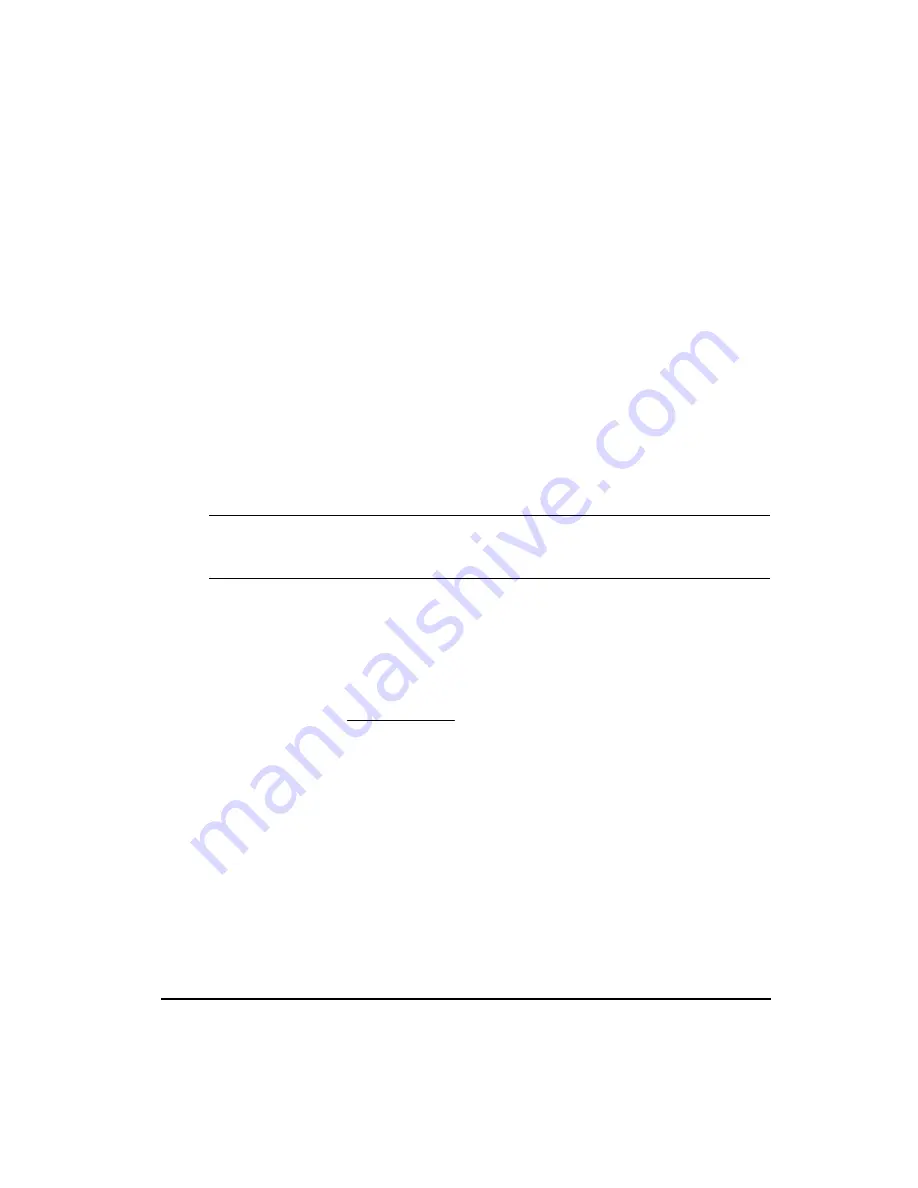
141
Tuning Procedures
• If your application has travel limits, it may be helpful to use an external position controller
to prevent the axis from exceeding the machine limits. Set up a trapezoidal profile as
shown.
• In the procedure below, the Torque Command and Velocity Feedback parameters can be
measured using the drive’s analog outputs, PowerTools software.
• With vertical loads the test readings must be taken while traveling in the same direction.
• An oscilloscope may be needed for systems with limited travel moves to measure the
rapidly changing torque and velocity signals.
• If your system’s friction changes with operating temperature, perform this procedure at
normal operating temperature.
Procedure for Determining Friction:
1. Run the motor at the low test speed (at least 500 RPM).
2. While at speed, note the Torque Command Actual value (T
CL
).
Note
If the friction loading of your system varies when operating at constant speed, due to a
load or spring load that changes as the motor rotates, use the lowest value measured.
3. Repeat Step 1 using a velocity at least two times the low speed.
4. While at speed, note the Torque Command Actual value (T
CH
).
5. Use the following formula to calculate the friction:
Where:
T
CH
= Torque Command Limited value at higher speed
T
CL
= Torque Command Limited at lower speed
RPM
H
= Higher RPM (velocity)
RPM
L
= Lower RPM (velocity)
FV = Friction value
The figure below shows the relationship of Torque Command to the Velocity Feedback.
There is increased torque during the Accel ramp (Ta), constant torque (Tc) during the
constant velocity portion of the ramp and decreased torque (Td) during the decel ramp.
L
H
CL
CH
RPM
-
RPM
)
T
-
(T
FV
)
100
(
=
Artisan Technology Group - Quality Instrumentation ... Guaranteed | (888) 88-SOURCE | www.artisantg.com