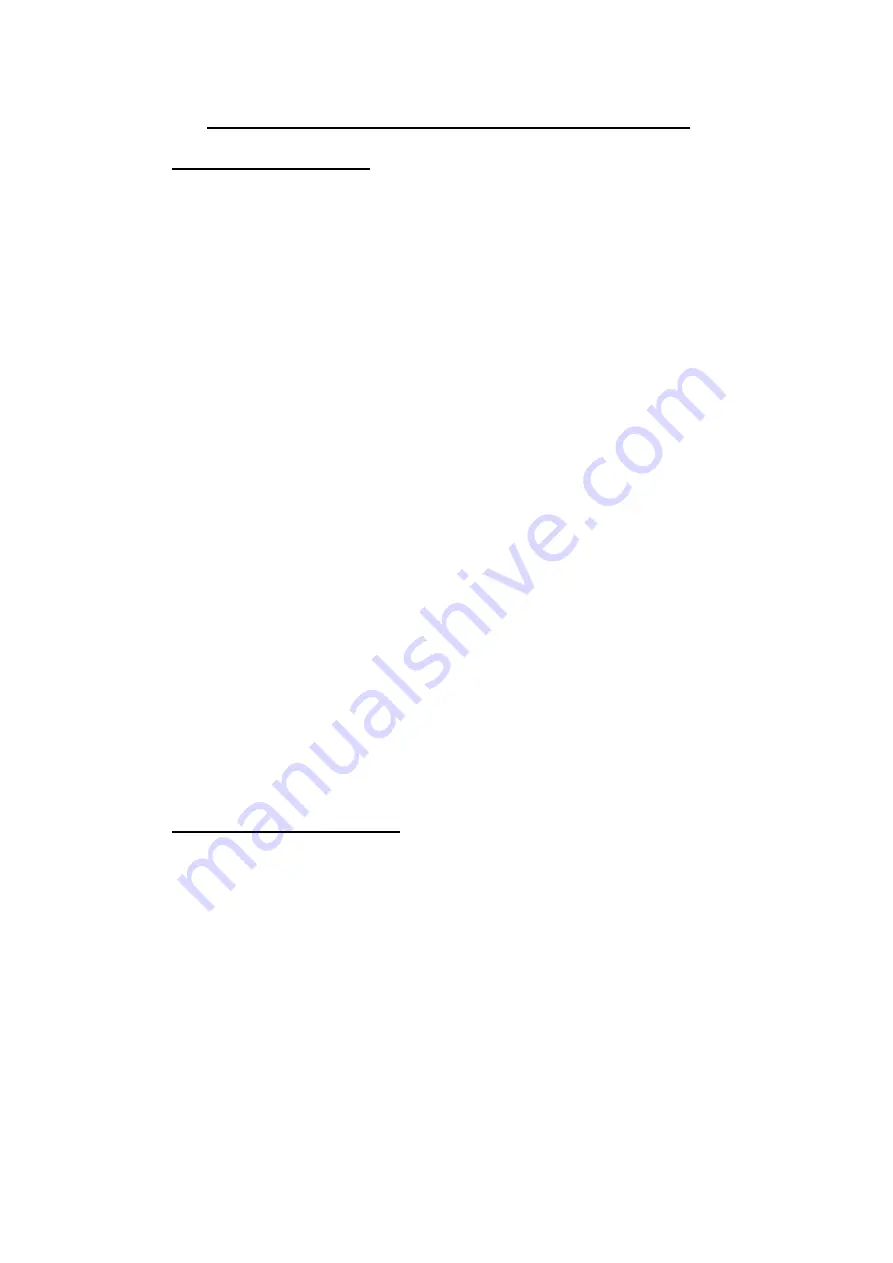
SECTION 4
– GUIDANCE FOR DRILLING APPLICATIONS
4.1
DRILL ROD HANDLING
To enable rotary drilling work to be carried out efficiently it is essential that all
practical steps should be taken to enable the drill rods to be handled as
easily and quickly as possible. It is recommended that particular attention
should be paid to the following points:
1)
The drill rod joints usually have wrench flats cut in to them. By placing
the wrench in position on these flats the rods are not only supported but also
locked ready for making or breaking the joints.
2)
The rods should be suitably positioned in front of the rig. Valuable time
can be saved by the provision of suitable stands, preferably with roller tops.
3)
It is advisable to keep the threads clean and coated with high pressure
tool joint grease.
Drill rods are connected and disconnected from the rotary drill head by
handling them to and from the horizontal in front of the rig.
The drill head itself is tilted by attaching the tilt wire to the hook provided on
the head as the carriage is being lowered. Continued downward movement
on the carriage will automatically tilt the head to the desired angle.
The drill rod box end can then be lifted and offered up to the driving pin, and
by rotating the head the joint will be screwed up. By raising the carriage
assembly, the drill rod will be lifted and the head will automatically swing
back allowing the tilt wire to be detached.
When handling the rod, the carriage assembly is quickly raised and lowered
by operation of the spring loaded Rapid Hoist/Feed Control Lever - No. 26.
4.2
D.T.H. HAMMER DRILLING
The main requirements for D.T.H. hammer drilling are slow speed rotation
and requisite feed control combined with accurate load control by operation
of the spring-loaded Hoist/Feed Control Lever
– No. 14.
