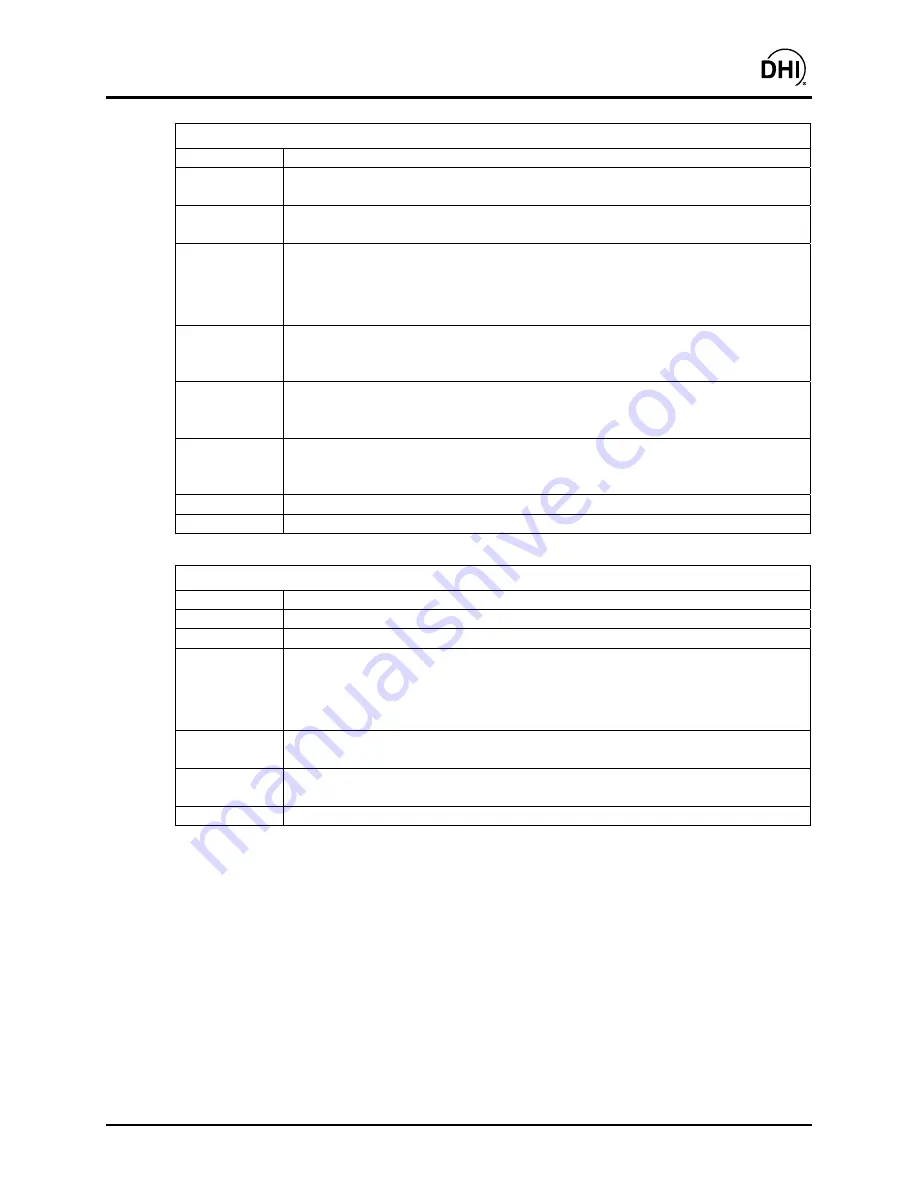
PPCK+™ Operation and Maintenance Manual
Page 95
©2001
DH Instruments, Inc
.
READYCK
Purpose
Read or set the ready check flag.
Command
Query
“READYCK 1”
“READYCK?”
Classic “READYCK=1”
“READYCK”
Remarks
The internal ready check flag is cleared whenever the PPCK+ reaches a
Not Ready
(NR) condition. The "READYCK" query will return the status of this flag. This flag is
set by sending the "READYCK 1" program message while the PPCK+ is in a
Ready
condition. You can then use “READYCK” program message query at a later
time to determine if a
Not Ready
(NR) condition has occurred since.
Example
(enhanced)
Cmd sent:
Query reply:
“READYCK 1”
“1” (if PPCK+ condition has stayed
Ready
)
“0” (if PPCK+ condition has NOT stayed
Ready
)
Example
(classic v2.01
& up)
Sent:
Query reply:
“READYCK=1”
“READYCK=1” (if PPCK+ condition has stayed
Ready
)
“READYCK=0” (if PPCK+ condition has NOT stayed
Ready
)
Example
(classic v2.00)
Sent:
Query reply:
“READYCK=1”
“1” (if PPCK+ condition has stayed
Ready
)
“0” (if PPCK+ condition has NOT stayed
Ready
)
Errors
ERR# 6:
Argument is not a ‘0’ or a ‘1’.
See Also
3.1.2.5, “SR?”
REMOTE
Purpose
Lock out the front panel controls.
Command “REMOTE”
Classic “REMOTE”
Remarks
The PPCK+ goes into remote mode whenever communications take place. The user
can return to local operation by pressing the
[ESC]
key. The REMOTE program
message locks out the front panel completely. The only way to unlock the front panel
is by using the LOCAL program message, the IEEE-488 ‘GTL’ command, or by
cycling the PPCK+ power.
Example
(enhanced)
Cmd sent:
Reply:
“REMOTE”
“REMOTE” (no reply if IEEE-488)
Example
(classic)
Sent:
Reply:
“REMOTE”
“REMOTE”
See Also
“LOCAL”
Summary of Contents for PPCK PLUS
Page 14: ...PPCK Operation and Maintenance Manual 2001 DH Instruments Inc Page 6 N NO OT TE ES S...
Page 24: ...PPCK Operation and Maintenance Manual 2001 DH Instruments Inc Page 16 N NO OT TE ES S...
Page 76: ...PPCK Operation and Maintenance Manual 2001 DH Instruments Inc Page 68 N NO OT TE ES S...
Page 142: ...PPCK Operation and Maintenance Manual 2001 DH Instruments Inc Page 134 N NO OT TE ES S...
Page 150: ...PPCK Operation and Maintenance Manual 2001 DH Instruments Inc Page 142 N NO OT TE ES S...