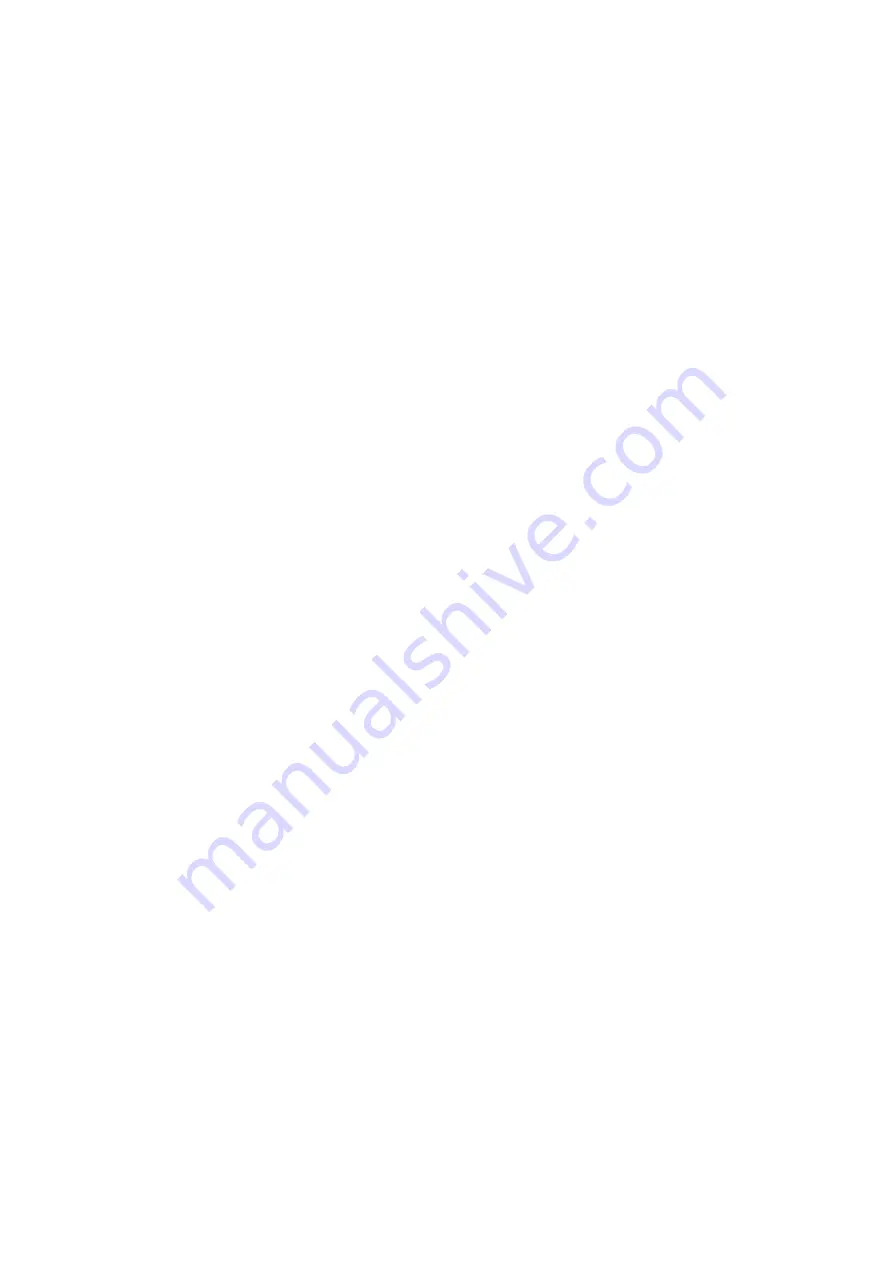
B 3
B_DF1
1
5PD_DF125
PD_01_G
B.
fm
3-
2
4
2.1
Vehicle
Construction
The paver finisher has a welded steel frame on which the individual components are
mounted.
The large drive wheels together with the front tandem shaft jointly compensate the
irregularities of the soil and as a result of the suspension of the screed they guarantee
a particularly high paving precision.
The continuously adjustable hydrostatic traction drive allows the speed of the paver
finisher to be matched to all work conditions.
The operation of the road construction equipment is considerably facilitated by the
automatic mixer device, the independent drives and the transparent operating com-
ponents and controls.
The following extra equipment (option) is available:
o
Automatic levelling/slope control system
o
Ultrasonic sensors for material transport (controller)
o
Additional cut-off shoe
o
Larger working widths
o
Automatic central lubrication system for the paver finisher and/or the screed
o
Protective roof
o
Further equipment and upgrade options on request
Engine: The paver finisher is driven by a water cooled Diesel engine. For further de-
tails see the technical data and the engine's instruction manual.
The particle filter (
o
) cleans the exhaust gas from the soot particles produced, reduc-
es the generation of harmful carbon-monoxyde and carbon-dioxyde gases, therefore,
it operates as a catalyser to minimize the load on the environment and health. A con-
trol light indicates the necessity of maintenance operations.
Running gear: The front axle was designed as a tandem swinging axle. As the
wheels are not mounted on non-uniform lifting axles, the second front wheel is subject
to a heavier load on the shorter lifting arm.
As a result of this solution the steering possibility and the load capacity are improved,
especially on soft ground. Tyres mounted with flexible solid tyres on the front wheels
and large-size, tubeless, air filled tyres on the rear wheels (water filled tyres -
o
).
In case of complementary front wheel drive the second front axle or both front axles
can be engaged as additional drive axles.
Summary of Contents for Svedala Demag DF 115 P/D
Page 2: ...VALUE QUALITY THE ORIGINAL Your Authorized Dynapac Dealer...
Page 10: ......
Page 18: ......
Page 20: ......
Page 44: ......
Page 60: ...D 1 3 4 D_1 3_01_GB fm 4 24 Element2_konv_Rad_634 bmp 9 12 9a 5 8 14 A 6 7 13 10 11...
Page 62: ...D 1 3 6 D_1 3_01_GB fm 6 24 Element2_konv_Rad_634 bmp 9 12 9a 5 8 14 A 6 7 13 10 11...
Page 80: ...D 1 3 24 D_1 3_01_GB fm 24 24...
Page 120: ...D 4 5 24 D_4 5_01_GB fm 24 34 2 2 Error messages...
Page 121: ...D 4 5 25 D_4 5_01_GB fm 25 34...
Page 122: ...D 4 5 26 D_4 5_01_GB fm 26 34...
Page 123: ...D 4 5 27 D_4 5_01_GB fm 27 34...
Page 124: ...D 4 5 28 D_4 5_01_GB fm 28 34...
Page 125: ...D 4 5 29 D_4 5_01_GB fm 29 34 2 3 FMI codes...
Page 142: ...E 01 12 E_01_GB fm 12 18 3 Auger extension auger type II Auger_DEM bmp...
Page 148: ......
Page 150: ......
Page 153: ...F 3 0 1 F_3 0_01_GB fm 1 4 F 3 0 Maintenance Conveyor 1 Maintenance Conveyor...
Page 157: ...F 4 1 1 F_4 1_01_GB fm 1 8 F 4 1 Maintenance Auger 1 Maintenance auger sub unit...
Page 164: ......
Page 176: ......
Page 177: ...F 6 0 1 F_6 0_01_GB fm 1 8 F 6 0 Maintenance Hydraulic system 1 Maintenance hydraulic system...
Page 190: ......
Page 218: ......
Page 219: ...F 10 0 1 F_10 0_01_GB fm 1 6 F 10 0 Checks decommissioning 1 Tests check up cleaning stopping...
Page 224: ......
Page 232: ......