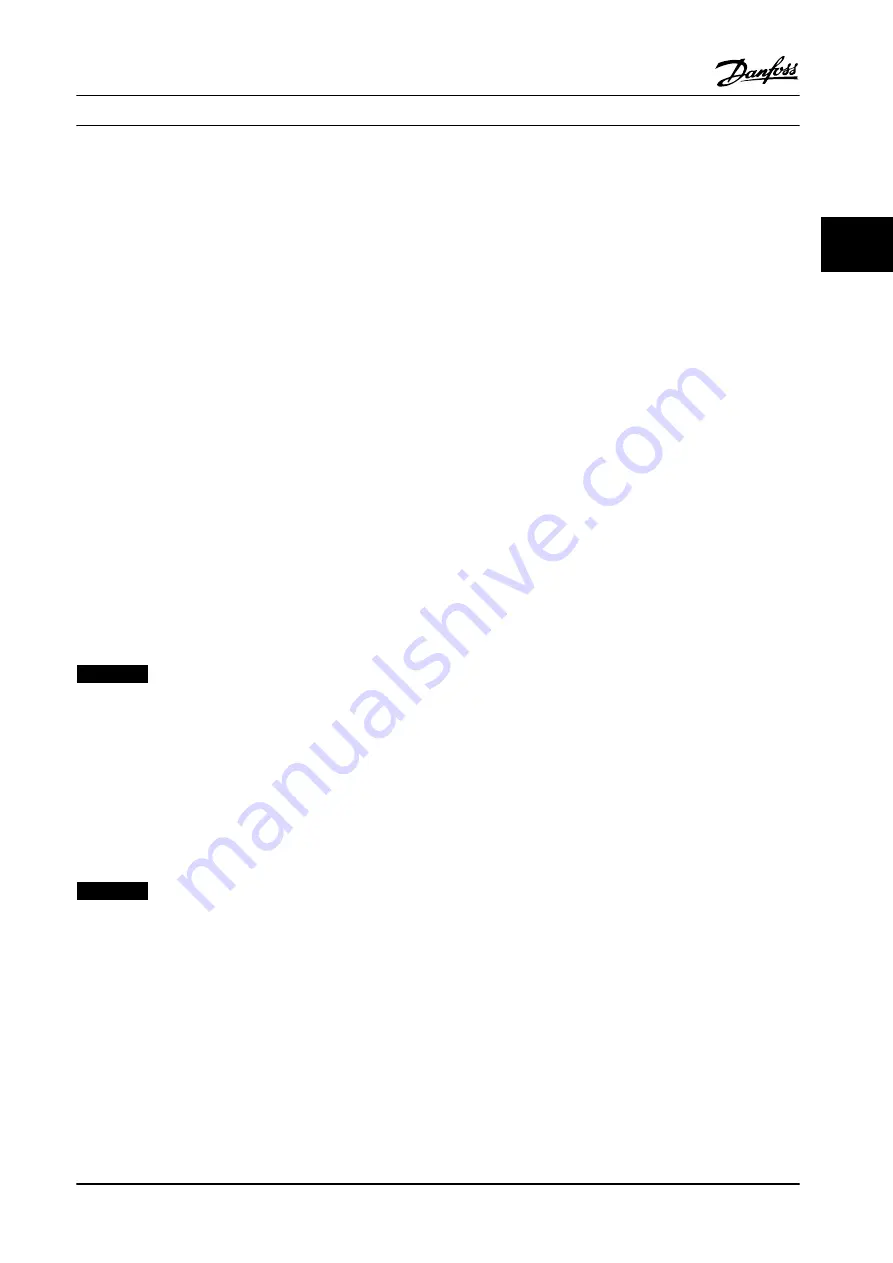
Motor-Generated Overvoltage
The voltage in the intermediate circuit is increased when
the motor acts as a generator. This occurs in the following
cases:
•
When the load generates energy, the load drives
the motor at a constant output frequency from
the adjustable frequency drive.
