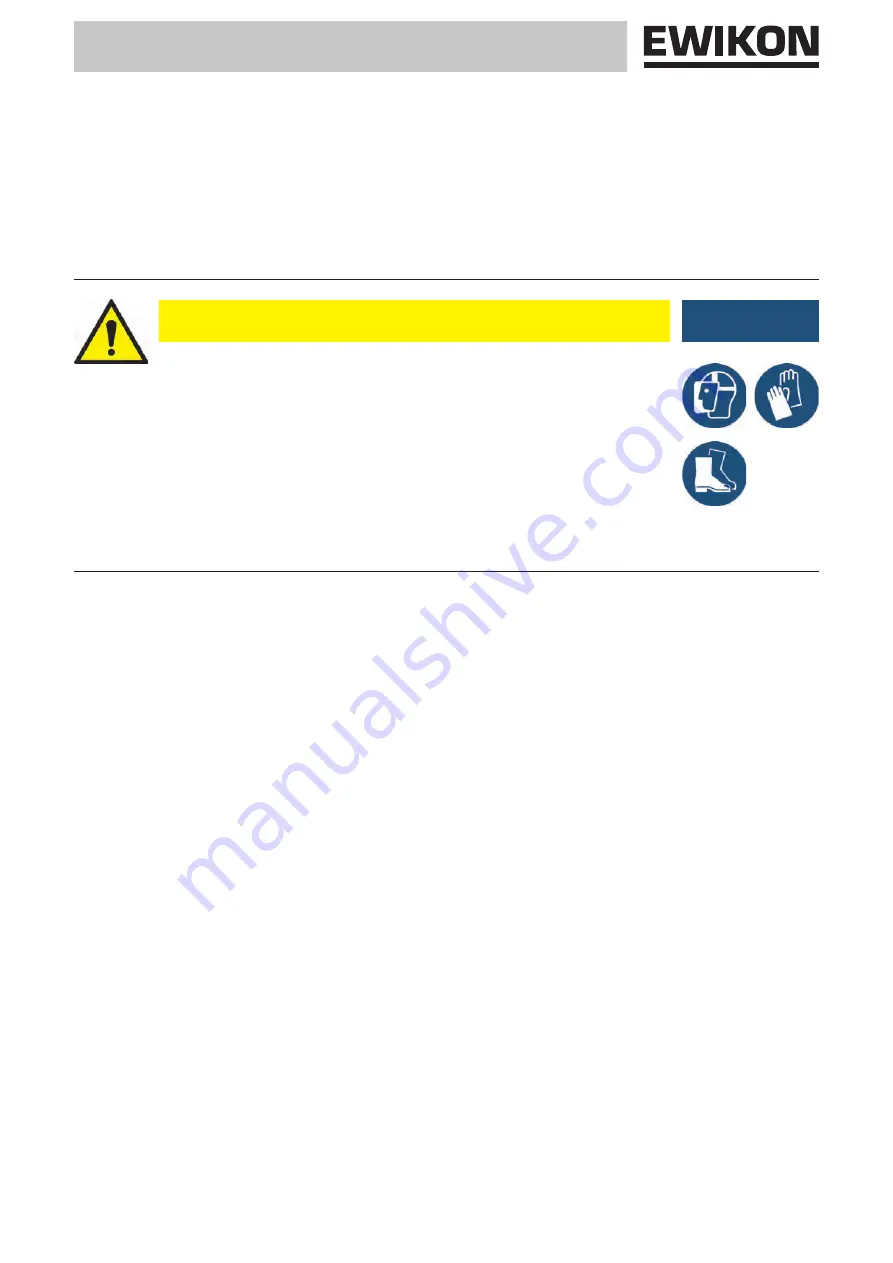
53
HPS-III-Heißkanalsystem_Elektro-Nach-Einbau_BA_V-2-0_EN
Checks after installation
5.7 Checks after installation
To be checked in cold condition
•
Bores and connections for media (e.g. cooling circuits, hydraulic circuits) (optical check)
•
Allocation of wiring according to the wiring scheme (see order specific documents)
•
Resistance of the protective earth conductor
•
Insulation resistances of the heating zones
•
Check of cooling (function, correct piping): Are all components that require cooling supplied with water (is the flow rate
sufficient)?
Ckeck of heaters by heating the HPS III hot runner system to operating temperature
•
Switch on the mould cooling.
•
Check if the thermocouple and power connections are allocated correctly by heating up each zone separately
(for a short time)
•
Check response of the respective thermocouple
•
When using a EWIKON controller this procedure can be automatically carried out by using the diagnosis function.
To be checked in heated condition (operating temperature)
•
Leak tightness and function of drive units (hydraulic fluid, pressurised air) by repeatedly moving the valve pin to the end
positions in manual mode while the mould is opened.
•
Valve pin position (move valve pin to end position „closed“).
•
Valve pin function (move valve pin repeatedly into end positions „open“ and „closed“).
•
Leak tightness and function of mould cooling.
CAUTION!
PPE
Respect operating temperatures
For all further checks the HPS III hot runner system must be heated to operating tem-
perature in order to avoid damage to hot runner components.
Each hot runner system is individually designed for the material to be processed.
Therefore, the specified operating temperatures must be observed. The temperature
difference ∆T between hot runner temperature T
HK (processing temperature) and
mould temperature TWZ, must be strictly adhered to.
•
Non-observance may cause an escape of melt inside the mould (∆T too low) or
damage to components (∆T too large).