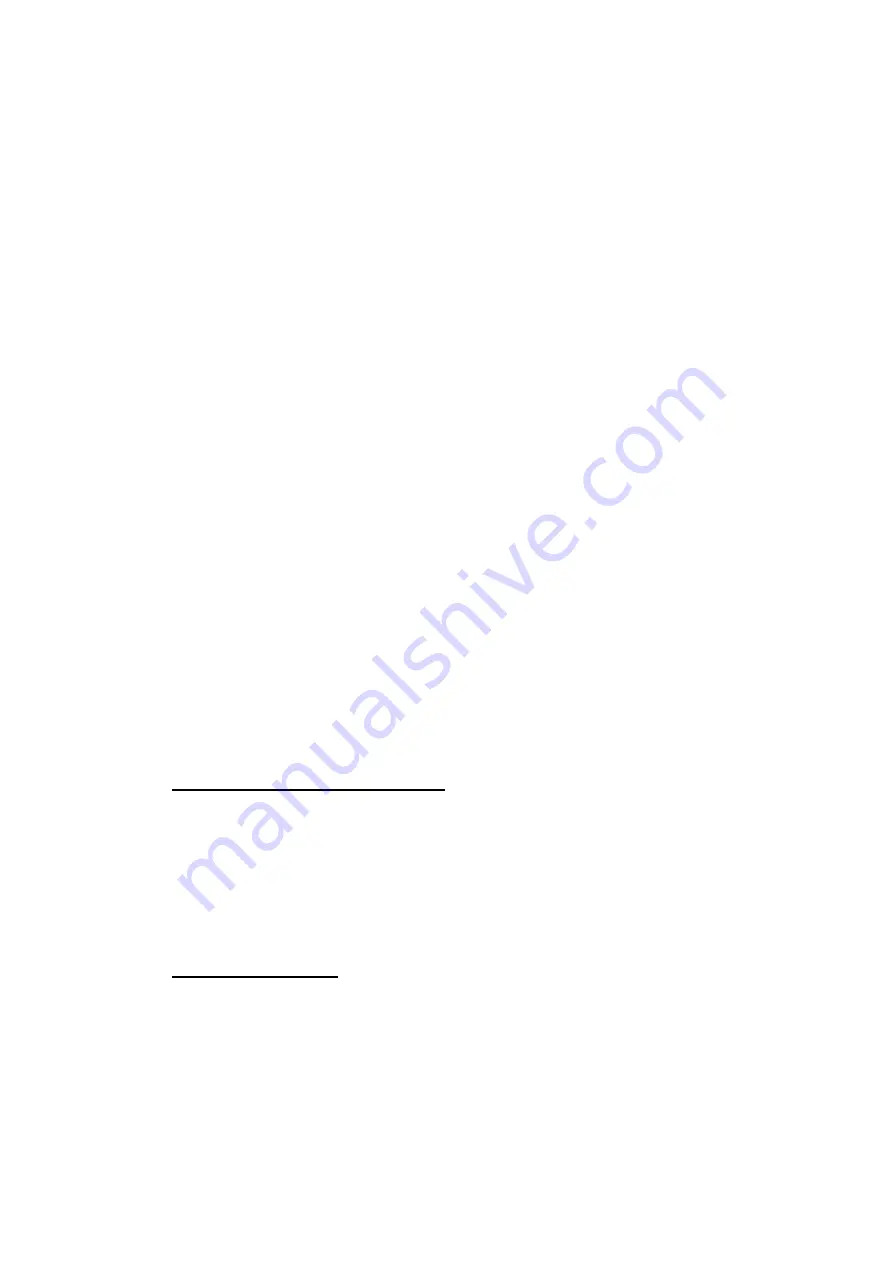
The load on the hammer is the actual weight of the rotary head and drill rods
plus the additional hydraulic pressure which is being applied. For drilling at
shallow depths, the requisite load is obtained by applying the necessary
hydraulic pressure, which is set by adjusting the Variable Feed Control -
No.28.
As the depth increases, so the required hydraulic loading can be reduced.
Eventually a position is reached where the combined head and rod weight
exceed the required bit loading. At this point the Variable Feed Control -
No.28 should be turned towards "DECREASE" fully open, the Holdback
Pressure Control - No.30 is also turned towards "DECREASE" fully closed
and the Hoist/Feed Control Lever - No.14 moved to the "UP" position. With
the drill string suspended on the rotary head and hanging just off hole
bottom, the combined head and drill weight will register on Pressure Gauge.
Gravity feed drilling can then continue by slowly turning the Holdback
Pressure Control - No.30 towards "INCREASE" thereby bleeding oil from the
hoist/feed cylinder and transferring the precise requirement of rod weight to
the bit.
The loads equivalent to the pressure indicated on the gauges are given on
the legend plate attached to the control console.
One of the major problems that occurs when carrying out air hammer drilling
is that the cuttings can stick to the sides of the borehole. This prevents the
hammer from being freely withdrawn. This often occurs when there is a
small amount of water sufficient to dampen the cuttings. One method of
overcoming this problem is to fit a retract substitute immediately on top of the
hammer. The over the top rotary head allows the drill rods and hammer to
be continuously rotated, as the rods are withdrawn from the borehole which
enables the retract cutter blades to clear any obstructions.
