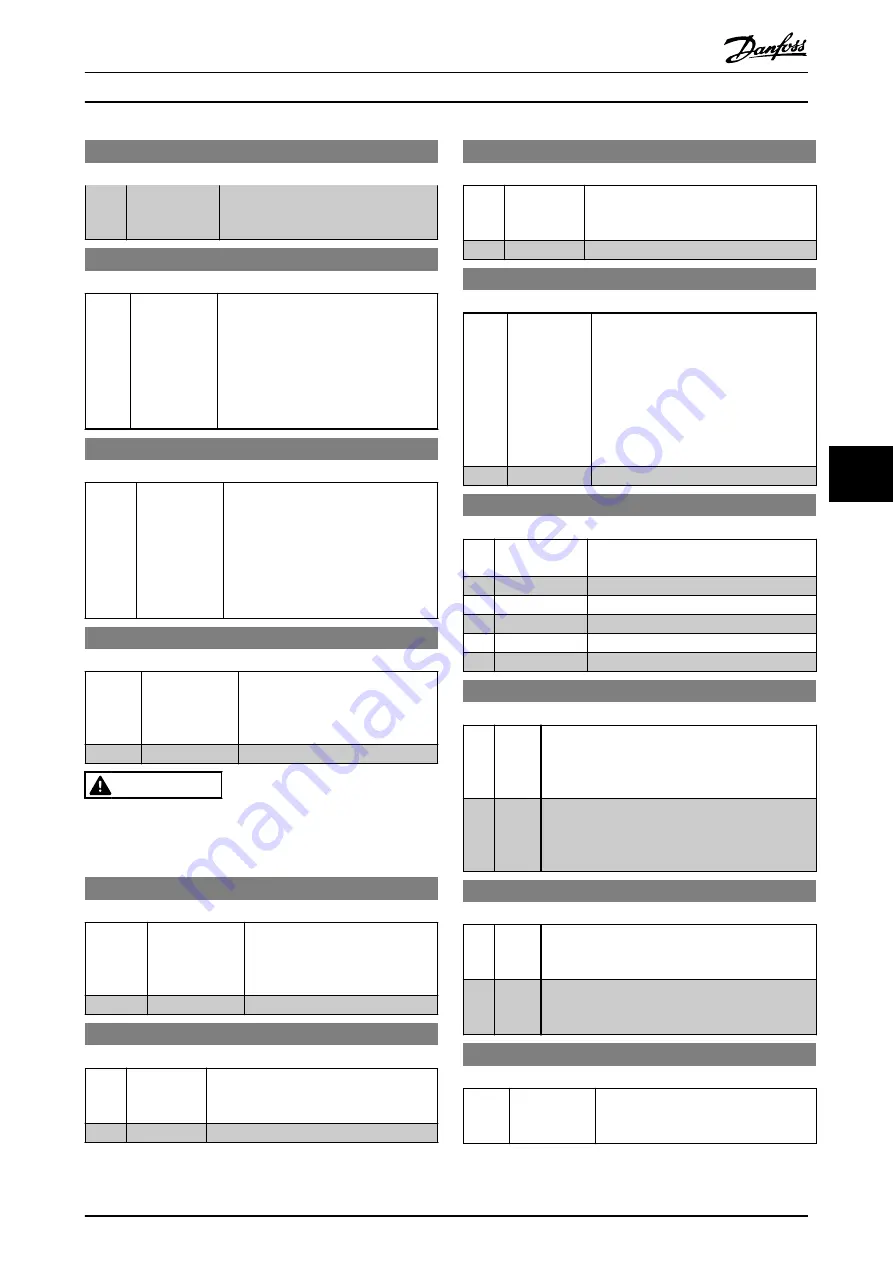
3-10 Preset Reference
Option:
Function:
3-02 Minimum Reference
is set to -70
and
3-03 Maximum Reference
is set to
50. In this case 0%=0 and 100%=70.
4-12 Motor Speed Low Limit
Range:
Function:
0.0 Hz
*
[0.0-400.0 Hz] Set the
Minimum Motor Speed Limit
corresponding to the minimum output
frequency of the motor shaft.
NOTE
As the minimum output frequency
is an absolute value, it cannot be
deviated from.
4-14 Motor Speed High Limit
Range:
Function:
65.0 Hz
*
[0.0-400.0 Hz] Set the
Maximum Motor Speed
corresponding to the maximum output
frequency of the motor shaft.
NOTE
As the maximum output frequency
is an absolute value, it cannot be
deviated from.
6-22 Terminal 60 Low Current
Range:
Function:
This reference signal should
correspond to minimum reference
value set in
6-24 Terminal 60 Low
Ref./Feedb. Value
.
0.14 mA
*
[0.00-19.90 mA] Enter low current value.
CAUTION
The value must be set to min. 2 mA in order to activate
the Live Zero Timeout function in
6-01 Live Zero Timeout
Time
.
6-23 Terminal 60 High Current
Range:
Function:
This reference signal should
correspond to the high current
value set in
6-25 Terminal 60 High
Ref./Feedb. Value
.
20.00 mA
*
[0.10-20.00 mA] Enter high current value.
6-24 Terminal 60 Low Ref./Feedb. Value
Range:
Function:
The scaling value corresponding to the
low current set in
6-22 Terminal 60 Low
Current
.
0.000
*
[-4999-4999] Enter analog input scaling value.
6-25 Terminal 60 High Ref./Feedb. Value
Range:
Function:
The scaling value corresponding to the
high current set in
6-23 Terminal 60 High
Current
.
50.00
*
[-4999-4999] Enter analog input scaling value.
6-26 Terminal 60 Filter Time Constant
Range:
Function:
A first-order digital low pass filter time
constant for suppressing electrical noise
in terminal 60. A high time constant
value improves dampening, but also
increases time delay through the filter.
NOTE
This parameter cannot be changed
while motor runs.
0.01 s
*
[0.01-10.00 s] Enter time constant.
7-20 Process CL Feedback Resources
Option:
Function:
Select input to function as feedback
signal.
[0]
*
No Function
[1]
Analog Input 53
[2]
Analog Input 60
[8]
Pulse Input 33
[11] Local Bus Ref.
7-30 Process PI Normal/Inverse Control
Option:
Function:
[0]
*
Normal Feedback larger than setpoint result in a speed
reduction.
Feedback less than setpoint result in a speed
increase.
[1]
Inverse Feedback larger than setpoint result in a speed
increase.
Feedback less than setpoint result in a speed
reduction.
7-31 Process PI Anti Windup
Option:
Function:
[0]
Disable Regulation of a given error will continue even
when the output frequency cannot be increased/
decreased.
[1]
*
Enable PI-controller ceases from regulating a given error
when the output frequency cannot be increased/
decreased.
7-32 Process PI Start Speed
Range:
Function:
0.0 Hz
*
[0.0-200.0 Hz] Until the set motor speed has been
reached the frequency converter
operates in Open Loop mode.
Programming
VLT
®
Micro Drive FC 51 Design Guide
MG02K202 - VLT
®
is a registered Danfoss trademark
67
7
7
Buy: www.ValinOnline.com | Phone 844-385-3099 | Email: [email protected]