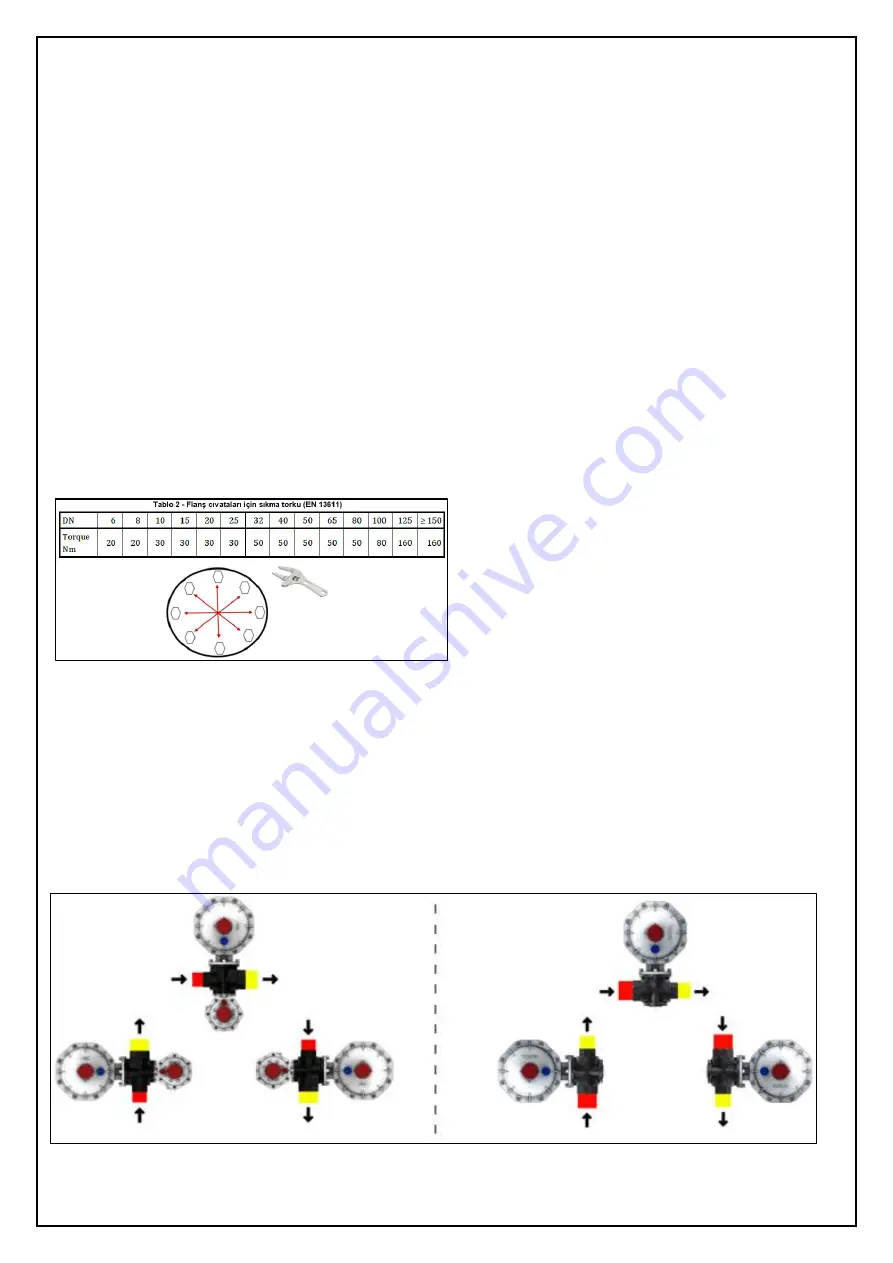
Page
8
of
32
While connecting the product to the line; place it in such way that the product shall not block the front of the sensing line. Pay attention
to the specified distance of the measuring point for the sensing line. While connecting the product to the line; use appropriate wrenches
for tightening inlet and outlet connections and make sure that no excessive load, force and impact is applied and that external leakage
is prevented. Pipe connections should always be welded to the upper part of the pipe, and the hole in the pipe should not show any burrs
or protrusions inwards. Ensure that there is no pressure gas trapped in the line where the product will be installed and between the line
and the product, that the gas supply is turned off and that the possibility of opening is completely prevented. After tightening, make the
controls that the connections are fully seated in the sockets and there are no cracks, breakages, etc., mechanical problems and
deformations in the connections and in the product and that no mechanical stress caused by the line, pipe and connection has occurred.
If connection components which are larger than the connection diameter on the body of the product are installed in the inlet and outlet
of the product for assembly, forces and moments exceeding the values required by the main connection diameter on the body should
not be applied and limitations should not be exceeded.
While screwing the product on the line, make sure that the pipe thread is not too long in order to prevent damage on the body. If the
product is modularly flanged; make sure that the inlet and outlet counter flanges are perfectly coaxial and parallel in order to avoid
unnecessary mechanical pressure on the product body. Also calculate the space required to place the seal. As the product may be
disassembled from the installation for testing, repair, maintenance, replacement and similar purposes, use a gland or ball valves at the
product inlet and outlet. Connect the product to the line without causing mechanical stress. It should be remembered that excessive
loads to be applied to the body may lead to cracks. For these reasons, assemble with wrenches. For products with flanges, follow the
mounting torques shown in chart 2. For tightening operations, make available single or double calibrated torque wrenches or other
controlled locking tools. After tightening, make the controls that the connections are fully seated in the sockets and there are no cracks,
breakages, etc., mechanical problems and deformations in the connections and in the product and that no mechanical stress caused by
the line, pipe and connection has occurred.
The necessary gaps and spaces should be left around the product and between the wall and the product by taking the outer dimensions
of the product as reference, in order to enable access
to the product’s
components, perform the necessary operations and carry out
testing. If the product is accessible to unauthorized persons, provide protection against impact or accidental contact. During installation,
make sure that the gas in front of the product is turned off. Close the gas cutting valves at the line inlet and outlet. Make sure there are
no gas flows. While mounting the product on the line; connection shall be in the direction of the arrow indicated on the product. The
arrow on the product shall be mounted in such way that the outlet side shall indicate the user, that means it shall show the gas flow
direction. By this, the flow will be from the network to the user.
- Install the product in horizontal or vertical position with a tolerance of ±5
o
C at the appropriate mounting position as shown in figure 3.
However, it should be preferred to install in such way that the cover shall be vertical with an upwards direction. The mounting position
for dry gases may be vertical or horizontal provided that the outlet pressure regulation part shall not be downwards and mounting
pos
ition for LPG shall in such way that the regulator’s outlet side shall be downwards.
Figure 3
Summary of Contents for ERG-H5
Page 19: ...Page 19 of 32 Figure 11...
Page 20: ...Page 20 of 32...