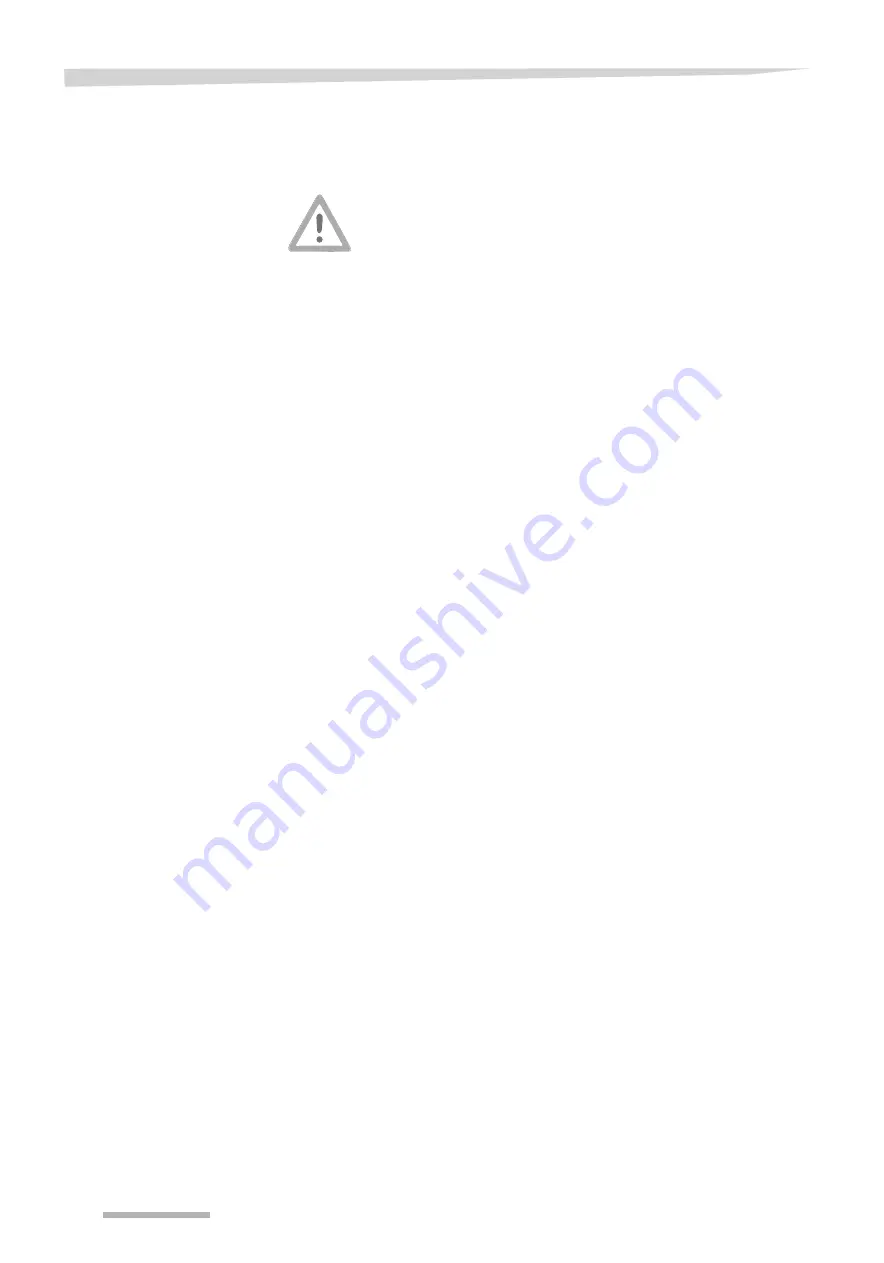
46
Cleaning and care
Cleaning and care
Safety
The following applies to all cleaning and care work:
Observe safety instructions
Do not fail to observe the safety instructions when performing all work
operations. Any disregard for safety instructions can lead to severe or
fatal injuries to persons.
Securing the implement
•
Before starting the cleaning work, always switch off the p.t.o. and
lock it out against accidental operation!
•
Secure the implement against rolling away by using wheel wedges
•
The implement must be standing on a flat, firm surface and may
have to be supported during the work
Unsecured or non-supported implements can cause accidents.
Do not clean bearings or hydraulic parts with high pressure cle-
aners
Do not clean bearings or hydraulic parts with high pressure cleaners.
This will degrease the bright parts and they will start to rust. After each
cleaning process lubricate the bearing points and grease the bright
parts.
Cleaning
After each deployment clean the implement of any coarse dirt and
crops.
Cleaning is performed with a high-pressure cleaner, with the excepti-
on of the bearings and piston rods of the hydraulic cylinders.
After cleaning:
After cleaning with the high-pressure cleaner lubricate all bearing
points.
Care
In order that the wheel rake has a long service life we recommend:
> applying a protective layer of oil to all bright work tools. Use only
permitted biologically degradable oil, for example, rapeseed oil
> Repair any paint damage
All manuals and user guides at all-guides.com