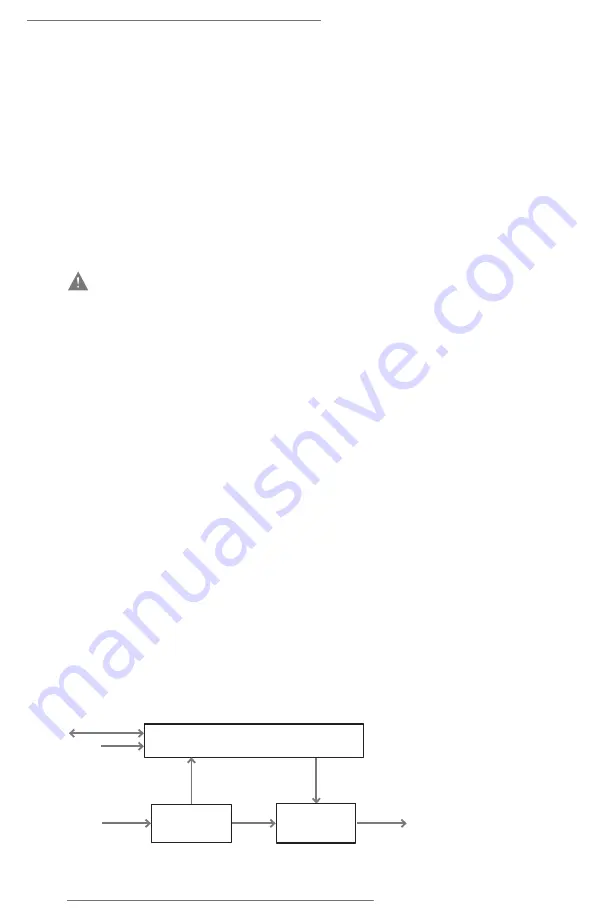
NT INTEGRATED FLOW CONTROLLER WITH DEVICENET COMMUNICATION
2
User Guide | Entegris, Inc.
Introduction
This manual is for use with standard
NT
TM
Integrated Flow Controllers with
DeviceNet
TM
communication, Model
6500. These instruments have been
designed for use in high-purity appli-
cations in the semiconductor industry.
The wetted parts are constructed
with PTFE, PFA or other similar
high-purity inert materials.
WARNING! Attempting to install
or operate standard NT Integrated
Flow Controllers without review-
ing the instructions contained
in this manual could result in
personal injury or equipment
damage.
IDENTIFYING NONSTANDARD
PRODUCT CONFIGURATIONS
—
This User Guide applies to product
manufactured as the standard NT
Integrated Flow Controller. Entegris
also manufactures nonstandard prod-
uct to meet the needs of specific
applications. Nonstandard product
may have different materials of con-
struction, accuracy specifications,
performance and other specifications
that differentiate the nonstandard
product from the standard offering.
NOTE: Nonstandard NT Integrated Flow
Controllers may be identified by the
model number found on the product
label. Specifications for nonstandard
NT Integrated Flow Controllers are
available by contacting Entegris.
Nonstandard NT Integrated Flow
Controllers, Model 6500 product line,
are identified with an
“M"
followed by
a number code.
Example part number:
6500-T2-F02-AM12-D-P7-U3-M02
The “M02" designates the product
as a nonstandard product manu-
factured to certain specifications
designated under the “M02" code.
PRINCIPLE OF OPERATION
—
The user provides a setpoint signal
that corresponds to the desired
amount of flow. The standard NT
Integrated Flow Controller compares
the setpoint to the actual flow signal
from the flow module. If the actual
flow is greater than the setpoint, the
unit closes the valve. If the actual
flow is less than the setpoint, the unit
opens the valve. The flow controller
does this in a precise manner until
the actual flow signal is equal to the
setpoint.
IFC control interface
MAC ID, baud rate, status LEDs
Flow module
Valve module
Valve
control
Fluid flow
Fluid flow
Fluid flow
Power
DeviceNet I/O
Flow and pressure
measurement
Figure 1. System block diagram.