4.3
CONTINUOUS FLIGHT AUGERS
When operating continuous flight augers, it is important that the auger should
act as a cutting tool and not be allowed to screw itself in to the ground. The
required control can be achieved by using the Holdback Pressure Control -
No.30 under gravity feed, or the Variable Feed Control
– No 28. The actual
system of controlled feed would be entirely dependent on the strata being
drilled.
4.4
ROTARY DRILLING
The major requirement to enable tricone roller bits to drill efficiently is the
application of requisite loading whilst operating within the recommended
speed range. As a general rule, it is essential to make full use of the
hydraulic pull-down system, which is controlled by the Variable Feed Control
- No.28. Turn the control towards "INCREASE" to increase bit loading and
towards "DECREASE" to reduce bit loading. The maximum hydraulic
pressure which can be applied is 2250 psi. This will induce a load pressure
on the drill string of 5 tons. The actual bit loading will be the applied hydraulic
pressure plus the weight of the drill string and rotary head.
Summary of Contents for TERRIER Mk 1
Page 2: ......
Page 3: ...SECTION 1 GENERAL...
Page 4: ......
Page 24: ...FIGURE 1 1 SAFETY WEDGE LOCATION...
Page 28: ......
Page 29: ...SECTION 2 TECHNICAL DATA...
Page 30: ......
Page 33: ...SECTION 3 OPERATING INSTRUCTIONS...
Page 34: ......
Page 37: ...FIGURE 3 2 VALVE CONTROLS A B C...
Page 44: ......
Page 45: ...SECTION 4 GUIDANCE FOR DRILLING APPLICATIONS...
Page 46: ......
Page 52: ......
Page 53: ...SECTION 5 RIG MAINTENANCE AND SERVICE...
Page 54: ......
Page 70: ......
Page 71: ...SECTION 6 SPARE PARTS ILLUSTRATIONS AND LISTINGS...
Page 72: ...23...
Page 74: ...25...
Page 76: ...27...
Page 78: ...29...
Page 80: ...31...
Page 82: ...33...
Page 84: ...35...
Page 86: ...37...
Page 88: ...39...
Page 90: ......
Page 91: ...SPARE PARTS ILLUSTRATIONS AND LISTINGS FOR UNDER CARRIAGE ENGINE...
Page 92: ......
Page 93: ......
Page 94: ......
Page 95: ......
Page 96: ......
Page 97: ......
Page 98: ......
Page 99: ......
Page 100: ......
Page 101: ......
Page 102: ......
Page 103: ......
Page 104: ......
Page 105: ......
Page 106: ......
Page 107: ......
Page 108: ......
Page 109: ......
Page 110: ......
Page 111: ......
Page 112: ......
Page 113: ......
Page 114: ......
Page 115: ......
Page 116: ......
Page 117: ......
Page 118: ......
Page 119: ......
Page 120: ......
Page 121: ......
Page 122: ......
Page 123: ......
Page 124: ......
Page 125: ......
Page 126: ......
Page 127: ......
Page 128: ......
Page 129: ......
Page 130: ......
Page 131: ......
Page 132: ......
Page 133: ......
Page 134: ......
Page 135: ......
Page 136: ......
Page 137: ......
Page 138: ......
Page 139: ......
Page 140: ......
Page 141: ......
Page 142: ......
Page 143: ......
Page 144: ......
Page 145: ......
Page 146: ......
Page 147: ......
Page 148: ......
Page 149: ......
Page 150: ......
Page 151: ......
Page 152: ......
Page 153: ......
Page 154: ......
Page 155: ......
Page 156: ......
Page 157: ......
Page 158: ......
Page 159: ......
Page 160: ......
Page 161: ......
Page 162: ......
Page 163: ......
Page 164: ......
Page 165: ......
Page 166: ......
Page 167: ......
Page 168: ......
Page 169: ......
Page 170: ......
Page 171: ......
Page 172: ......
Page 173: ......
Page 174: ......
Page 175: ......
Page 176: ......
Page 177: ......
Page 178: ......
Page 179: ......
Page 180: ......
Page 181: ......
Page 182: ......
Page 183: ...SPARE PARTS ILLUSTRATIONS AND LISTINGS FOR 7 1 HYDRAULIC ROTARY ATTACHMENT OPTIONAL EXTRA...
Page 192: ......
Page 193: ...APPENDIX A KUBOTA DIESEL ENGINE...
Page 194: ......
Page 195: ......
Page 196: ......
Page 197: ......
Page 198: ......
Page 199: ......
Page 200: ......
Page 201: ......
Page 202: ......
Page 203: ......
Page 204: ......
Page 205: ......
Page 206: ......
Page 207: ......
Page 208: ......
Page 209: ......
Page 210: ......
Page 211: ......
Page 212: ......
Page 213: ......
Page 214: ......
Page 215: ......
Page 216: ......
Page 217: ......
Page 218: ......
Page 219: ......
Page 220: ......
Page 221: ......
Page 222: ......
Page 223: ......
Page 224: ......
Page 225: ......
Page 226: ......
Page 227: ......
Page 228: ......
Page 229: ......
Page 230: ......
Page 231: ......
Page 232: ......
Page 233: ...APPENDIX B MESSERSI MINI TRANSPORTER...
Page 234: ......
Page 235: ...USE MAINTENANCE 03672872 MINITRANSPORTER TCH K722 N ______________...
Page 236: ...2...
Page 273: ...39 10 10 NOTES ON MAINTENANCE DATE WORK PERFORMED HOURS WORK PARTS INVOLVED...
Page 274: ......
Page 275: ...APPENDIX C TEST REPORTS...
Page 276: ......