The necessary slow speed rotation is obtained by moving the Holdback
Pressure Control - No.30 towards the DECREASE position.
The feed control must be set to suit the rate of penetration of the hammer
which will vary according to the type and hardness of the formation.
It is important that the load on the hammer should be maintained as
accurately as possible within the limits recommended by the manufacturer in
order to allow for efficient drilling. This load must be varied according to the
type of formation being penetrated and in hard formations it is possible to
judge from the size of the particles being ejected in the return air stream as to
whether the controls are correctly set.
Summary of Contents for TERRIER Mk 1
Page 2: ......
Page 3: ...SECTION 1 GENERAL...
Page 4: ......
Page 24: ...FIGURE 1 1 SAFETY WEDGE LOCATION...
Page 28: ......
Page 29: ...SECTION 2 TECHNICAL DATA...
Page 30: ......
Page 33: ...SECTION 3 OPERATING INSTRUCTIONS...
Page 34: ......
Page 37: ...FIGURE 3 2 VALVE CONTROLS A B C...
Page 44: ......
Page 45: ...SECTION 4 GUIDANCE FOR DRILLING APPLICATIONS...
Page 46: ......
Page 52: ......
Page 53: ...SECTION 5 RIG MAINTENANCE AND SERVICE...
Page 54: ......
Page 70: ......
Page 71: ...SECTION 6 SPARE PARTS ILLUSTRATIONS AND LISTINGS...
Page 72: ...23...
Page 74: ...25...
Page 76: ...27...
Page 78: ...29...
Page 80: ...31...
Page 82: ...33...
Page 84: ...35...
Page 86: ...37...
Page 88: ...39...
Page 90: ......
Page 91: ...SPARE PARTS ILLUSTRATIONS AND LISTINGS FOR UNDER CARRIAGE ENGINE...
Page 92: ......
Page 93: ......
Page 94: ......
Page 95: ......
Page 96: ......
Page 97: ......
Page 98: ......
Page 99: ......
Page 100: ......
Page 101: ......
Page 102: ......
Page 103: ......
Page 104: ......
Page 105: ......
Page 106: ......
Page 107: ......
Page 108: ......
Page 109: ......
Page 110: ......
Page 111: ......
Page 112: ......
Page 113: ......
Page 114: ......
Page 115: ......
Page 116: ......
Page 117: ......
Page 118: ......
Page 119: ......
Page 120: ......
Page 121: ......
Page 122: ......
Page 123: ......
Page 124: ......
Page 125: ......
Page 126: ......
Page 127: ......
Page 128: ......
Page 129: ......
Page 130: ......
Page 131: ......
Page 132: ......
Page 133: ......
Page 134: ......
Page 135: ......
Page 136: ......
Page 137: ......
Page 138: ......
Page 139: ......
Page 140: ......
Page 141: ......
Page 142: ......
Page 143: ......
Page 144: ......
Page 145: ......
Page 146: ......
Page 147: ......
Page 148: ......
Page 149: ......
Page 150: ......
Page 151: ......
Page 152: ......
Page 153: ......
Page 154: ......
Page 155: ......
Page 156: ......
Page 157: ......
Page 158: ......
Page 159: ......
Page 160: ......
Page 161: ......
Page 162: ......
Page 163: ......
Page 164: ......
Page 165: ......
Page 166: ......
Page 167: ......
Page 168: ......
Page 169: ......
Page 170: ......
Page 171: ......
Page 172: ......
Page 173: ......
Page 174: ......
Page 175: ......
Page 176: ......
Page 177: ......
Page 178: ......
Page 179: ......
Page 180: ......
Page 181: ......
Page 182: ......
Page 183: ...SPARE PARTS ILLUSTRATIONS AND LISTINGS FOR 7 1 HYDRAULIC ROTARY ATTACHMENT OPTIONAL EXTRA...
Page 192: ......
Page 193: ...APPENDIX A KUBOTA DIESEL ENGINE...
Page 194: ......
Page 195: ......
Page 196: ......
Page 197: ......
Page 198: ......
Page 199: ......
Page 200: ......
Page 201: ......
Page 202: ......
Page 203: ......
Page 204: ......
Page 205: ......
Page 206: ......
Page 207: ......
Page 208: ......
Page 209: ......
Page 210: ......
Page 211: ......
Page 212: ......
Page 213: ......
Page 214: ......
Page 215: ......
Page 216: ......
Page 217: ......
Page 218: ......
Page 219: ......
Page 220: ......
Page 221: ......
Page 222: ......
Page 223: ......
Page 224: ......
Page 225: ......
Page 226: ......
Page 227: ......
Page 228: ......
Page 229: ......
Page 230: ......
Page 231: ......
Page 232: ......
Page 233: ...APPENDIX B MESSERSI MINI TRANSPORTER...
Page 234: ......
Page 235: ...USE MAINTENANCE 03672872 MINITRANSPORTER TCH K722 N ______________...
Page 236: ...2...
Page 273: ...39 10 10 NOTES ON MAINTENANCE DATE WORK PERFORMED HOURS WORK PARTS INVOLVED...
Page 274: ......
Page 275: ...APPENDIX C TEST REPORTS...
Page 276: ......