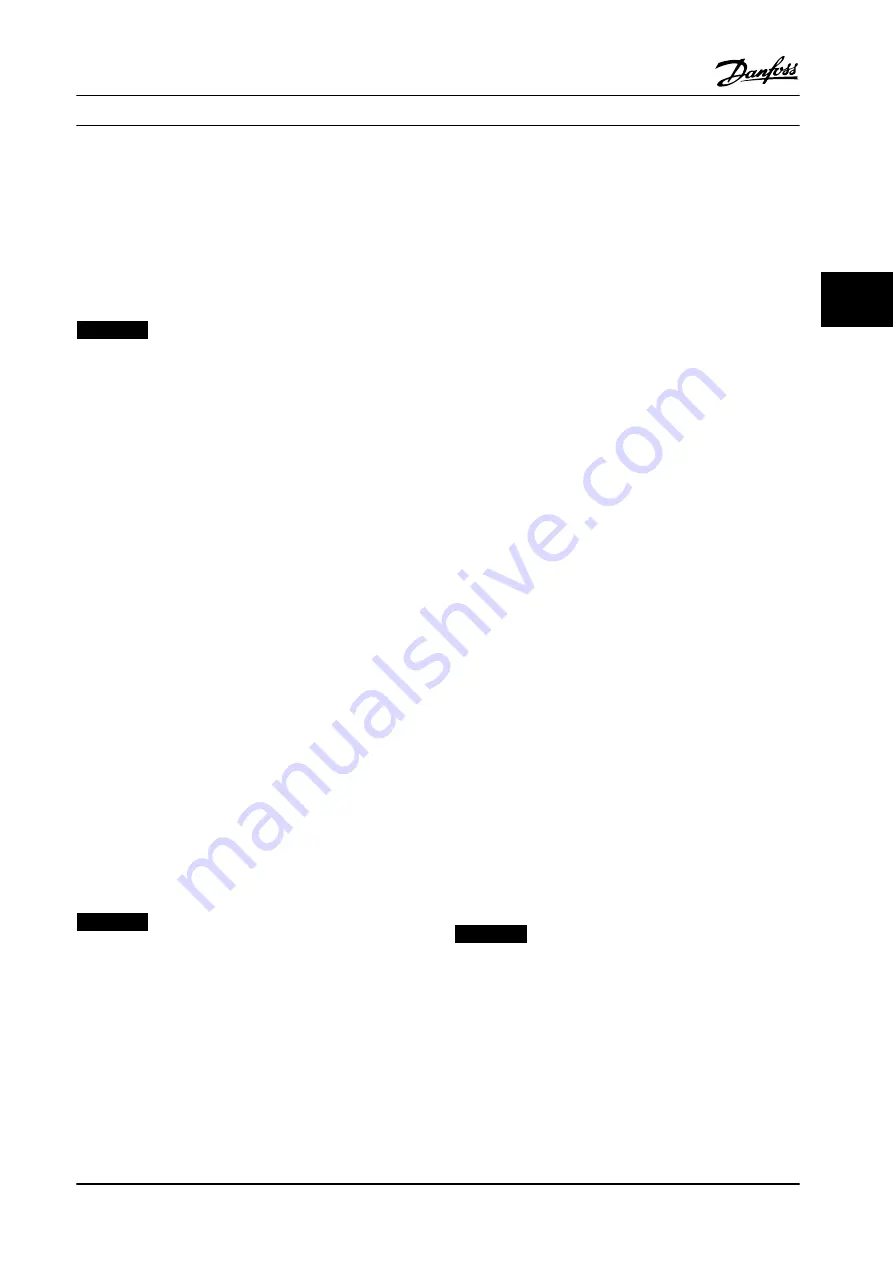
Ensure that the parameters previously mentioned are
programmed correctly and that any digital input
programmed for
Stop Inverse
is high (logic “1”).
Display indication that the unit is functioning, but no
output
If the unit is equipped with an external 24 V DC option,
check that line power is applied to the adjustable
frequency drive.
NOTICE!
Note: In this case, the LCP display shows
[8] DC undervolt
4.5.4 Incorrect Motor Operation
Occasionally, there is a fault where the motor continues to
run but not in the correct manner. There can be a number
of different causes for this type of fault. The following is a
list of possible problems and recommended procedures for
determining their causes.
Wrong speed/unit does not respond to command
Possible incorrect reference (speed command).
Ensure that the unit is programmed correctly according to
the reference signal being used, and that all reference
limits are set correctly as well. Perform
to check for faulty reference signals.
Motor speed unstable
Possible incorrect parameter settings, faulty current
feedback circuit, loss of motor (output) phase.
Check the settings of all motor parameters, including all
motor compensation settings (slip compensation, load
compensation, and so on). For closed-loop operation,
check PID settings. Perform the
to check for faulty reference signals.
Perform the
chapter 6.4.9 Output Imbalance of Motor
to check for loss of motor phase.
Motor runs rough
Possible over-magnetization (incorrect motor settings), or
an IGBT misfiring.
NOTICE!
Other symptoms include motor stalling when loaded or
the adjustable frequency drive tripping on Alarm 13.
Check setting of all motor parameters. Perform the
chapter 6.4.9 Output Imbalance of Motor Voltage and
Current
.
If output voltage is unbalanced, perform the
chapter 6.4.11 IGBT Gate Drive Signals Test
Motor draws high current but cannot start
Possible open winding in the motor or open phase in
connection to the motor.
Perform the
chapter 6.4.9 Output Imbalance of Motor
to ensure that the adjustable
frequency drive is providing correct output (See Motor
runs rough).
Run an AMA to check the motor for open windings and
unbalanced resistance. Inspect all motor wiring
connections.
Motor will not brake.
Possible fault in the brake circuit. Possible incorrect setting
in the brake parameters. The ramp-down time is too short.
Note: An alarm or warning message may occur.
Check all brake parameters and ramp-down time
(parameter group
2–0*
and
3–4*
).
Perform
.
4.6 Warning/Alarm Messages
4.6.1 Warning/Alarm Code List
A code on the display or the LEDs on the front of the
adjustable frequency drive signal a warning/alarm.
A
warning
indicates a condition that requires attention or
a potentially alarming trend. A warning remains active
until the cause is no longer present. Under some circum-
stances, motor operation may continue.
A trip is the action when an alarm has appeared. The trip
removes power to the motor. Reset it after the condition
has been cleared by pressing [Reset] or through a digital
input (parameter group 5–1*). The event that caused an
alarm cannot damage the adjustable frequency drive or
cause a dangerous condition. Alarms must be reset to
restart operation once their cause has been rectified.
There are three ways to reset:
1.
Pressing [Reset].
2.
A digital reset input.
3.
Serial communication/optional serial communi-
cation bus reset signal.
NOTICE!
After a manual reset pressing [Reset], [Auto On] must be
pressed to restart the motor.
A
trip lock
is an action when a potentially damaging alarm
occurs. Power is removed from the motor. A trip lock can
only be reset after the condition is cleared by cycling
power. Once the problem has been rectified, only the
alarm continues flashing until the adjustable frequency
drive is reset.
Troubleshooting
Service Manual
MG94A222
Danfoss A/S © Rev. 2014-02-10 All rights reserved.
49
4
4
Summary of Contents for VLT FC 103
Page 2: ......