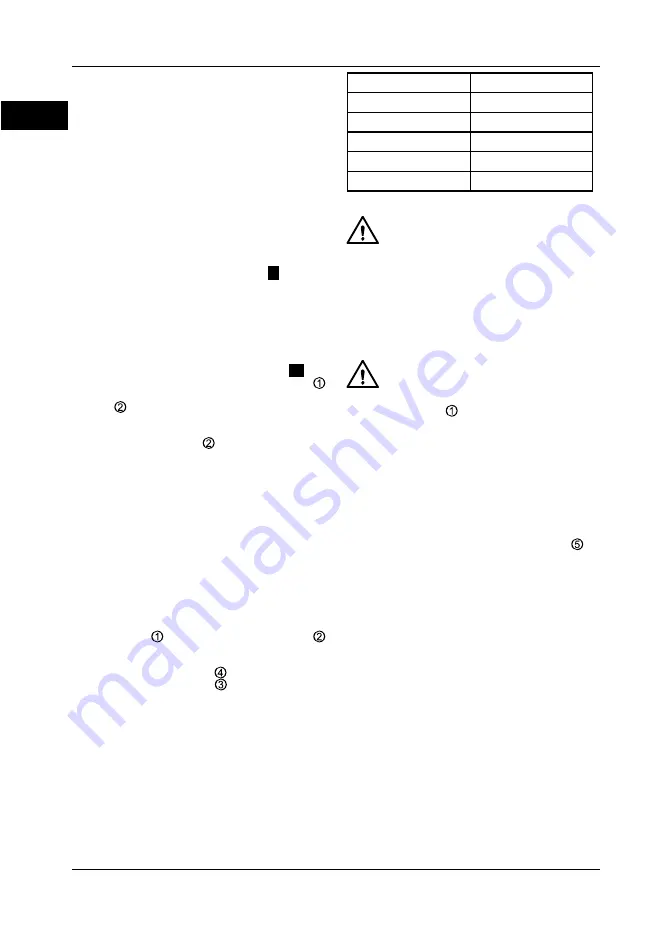
8
GB
H Insulation
class
X
Duty Cycle (measured in % from
standard 5 min cycle). For in-stance,
10% means that each 30 seconds use
shall be followed by 4 min 30 sec break.
Stick to this to prolong the service life of
your welding machine.
The set is interference-suppressed in compliance with
EC Directive 89/336/EEC
5. CABLE CONNECTION
TO THE MAINS SOCKET
Among three-core cables, two shall be the input power
cables and one double-color (yellow-green) shall be
the earthing wire with PE bushing. See
fi
g.
2
for guide-
lines.
Using surge protector is recommended to protect the
machine from the
fl
uctuation of voltage.
6. WELDING PREPARATIONS
Important! Always make sure the device is unplugged
before connecting or disconnecting the welding cable!
Connect the welding cables as shown in (
fi
g.
3
). To
do so, connect the cable with the electrode holder
to the positive pole quick-lock coupling and the ground
terminal
to the negative pole quick-lock coupling.
Lock the connectors in place by turning them in a
clockwise direction.
Connect the earth terminal
direct to the part to be
welded or to the support on which the part is resting.
Ensure that the earth terminal is in direct contact with
the part to be welded. You should therefore avoid coat-
ed surfaces and/or insulated materials. The electrode
holder cable has a special clamp at one end, which is
used to secure the electrode. The welding safety shield
must be used at all times for welding. It protects your
eyes from the radiation emitted by the arc and never-
theless enables you to watch the welding process.
7. WELDING
After you have made all the electrical connections for
the power supply and for the welding circuit, you can
proceed as follows:
Insert the unsheathed end of the electrode into the
electrode holder
and connect the earth terminal
to the part you wish to weld.
Ensure that a good electric contact is made. Switch on
the welding set at the switch
and set the welding
current using the hand wheel
to suit the electrode
you wish to use. Hold the safety shield in front of your
face and rub the tip of the electrode on the part you
wish to weld as if you were striking a match. This is
the best method of igniting the arc. Check that you
have the correct electrode and current strength on a
test part.
Electrode (Ø mm)
Welding current (A)
2
40-80
2,5
60-110
3,2
80-160
4
120-200
5
150-200
Important!
Do not dab the workpiece with the electrode
since it could be damaged, making it more
dif
fi
cult to ignite the arc.
As soon as the arc has ignited, attempt to keep it a
distance from the workpiece equivalent to the diameter
of the electrode.
This distance should be kept as constant as possible
during the welding process. The angle of the electrode
in the direction in which you are working should be
20/30°.
Important!
Always use tongs to remove spent electrodes
and to
move parts that you have just welded. Please note that
the electrode holder must always be put down so
that it is insulated after you have completed the weld-
ing work.
Do not remove the slag until the weld has cooled. If you
want to continue a weld after an interruption, the slag
from your initial attempt must
fi
rst be removed.
Switch off and unplug the machine after operation.
8. OVERHEATING GUARD
The welding set is
fi
tted with an overheating guard that
protects the welding transformer from overheating. If
the overheating guard trips, the control lamp on
your set will be lit. Allow the welding set to cool for a
time.
9. MAINTENANCE
Switch off and unplug the machine before carrying out
any maintenance works on it. Remove dust and dirt
from the machine at regular intervals. Cleaning is best
carried out with a
fi
ne brush or a cloth.
Summary of Contents for 98291445
Page 1: ......
Page 45: ...45 RU 42 10 C 40 C 1000 1 2 3 4 5 6 7 RU...
Page 46: ...46 RU 9 10 DIN 50 Hz U1 I1 max U0 I2 mm nc nc1 nc nc1 nh nh1 nh nh1 IP 21 H X 5 10 30 4 30...
Page 47: ...47 RU 2 40 80 2 5 60 110 3 2 80 160 4 120 200 5 150 200 20 30...
Page 48: ...48 KZ 42 1000 10 40 1 2 3 4 5 6 7 DIN 9 10 KZ...
Page 49: ...49 KZ 50 Hz U1 I1 max U0 I2 mm nc nc1 nc nc1 nh nh1 nh nh1 IP 21 H X 5 10 30 4 30...
Page 50: ...50 KZ 220 230 2 40 80 2 5 60 110 3 2 80 160 4 120 200 5 150 200 20 30...
Page 51: ...51 UA I i 42 10 C 40 C 1000 1 2 3 4 5 6 7 9 10 D N UA...
Page 52: ...52 UA 50 Hz U1 I1 max U0 I2 mm nc nc1 nc nc1 nh nh1 nh nh1 IP 21 H X 5 10 30 4 30...
Page 53: ...53 UA 2 40 80 2 5 60 110 3 2 80 160 4 120 200 5 150 200 20 30 i i...
Page 75: ...75 GR 42 V 1 2 3 4 5 6 7 9 10 DIN...
Page 76: ...76 GR 50 Hz U1 I1 max U0 I2 mm nc nc1 nc nc1 nh nh1 nh nh1 IP 21 H X 89 334 X 220 230 V o...
Page 77: ...77 GR mm A 2 40 80 2 5 60 110 3 2 80 160 4 120 200 5 150 200 20 300...
Page 81: ...81 AE 1 2 3 4 5 6 7 AE...
Page 82: ...82 Exploded view DWI 200S...
Page 88: ...R R L L...