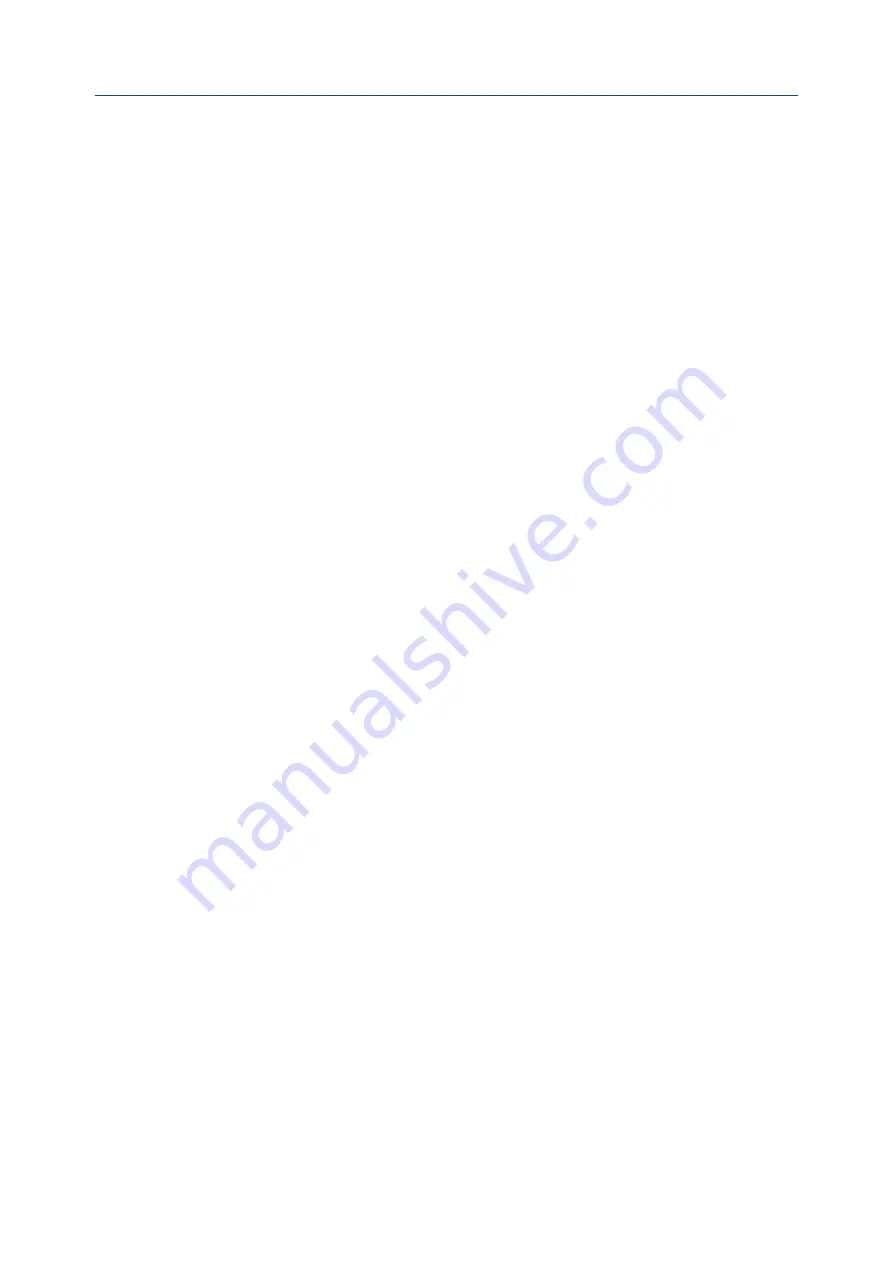
October 2019
Installation, Operation and Maintenance Manual
MAN-02-04-97-0713-EN Rev. 1
56
Section 9: Set-Up Routines
Set-Up Routines
•
Press YES to change ESD priority with reference to the following signals or status:
—
(*) Motor thermostat alarm. By choosing ESD > THERMOSTAT, the
ESD action will be carried out even in the event of motor over-heating.
Conversely, if ESD < THERMOSTAT was chosen, the ESD action will not be
performed in the event of motor over-heating.
—
(*) Torque limit tripped. By choosing ESD > TORQUE LIMIT, the ESD
action will be carried out even if a torque alarm is present. Conversely, if
ESD < TORQUE LIMIT was chosen, the ESD action will not be performed
while a torque alarm is present.
—
(*) Local stop pressed. By choosing ESD > LOCAL STOP, the ESD action
will override the local STOP signal. Conversely, if ESD < LOCAL STOP
was chosen, the ESD action will not be performed if the local STOP
push-button is pressed.
—
Local selector in LOCAL. By choosing ESD > LOCAL CONTROLS, the
ESD action will be carried out also when the local selector is in LOCAL.
Conversely, if ESD < LOCAL CONTROLS was chosen, the ESD action will not
be performed if the 3-position selector is in LOCAL.
—
2-speed timer. By choosing ESD > 2-speed timer, the 2-speed timer function
will be inhibited during the ESD action. Conversely, if ESD < 2-speed timer was
chosen, the 2-speed timer function will remain enabled during ESD action.
—
(*) Local selector in OFF. By choosing ESD > OFF, the ESD action will be
carried out also when the local selector is in OFF. Conversely, if ESD < OFF
was chosen, the ESD action will not be performed if the 3-position selector
is in OFF.
The factory configuration is the following:
action: CLOSE, signal type: PRESENT, priorities: ESD > LOCAL CONTROLS, ESD > 2-SPEED
TIMER, ESD < all other cases.
9.1.4
Remote Controls
The actuator may be remotely controlled by 4, or 3, or 2 wires depending on the
connection made on the terminal board of the actuator.
The following options are available:
•
4 wires latched: requires 2 momentary signals (since the control is self-maintained)
to open or close and one signal to stop in mid-travel. The action of the stop
signal can be reversed (stop when signal is On [MAKE] or stop when signal is Off
[BREAK]).
•
3 wires latched instant reverse: requires 2 momentary signals
(since the control is self-maintained) to open or close. A reverse momentary
signal reverses the direction.
•
3 wires momentary: requires 2 push-to-run type signals (since the control is not
self-maintained) to open or close.
•
2 wires open if signal On: requires signal On to open and no signal to close.
•
2 wires open if signal Off: requires signal Off to open and signal On to close
By selecting the option "Off", the remote controls are disabled.
Configuration should be performed during actuator set-up.