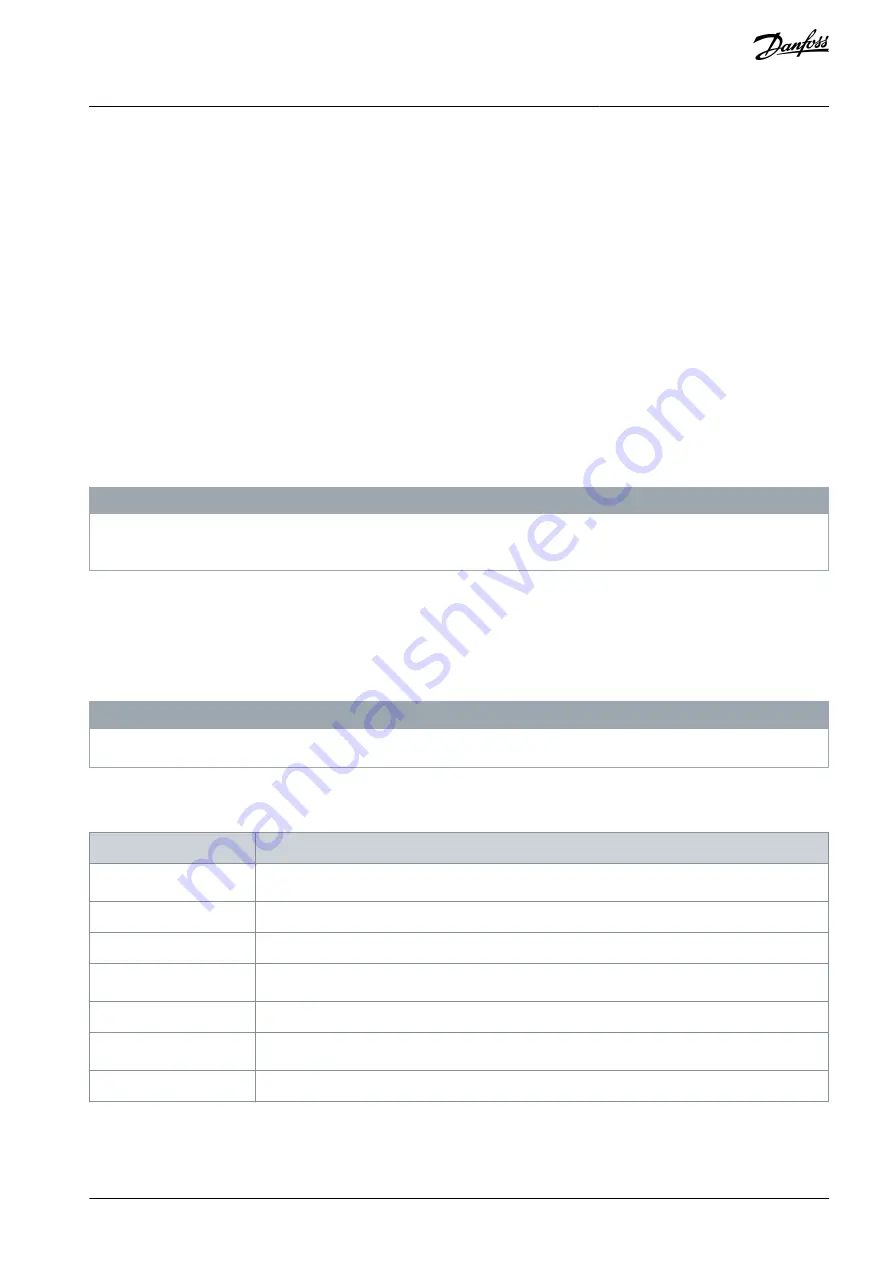
•
•
•
•
•
•
•
•
•
-
-
6.5.14 Programming Guidelines for Automation Studio™
Recommendations for implementation:
Initialize parameters that usually do not change only once at the beginning of the program. In Automation Studio
™
, use the
_INIT
section.
Call up function blocks that provide status or error information with
Enable
input at the beginning of the program.
Use 1 instance of the function block
MC_Power_DDS
for every axis to control its power stage. Call up this function block in every
PLC cycle.
Use 1 instance of the function block
DD_Power_PSM
for every PSM 510 to control the DC-link voltage on the output. Call up this
function block in every PLC cycle.
Use 1 instance of the function block
DD_Power_DAM
for every DAM 510 to control the DC-link voltage on the output. Call up
this function block in every PLC cycle.
Use 1 instance of the function block
DD_Power_ACM
for every ACM 510 to control the connection between the DC-link and the
ACM 510. Call up this function block in every PLC cycle.
Call up function blocks that execute (motion) commands at the end of the program.
Do not use any POUs from the library (folder)
DDS_Intern
.
Do not change the reference to the axis on a function block while it is busy.
N O T I C E
The full parameter list can be found in the
VLT® Servo Drive System ISD 510, DSD 510, MSD 510 (VLT® Flexmotion
™
) Pro-
gramming Guide
.
6.6 VLT® Servo Toolbox Software
6.6.1 Overview
The VLT
®
Servo Toolbox is a standalone PC software designed by Danfoss. It is used for parameterization and diagnostics of the
system modules. It is also possible to operate the devices in a non-productive environment.
N O T I C E
The VLT® Servo Toolbox software must be allowed for every firewall profile (private/public/domain).
The VLT
®
Servo Toolbox contains several subtools that provide various functionalities.
Table 16: Important Subtools
Subtool
Description
Scope
For visualization of the tracing functionality of the ISD 511, PSM 510, DAM 510, and ACM 510.
Parameter list
For reading/writing parameters.
Firmware update
For updating the firmware on the devices.
Drive control
For operating the servo drives for testing purposes.
PSM control
For operating the Power Supply Module (PSM 510) for testing purposes.
DAM control
For operating the Decentral Access Module (DAM 510) for testing purposes.
ACM control
For operating the Auxiliary Capacitors Module (ACM 510) for testing purposes.
AQ377148425069en-000101
/ 130R1213 | 77
Danfoss A/S © 2023.08
Commissioning
VLT® Servo Drive System ISD 511
Operating Guide