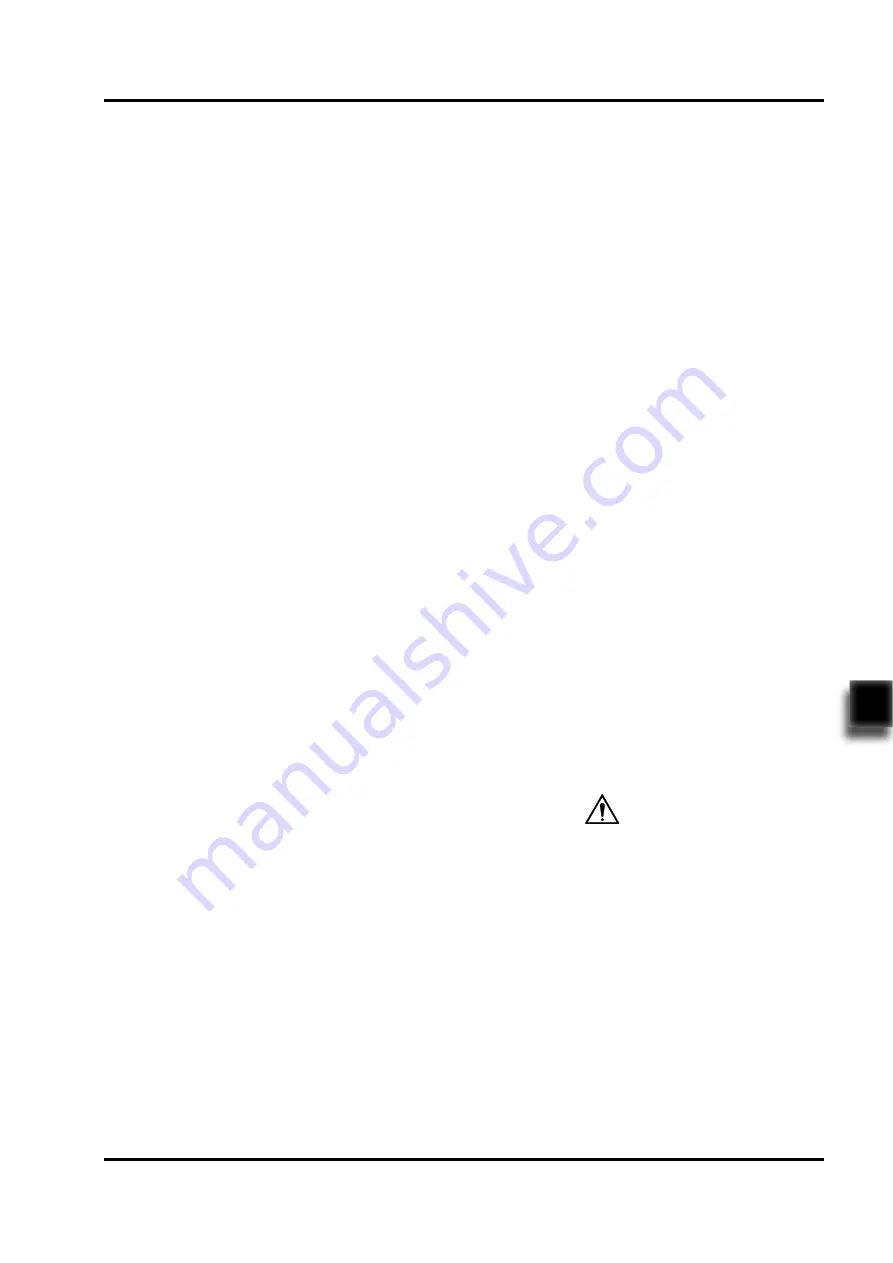
71
REV. 05/2020
HYDRAULIC SYSTEM
7
7.1 Overview
The system pressure of the entire hydraulic
system pressure is provided by hydraulic power
unit system, which is used for lifting. While the
hydraulic power unit is equipped with a relief
valve to ensure that the entire system pressure
is always within the safety limits that can lift the
maximum load capacity.
Solenoid valve on the valve body is used for the
control of lowering. Throttle valve is used for the
control of lowering speed. Inlet is equipped with
a filter to prevent the impurities in the hydraulic
oil from entering into the pump.
Oil pipeline explosion-proof valve is installed at
the hydraulic cylinder to prevent the free falling
of the load after system failure.
Hydraulic Schematic Diagram is as shown in
Fig3131-40001SM;
See Section 7.11 for hydraulic symbol descripti-
ons.
-
-
-
-
Lower the mast to the bottom, remove the air
filter on cylinder, observe the oil level with the
oil dipstick. When adding hydraulic oil, please
use hydraulic oil of the same specifications.
When the mast occasionally jitters, that may
be leaks in the cylinder, or there could be
leaks on the valve body. Dismantle and clean
(to clean with hydraulic oil of the same spe-
cifications) the valve on the valve body, disch-
arge the foreign bodies within the valve body
through repeatedly lifting and lowering of the
mast.
If hydraulic oil is becoming less, please tho-
roughly check the hydraulic system for leaks.