•
During deceleration ("ramp-down") when the
moment of inertia is high, the friction is low, and
the ramp-down time is too short for the energy
to be dissipated as a loss in the adjustable
frequency drive or motor.
•
Incorrect slip compensation setting may cause
higher DC link voltage.
•
Back-EMF from PM motor operation. If coasted at
high RPM, the PM motor back-EMF may
potentially exceed the maximum voltage
tolerance of the adjustable frequency drive and
cause damage. To help prevent this, the value of
4-19 Max Output Frequency
is automatically
limited based on an internal calculation based on
the value of
1-40 Back EMF at 1000 RPM
,
1-25 Motor Nominal Speed
and
1-39 Motor Poles
.
If it is possible that the motor may overspeed,
Danfoss recommends a brake resistor be
equipped to the adjustable frequency drive.
NOTICE!
The adjustable frequency drive must be equipped with a
brake chopper.
The control unit may attempt to correct the ramp if
possible (
2-17 Over-voltage Control
). The inverter turns off
to protect the transistors and the intermediate circuit
capacitors when a certain voltage level is reached. See
2-10 Brake Function
and
2-17 Over-voltage Control
to select
the method used for controlling the intermediate circuit
voltage level.
NOTICE!
OVC cannot be activated when running a PM motor
(when
1-10 Motor Construction
is set to
[1] PM non-salient
SPM
).
Line drop-out
During a line drop-out, the adjustable frequency drive
keeps running until the intermediate circuit voltage drops
below the minimum stop level. Minimum stop level
typically is 15% below the adjustable frequency drive's
lowest rated supply voltage. The AC line voltage before
the drop-out and the motor load determine how long it
takes for the inverter to coast.
Static overload in VVC
plus
mode
An overload occurs when the torque limit in
4-16 Torque
Limit Motor Mode
/
4-17 Torque Limit Generator Mode
is
reached.
When the adjustable frequency drive is overloaded, the
controls reduce the output frequency to reduce the load. If
the overload is excessive, a current may occur that makes
the adjustable frequency drive cut out after approximately
5–10 s. Operation within the torque limit is limited in time
(0–60 s) in
14-25 Trip Delay at Torque Limit
.
3.11.1 Motor Thermal Protection
To protect the application from serious damages, VLT
®
AutomationDrive offers several dedicated features.
Torque limit
The motor is protected from being overloaded
independent of the speed. Torque limit is controlled in
4-16 Torque Limit Motor Mode
and
4-17 Torque Limit
Generator Mode
. The time before the torque limit warning
trips is controlled in
14-25 Trip Delay at Torque Limit
.
Current limit
The current limit is controlled in
4-18 Current Limit
, and the
time before the current limit warning trips is controlled in
14-24 Trip Delay at Current Limit
Minimum speed limit
4-11 Motor Speed Low Limit [RPM]
or
4-12 Motor Speed Low
Limit [Hz]
limit the operating speed range to between 30
and 50/60 Hz.
4-13 Motor Speed High Limit [RPM]
or
4-19 Max Output Frequency
limit the max output speed the
adjustable frequency drive can provide.
ETR (Electronic Thermal Relay)
The adjustable frequency drive ETR function measures
actual current, speed, and time to calculate motor
temperature and protect the motor from being overheated
(warning or trip). An external thermistor input is also
available. ETR is an electronic feature that simulates a
bimetal relay based on internal measurements.
provides the following example, where the X-axis shows
the ratio between I
motor
and I
motor
nominal. The Y- axis
shows the time in seconds before the ETR cut of and trips
the adjustable frequency drive. The curves show the
characteristic nominal speed, at twice the nominal speed
and at 0.2 x the nominal speed.
Product Introduction
Design Guide
MG34S222
Danfoss A/S © Rev. 2014-02-10 All rights reserved.
61
3
3
Summary of Contents for VLT AutomationDrive FC 300
Page 2: ......