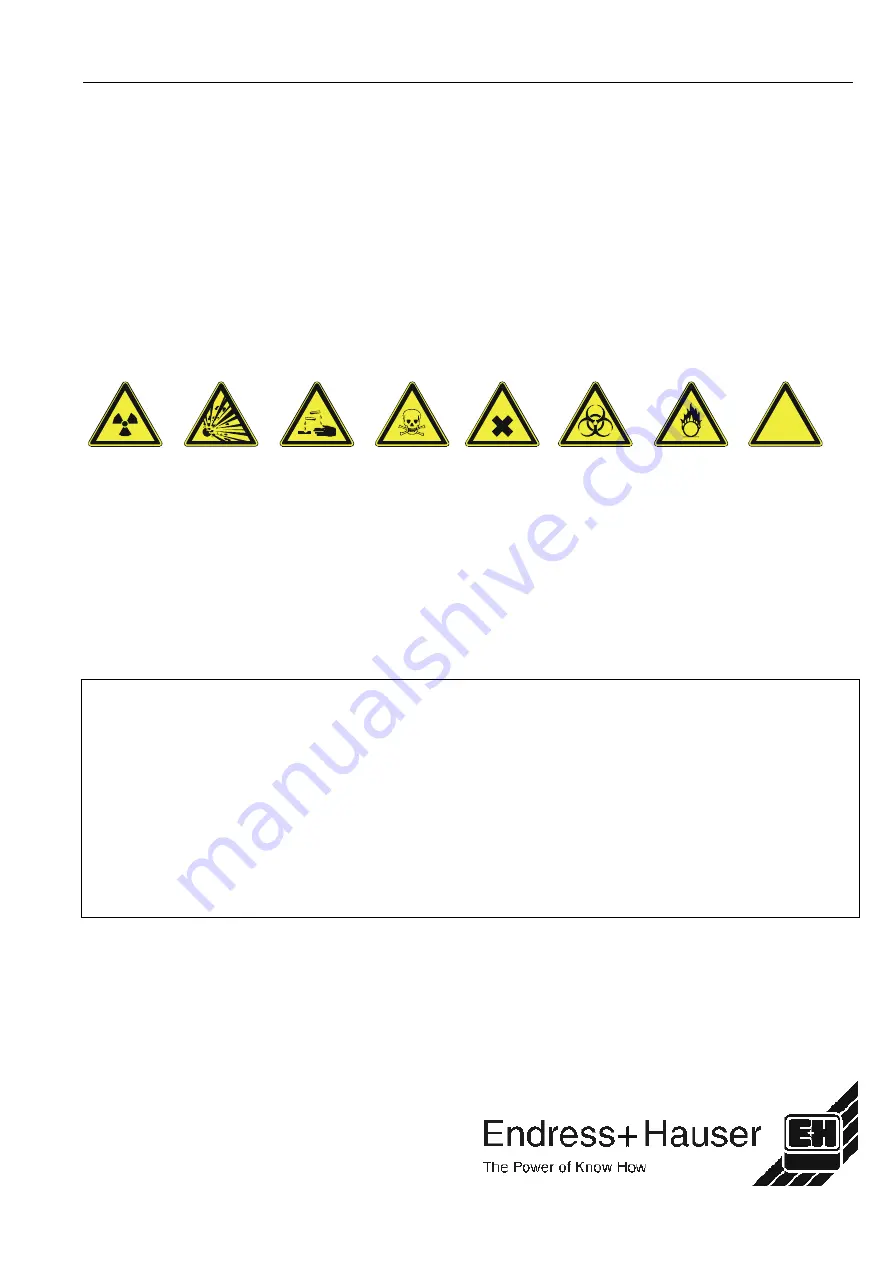
More information about services and repairs:
www.services.endress.com
Declaration of contamination
Dear customer,
Because of legal determinations and for the safety of our employes and operating equipment we need this
“Declaration of contamination” with your signature before your order can be handled. Please put the completely
filled in declaration to the instrument and to the shipping documents in any case. Add also safety sheets and/or
specific handling instructions if necessary.
type of instrument / sensor: __________________________________
serial number: _______________________
medium / concentration:
__________________________________
temperature: ______ pressure: _______
cleaned with:
__________________________________
conductivity: ______ viscosity: _______
Warning hints for medium used:
o
radioactive
o
explosive
o
caustic
o
poisonous
o
harmful of
health
o
biological
hazardous
o
inflammable
o
safe
Please mark the appropriate warning hints.
Reason for return:
___________________________________________________________________________
___________________________________________________________________________
Company data:
company:
______________________________
contact person:
_________________________
______________________________
_________________________
______________________________
department:
_________________________
address:
______________________________
phone number:
_________________________
______________________________
Fax/E-Mail:
_________________________
______________________________
your order no.:
_________________________
I hereby certify that the returned equipment has been cleaned and decontaminated acc. to good industrial prac-
tices and is in compliance with all regulations. This equipment poses no health or safety risks due to contamination.
_______________________________
___________________________________
(Date)
(company stamp and legally binding signature)
SAFE