Disassembly of cylinder needs to be perfor-
med in a clean environment. Before removing
the cylinder, the stains on the cylinder must
be removed first. Carefully remove the piston
rod to prevent the cylinder wall from being
scratched by its end surface or damaged
part. Every time when replacing the cylinder,
also replace the cylinder seals.
Hydraulic Oil
Hydraulic oil for truck:
Specifications: Anti-wear Hydraulic Oil L-HM46.
* For cold storage: Low Temperature Anti-wear
Hydraulic Oil L-HV32.
Hydraulic Seals
The seals installed within the cylinder are made
of rigid polyurethane. The deformation during
assembly due to compression will not cause a
permanent deformation.
When assembling, pay attention to prevent the
seals from being broken, rolled and undercut.
Assembly Instructions
The tools used to install the seals must be made
of soft metal or suitable plastic, without burrs
and sharp edges on surfaces. It is prohibited
to use the tools that can easily damage the
surface of seals, such as, screwdriver or other
similar tools with hard front edges.
Where the hydraulic seals to be installed should
be free of burrs, sharp edges and cracks. If the
installation of seals needs to cross sharp edges,
grooves or cuts, protective devices must be
used for protection. Before installing, lubrication
should be performed to the seals and the
mounting positions first.
The lubricant used during assembly must be of
the same specifications with the hydraulic oil
used in the vehicle.
CAUTION
Summary of Contents for CPD30L1-B
Page 1: ...Service Manual Electric Forklift Truck CPD30 35L1 B CPD30 35L1 S ...
Page 2: ...Service Manual Electric Forklift Truck CPD30 35L1 B CPD30 35L1 S ...
Page 13: ...1 1 1 INFORMATION SPECIFICATIONS ...
Page 14: ...2 NOTE ...
Page 20: ...REV 05 2020 INFORMATION SPECIFICATIONS 1 8 ...
Page 21: ...9 2 2 MAINTENANCE ...
Page 22: ...10 NOTE ...
Page 31: ...19 3 3 STRUCTURE FUNCTIONS ...
Page 32: ...20 NOTE ...
Page 39: ...27 4 4 CHASSIS SYSTEM ...
Page 40: ...28 NOTE ...
Page 46: ...34 REV 05 2020 CHASSIS SYSTEM 4 ...
Page 47: ...35 5 5 DRIVE SYSTEM ...
Page 48: ...36 NOTE ...
Page 49: ...37 REV 05 2020 DRIVE SYSTEM 5 Drive System No Name 1 Drive Wheel 2 Gearbox 3 Drive Motor ...
Page 55: ...43 REV 05 2020 DRIVE SYSTEM 5 For CPD30 35L1 S see Fig3131 20012SM ...
Page 61: ...49 6 6 OPERATING SYSTEM ...
Page 62: ...50 NOTE ...
Page 68: ...56 REV 05 2020 OPERATING SYSTEM 6 For CPD30 35L1 S Fig3131 30008SM ...
Page 80: ...68 REV 05 2020 OPERATING SYSTEM 6 ...
Page 81: ...69 7 7 HYDRAULIC SYSTEM ...
Page 82: ...70 NOTE ...
Page 84: ...72 REV 05 2020 HYDRAULIC SYSTEM 7 7 1 1 Hydraulic Schematic Diagram ...
Page 89: ...77 REV 05 2020 HYDRAULIC SYSTEM 7 ...
Page 101: ...89 8 8 STEERING SYSTEM ...
Page 102: ...90 NOTE ...
Page 107: ...REV 05 2020 STEERING SYSYTEM 8 95 ...
Page 109: ...97 9 9 ELECTRICAL SYSTEM ...
Page 110: ...98 NOTE ...
Page 183: ...REV 05 2020 ELECTRICAL SYSTEM 9 171 9 13 Electrical Schematic Diagrams CPD30 35L1 B ...
Page 185: ...REV 05 2020 ELECTRICAL SYSTEM 9 173 9 15 Wiring Harness and Connectors CPD30 35L1 B ...
Page 186: ...REV 05 2020 ELECTRICAL SYSTEM 9 174 9 16 Wiring Harness and Connectors CPD30 35L1 S ...
Page 187: ...175 10 10 TROUBLESHOOTING ...
Page 188: ...176 NOTE ...
Page 194: ...REV 05 2020 TROUBLESHOOTING 10 182 ...
Page 195: ...183 APPENDIX ...
Page 196: ...184 NOTE ...
Page 197: ...185 A A SERVICE MANUAL MAST ...
Page 198: ...186 NOTE ...
Page 213: ...201 REV 05 2020 SERVICE MANUAL MAST A ...
Page 220: ...208 REV 05 2020 SERVICE MANUAL MAST A ...
Page 226: ...214 REV 05 2020 SERVICE MANUAL MAST A ...
Page 227: ...215 B B SERVICE MANUAL BATTERY ...
Page 228: ...216 NOTE ...
Page 232: ...220 C C SCHEDULE ...
Page 233: ...221 ...
Page 235: ......